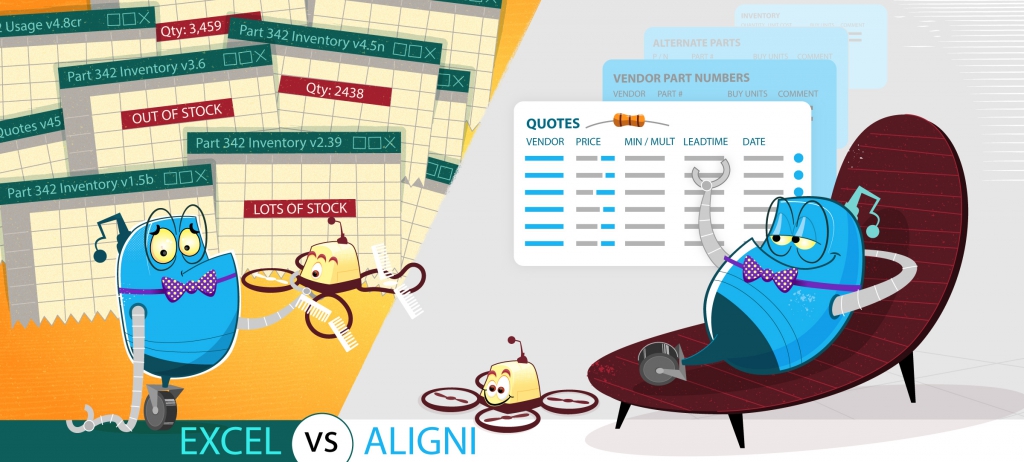
In the day-to-day and over the long term, a manufacturing company manages a large amount of data and communication regarding the parts and materials it uses to make its products. Using a centrally-located database system is almost a necessity for multiple departments, as well as the company as a whole. For companies that have moved past home-grown spreadsheet tracking processes, the item master is the central core of product information and inventory management for Product Lifecycle Management (PLM) and Material Resource Planning (MRP) software suites.
These item master databases allow companies to easily track, organize, and update everything that goes into physical products being made. Typically, the item master includes material items kept in inventory like resistors, capacitors, hardware, brackets, and batteries as well as the communications that go into sourcing them. Companies also may track non-material items such as NRE fees, shipping costs, labor costs, and test procedure documentation. More advanced implementations of an item master database may log abstract representations of data. This could include firmware and source code references. Some systems and companies also use these databases to manage capital assets such as test equipment for inventory tracking, calibration records, and depreciation.
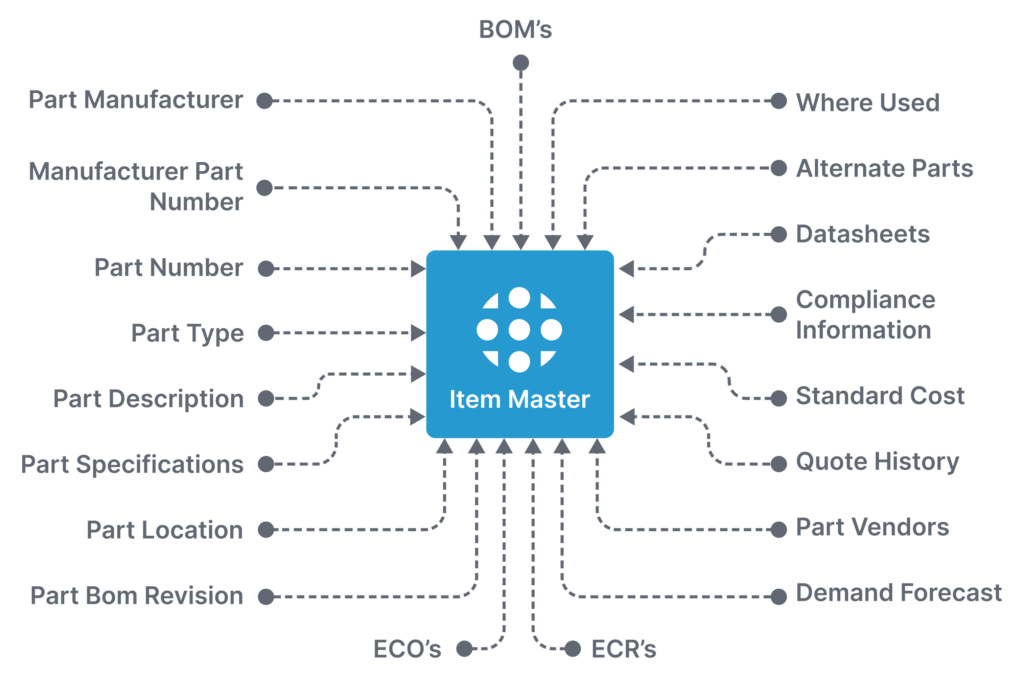
Once all this data is stored within the item master, it must be designed to be easily managed and shared with other departments in the organization. It is this aspect where using management software designed around an item master database creates numerous rewards.
