A Buyer/Planner has to manage two important aspects of the manufacturing process: purchasing and production scheduling. At larger companies, these operations are done by at least two people, full time. That means the person doing both has to pay greater attention to a variety of aspects or they need to have far better tools to manage both at the same time.
Aligni is that tool that can provide the visibility and oversight to effectively manage both the buying and production planning process. Our software provides the functionalities that a buyer/planner needs to be successful in a highly integrated manner that reduces the complexity of the role and increases its efficiency in the process. To illustrate, we’ll walk you through how a buyer/planner would perform their role using Aligni.
Starting the Production Procurement Process
It all begins at the process of turning the sales orders into production builds. Aligni’s interconnectedness with a product’s Bill of Materials (BOM) helps streamline setting up a production build by directly connecting the BOM to the build – and without leaving the system to do it.
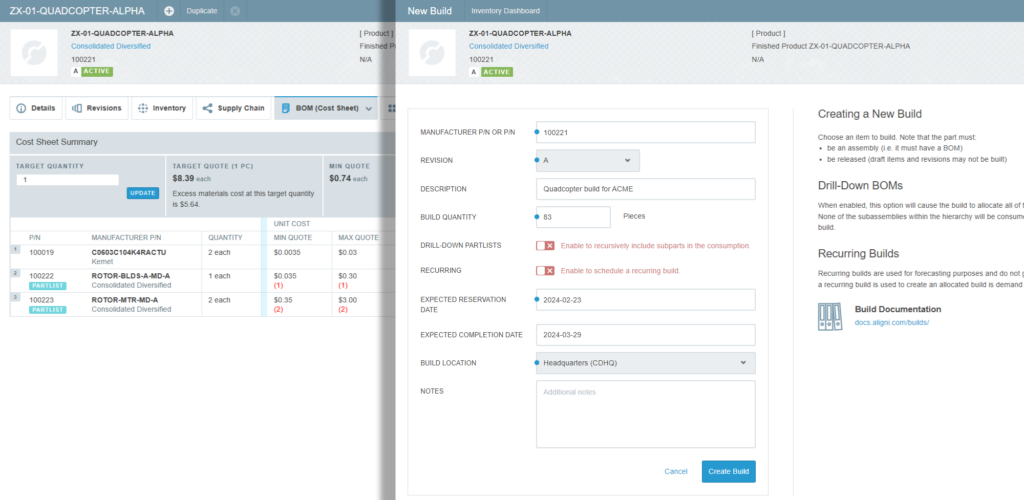
When production scheduling and inventory management are collocated within one system, seeing what parts and materials are necessary is that much easier. Aligni takes quantities of inventories on hand and automatically applies these values to the materials required by the build. The interconnection between build requirements and inventory on-hand provides the buyer/planner an immediate understanding of what’s needed for the production run being scheduled. This is available through the build’s Item List screen. Once the buyer/planner is aware of the current inventory situation for the build, they can begin to determine their next steps.
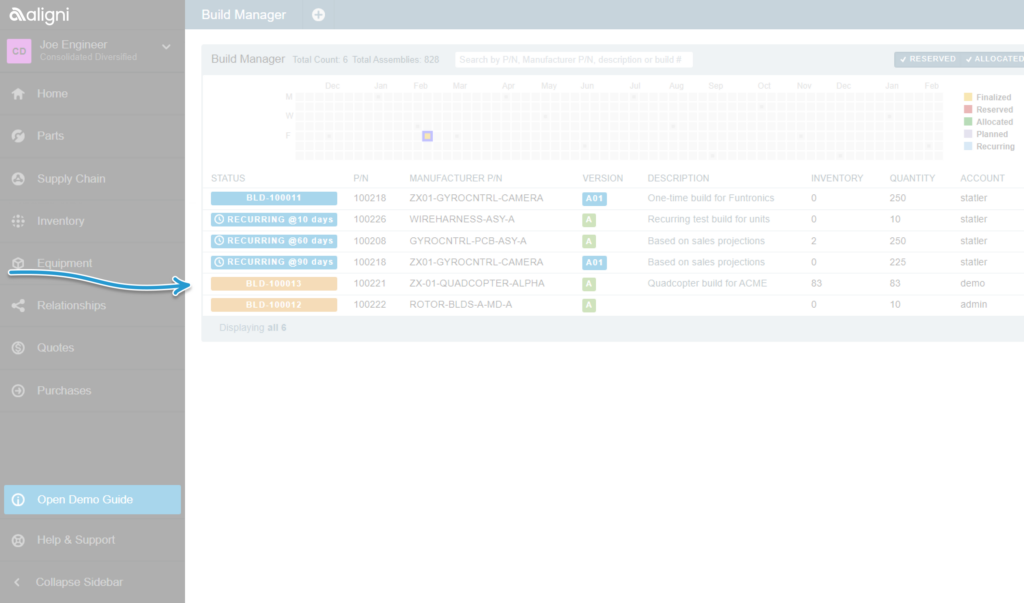
For instance, if the build has all of the materials necessary, then there’s no need for further action and the build can be scheduled for production. But if there is a shortage of materials for the job, then the buyer/planner needs to engage the purchasing aspects of their role and consider where to put the job on the production calendar.
