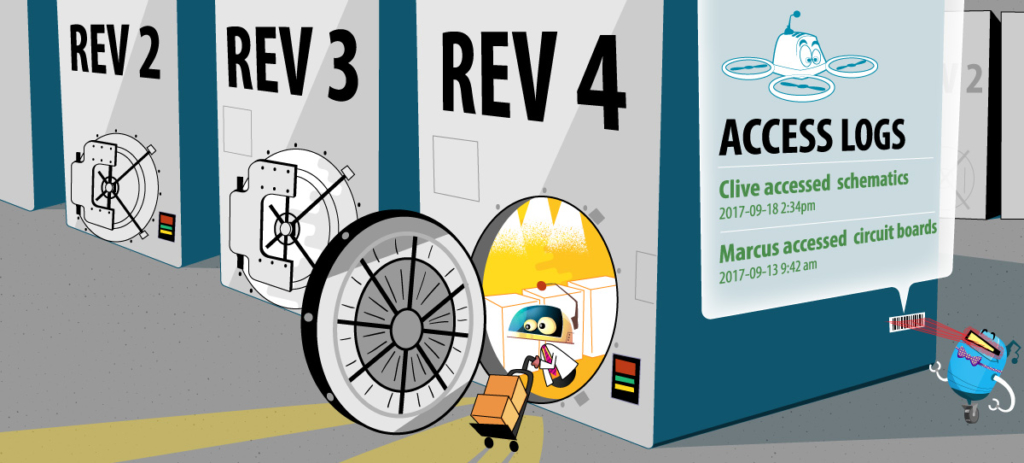
Software engineers have broadly embraced Source Code Management (SCM) systems such as Git, Subversion, and Perforce as best practices. Hardware projects don’t need to be treated differently. They just need the hardware project equivalent to SCM. For managing tangible parts and materials, that solution is Product Lifecycle Management (PLM) software.
PLM performs operations for hardware similar to what SCM does for software development. This includes managing the intricacies of component information, availability, and quality, then affixing those details to products being designed and built. We’ve outlined four areas where hardware projects are managed in the same fashion as software projects and why it’s of even greater importance to use purpose-built part management software like PLM for that management.
Staying on Top of Component Dependencies
Software products today include a long list of dependencies. These dependencies and their handling are very important to software lifecycle management and strong software organizations manage them accordingly.
Hardware products have similar dependencies in the components that they use. Each of the components have their own lifecycle supported by its respective manufacturer. The hardware PLM item master is where this is maintained.
Keeping Track of and Implementing Component Updates
Software products are updated with an endless stream of commits, merge requests (a.k.a. pull requests for git users), and reviews from collaborators. These actions help to keep the software project current in both the components and tracking those changes in case issues arise.
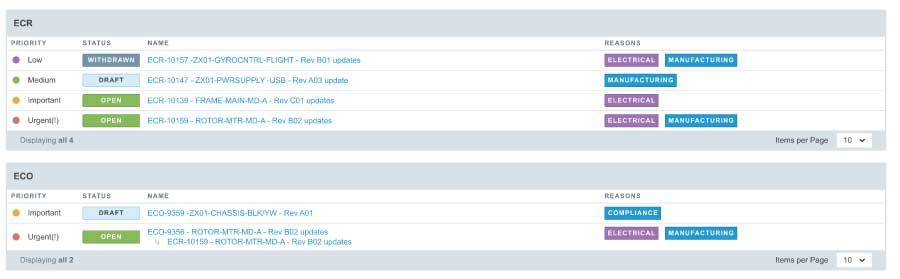
Using a PLM system, hardware products are similarly maintained by Engineering Change Request (ECR) and Engineering Change Order (ECO) processes. These processes alert the relevant departments to changes in part quality, availability, and performance. The ECR and ECO process combined within Engineering Change Management (ECM) make sure that updates to the selected parts occur, and that design documentation is updated with the necessary information. All these changes and updates are stored within the PLM system to maintain a record that can be reviewed when necessary.
Managing Product Deployment
Software products are deployed by packagers that collect the assets into a bundle and distribute to customers or deploy to server platforms. Packagers assure that all of the required assets are neatly organized and accounted for so that the systems can be deployed and updated with consistency and integrity.
Hardware designs are instead deployed to production floors and contract manufacturers. Delivering the necessary information on what goes into the product build is managed with part “data vaults” in a PLM system. Strict controls such as ISO 9001:2015 assure quality in the manufacturing of hardware and are facilitated by product lifecycle management systems. Both quality aspects and part and material specifications are packaged together to make sure the correct information is transmitted to the manufacturing process.
Bringing it All Together
Product management tools are available for both software and hardware environments. Using these tools provides a strong influence on the productivity and efficiency of the team as well as the quality of the end product. While there are similarities between software and hardware-based product management, hardware updates are subject to more extensive rigor, scrutiny, and review because the stakes are higher. That means hardware systems require even higher levels of oversight than software projects. This difference all but requires the use of specialized software like Aligni PLM to make sure proper management is available for tangible products.
If you’re looking to get the same level of oversight and control over your hardware products as you do with the software side, it’s time to sign up for Aligni’s PLM!
Start your 30-day free trial
Helping You Make Great Things…Better.