For many, PDM, PLM and MRP software suites may seem like competing systems. It’s not hard to come to that conclusion, either. Afterall, there’s a lot of functionality overlap between them. The fact is these systems, when executed properly, are designed to work together to help manage product information and streamline a company’s workflow.
Let’s walk through where each system fits within a tool chain that goes from new product development to manufacturing the product. While many of these systems have features that others have, we’ve focused on where the core strengths of each are in this process.
In general, the workflow between PDM (Product Data Management), PLM (Product Lifecycle Management), and MRP (Materials Requirements Planning) systems in product manufacturing involves a sequence of activities and data flows that enable organizations to efficiently manage product data, processes, and resources throughout the product lifecycle. Below is a high-level overview of the workflow, from new product introduction to production management operations:
1. Product Design: The product design process typically starts with PDM. It is used to manage and control engineering data, such as CAD files, drawings, and specifications. PDM systems are typically integrated with design software to provide tools for version control, change management, and collaboration among product engineering members. It must be noted that for companies whose products include both electrical and mechanical design, this might require two PDM systems for each sort of design software due to how tightly integrated they are to specific CAD suites.
2. Product Development: As the product design evolves, PLM becomes the primary system for managing the entire product lifecycle. It manages the product definition, bills of material (BOMs), documentation, change management, and collaboration among cross-functional teams. These groups include engineering, manufacturing, quality, and supply chain management.
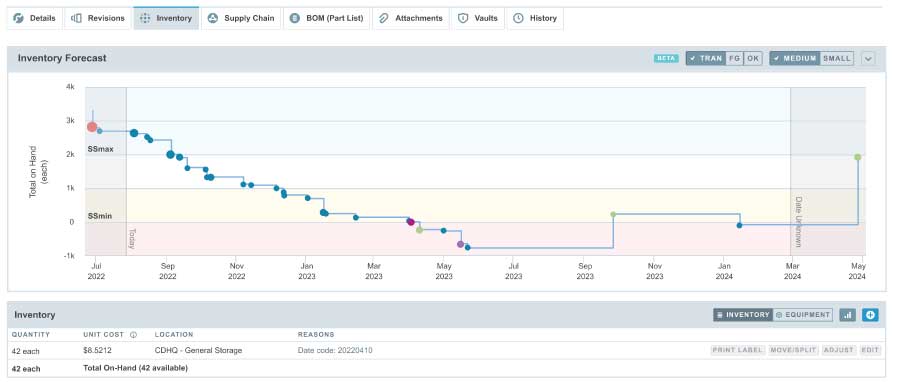
3. Materials Planning: As the product transitions to production intent, MRP systems are used to manage the materials required for manufacturing the product. This suite oversees raw materials, components, and subassemblies. MRP systems use a combination of inventory data, production schedules, and demand forecasts to generate material requirements plans. These plans specify the quantities and timing of materials needed to meet production goals.
4. Production Scheduling: Once the material requirements have been determined, MRP systems can be used to generate production schedules. They specify the timing and sequencing of production activities, including procurement, production, and assembly. PLM systems may also provide tools for managing the production process, such as work instructions, process workflows, and quality inspections.
5. Manufacturing Execution: Once production has started, MRP systems can be used to track the progress of production activities and manage inventory levels in real time. During production PLM systems are used to manage changes to product designs or manufacturing processes that may arise during production.
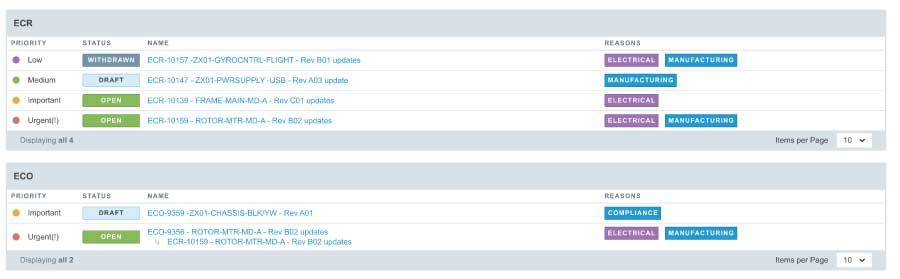
6. Quality Control: PLM and MRP systems can be used to manage quality control activities throughout the product lifecycle, including design reviews, process inspections, and product testing. Quality data can be captured and tracked in PLM and MRP systems, which can be used to identify and resolve quality issues.
The overview above is designed to serve as a general outline of how these systems work together and where their strengths are. For many companies, their needs will work as a guide to which of these software suites they’ll adopt first. The aforementioned functionality overlap usually helps lead firms in the direction of what will be most important to implement next. Eventually, the more successful small and medium sized businesses will arrive at an integrated suite we’ve put forth.
If you’re looking to get started on more efficiently running your production operations, it’s time to start thinking about Aligni PLM and Aligni MRP. Sign up online today!
Start your 30-day free trial
Helping You Make Great Things…Better.