Balancing Production with Better Scheduling
The twin goals of production planning are to make sure manufacturing operations are running as efficiently as possible and builds are completed in time to meet order delivery requirements. That means actively avoiding downtime while making sure those operations are not overbooked – all without creating shipping delays.
Aligni helps buyer/planners achieve the best possible production efficiency by helping understand how these builds are scheduled over time. The Build Matrix on the Build Manager screen displays all planned, allocated and reserved builds in the system. This screen is updated immediately as conditions change, including inventory changes or changes to the build itself.
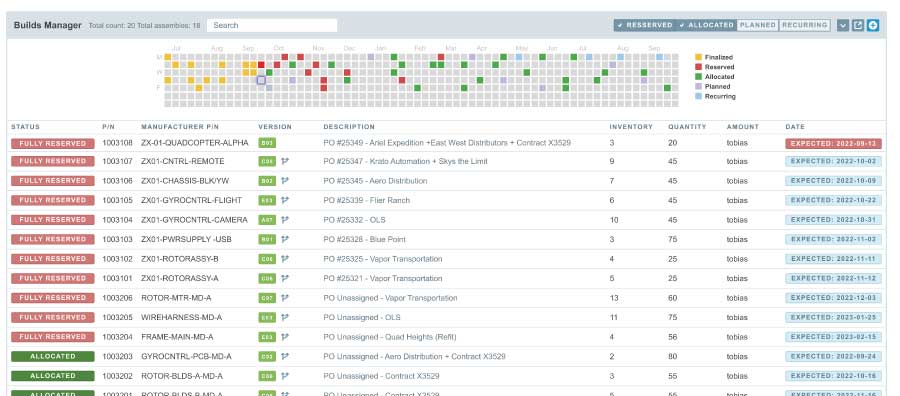
To balance production loads, buyer/planners can use the Build Matrix to identify where best to place new builds to fill underutilized times and dates. These low spots are easier to locate graphically than through tabular data alone. Builds experiencing delays or shortages can be moved to open times without doubling up production resources. The data for each build will be updated automatically.
Collating build information and production scheduling over a longer-term view provides benefits that are difficult to match with spreadsheets or combinations of apps. It helps buyer/planners capitalize on underutilized resources and reduce overtime needs by more efficiently spreading builds across time.
Supporting Builds with Integrated Purchasing
When it becomes necessary to purchase more parts, Aligni’s integrated platform provides greater efficiency than going it alone with spreadsheets and emails. Aligni’s inventory management capabilities also blend into purchasing operations and provides next-level continuity to the entire process.
The buyer/planner can move directly from a report on part shortages into more information on the parts themselves. More importantly, Aligni connects those parts to the organization’s preferred vendors that carry them, and potential alternates approved for substitution. These can be found by clicking on the part in question and going to its details tab.