Benefits of Centralized Data
The item master database provides a single source of truth from the product development process to the serial manufacture of products and beyond. Using this single location to store and operate on inventory data provides several advantages over the distribution of important data across multiple spreadsheets and even multiple computer systems.
A single, shared data location means everyone works off of the same data. By extension, the company works off the same revision level of data. Trying to achieve this with spreadsheets may be all but impossible.
While spreadsheets can be shared from a central server, typically these files (or derivatives of them) end up being saved locally on employee’s own systems where changes are made to local files rather than shared versions. Initially, the local versions may just be made for convenience or perhaps experimentation but once the copies proliferate within different divisions and get pressed into use, who has the most recent data? Who is responsible for reconciling the truth?
When it comes to revisions, spreadsheets also don’t contain the same level of revision tracking as item master-based systems do. That means values are changed in the file with no information on when, why or even by how much. It becomes almost impossible to analyze the change. Questions and doubts remain. Was it the correct change? If it wasn’t correct, how long has it been wrong?
Another benefit of centralized data is the process to make sure that data is secure and backed up properly becomes significantly less challenging. When data isn’t held in the same location, it’s spread across computer systems across the company. It’s on workers’ laptops, mobile devices, email accounts, and shared drives. Every new location increases the opportunity for data loss or corruption: a mobile device left in a cab, a laptop bathed in coffee, a power surge on the shop floor, or something else completely unplanned. A company may not lose all its data. It might lose an irreplaceable component of it. Once the data is distributed, the IT department’s backup strategy turns into an expensive game of whack-a-mole where there can be no winner.
More Efficient Workflows
The collaborative capabilities of a shared item master means reduced data silos in an organization. It also provides faster decision-making and execution. Different departments can work together within the item master and surrounding functions with shared access rather than constrained within functional groups or waiting for data from others.
Purchases and quotes can be managed in the item master instead of individual email accounts. Managing the purchasing process doesn’t mean sifting through email chains between buyers and vendors. These interactions can be stored and sorted more efficiently when saved within the item master database. It also makes it easy for others in the organization to understand the changes and adjustments to the order. The item master makes it possible to take over the conversation when necessary. When this information concerns a large number of products or requires difficult or complex negotiations, the time savings from being able to easily access and search what may be hundreds to thousands of emails may justify the move to an item master-based system by itself.