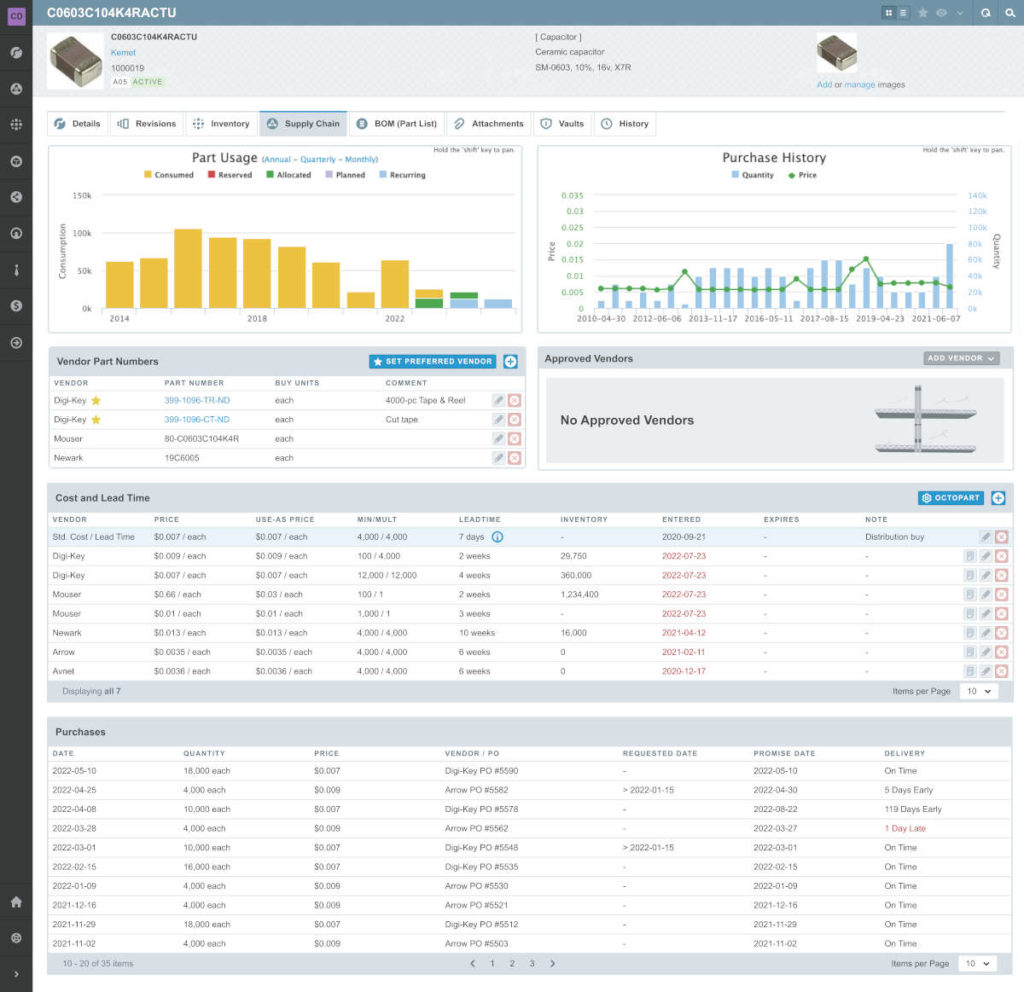
Aligni also reports on whether there are replenishing orders already in place and their predicted arrival times. When a new order needs to be placed, Aligni reports on the estimated lead times from each vendor. The buyer/planner can easily find this information in a variety of locations within the application, including the Aligni Material Shortage Report. This chart shows builds and the condition of the inventory needed.
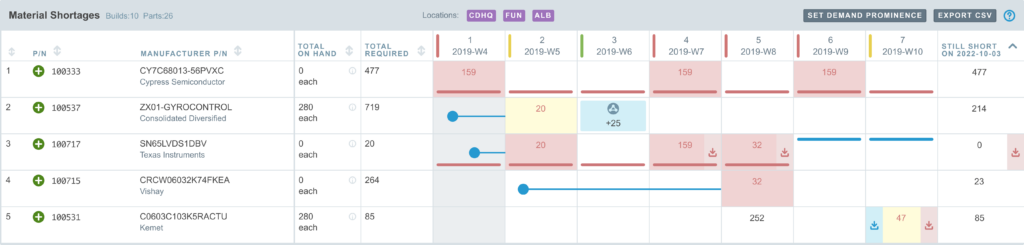
When more parts need to be ordered, once again Aligni’s integrated systems help support the buyer/planner. When they go through Aligni’s Vendor Portal to manage the RFQ and PO process, buyer/planners find several benefits that help reduce errors and complexity. When materials need to be purchased, the buyer/planner can transfer what’s needed from the build directly to the RFQ or PO they intend to send to vendors already in the system. This reduces translation errors between systems, spreadsheets or emails, ensuring the right parts in the right quantities are ordered for the build.