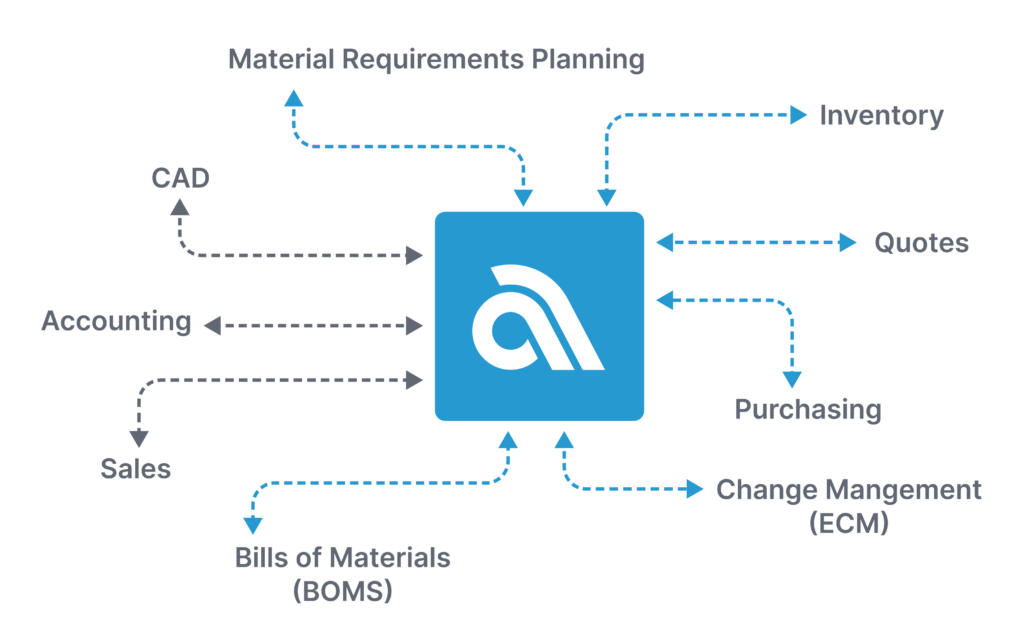
A centrally-located dataset means departments can independently use shared data contained within the item master for their own needs. A PLM or MRP system typically provides specialized access to multiple departments in a manufacturing operation. These access points are designed to provide relevant information. They also provide an interface that’s natural and efficient for each user. Inventory changes are recorded within the item master and groups beyond purchasing are kept up to date on changes in the organization.
This independent access helps increase the overall efficiency and effectiveness of an organization. It can reduce the need for status update meetings, tracking down information from other employees or worse: not finding out changes have been made.
Providing Operational intelligence
Item master-based systems let companies know where profitability stands at any moment. These systems provide a one stop shop for analyzing current part usage and costs. Parts consumed in production and on-hand amounts can be given values or assigned to product sales immediately. This is instead of contacting several departments to collect independently managed data to do so.
Confidence in centralized part and material data can reduce costs and lead times. This is especially true at the beginning of the product development and manufacturing process. Unnecessary sourcing operations can be reduced by encouraging engineers to choose parts that are broadly stocked and available from multiple sources. This can be done by searching the item master first. Manufacturing and planning teams can better understand part availability and make adjustments to production schedules through the item master. The inventory knowledge could be used to avoid downtime on the floor.
Firms can use archived data from the item master to be more predictive of future needs and sidestep sourcing issues. MRP item master systems provide much easier manipulation of historical purchasing data to find trends and potential issues. Forecasting sales order needs from previous jobs is easier with a purpose-built database rather than managing increasingly complex spreadsheets that become buggy with age and use. Developing insights from combined data from production and supply chain is far easier when that data is housed in one database.
Bringing it All Together
While these are only a few of the areas that could benefit, using an item master approach to part management is necessary to develop a highly efficient and profitable manufacturing operation. The benefits become obvious when compared to relying on a collection of spreadsheets dispersed across multiple departments. The flexibility, collaborative aspects, and speed combined with data security in using MRP or PLM software that have item master databases at their core are factors modern organizations will have a hard time being competitive without.
If you’re ready to move to a more reliable and efficient item master-based inventory management system, it’s time to move to Aligni. Sign up online today
Start your 30-day free trial
Helping You Make Great Things…Better.