Since the RFQs and POs are sent digitally from within Aligni, it reduces communication time. The Vendor Portal allows vendors to upload their information directly to Aligni, further reducing order time. These processes can all be managed through the company’s Vendor Portal screen.
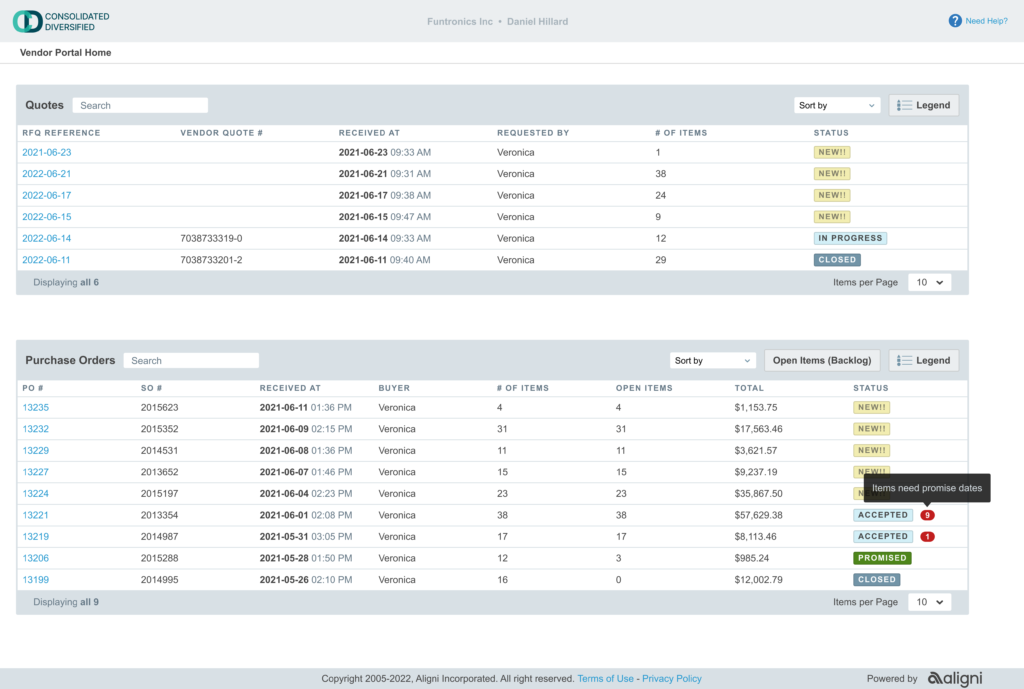
Buyer/planners can be alerted to this data’s arrival as well as other updates from the vendor, including changes to delivery times or product availability. The rest of the Aligni system is also updated with new vendor information, making sure every screen is current, and buyer/planners are working with the latest data.
Making Better Decisions with Combined Data
The Aligni Material Shortage Report can also be a buyer/planner’s main dashboard when it comes to readiness to build. Here, they can quickly scan upcoming builds and understand their inventory states, whether new part orders are on the way to cover shortfalls or if certain jobs are unable to be done. Buyer/planners can take action to change these states before line down situations occur by putting in needed orders if the lead times are available or potentially moving builds out until materials arrive to complete the process.
For the jobs that do not have enough materials on-hand, the buyer/planner can quickly ascertain whether parts can be brought in fast enough to hit build dates by checking the Inventory Forecast for the items in question. If they cannot, the buyer/planner can check Aligni to determine if there are substitutes available or other approved vendors to source from instead before returning to move production times or contact sales to push delivery times. All of these steps are just a few clicks away within Aligni.
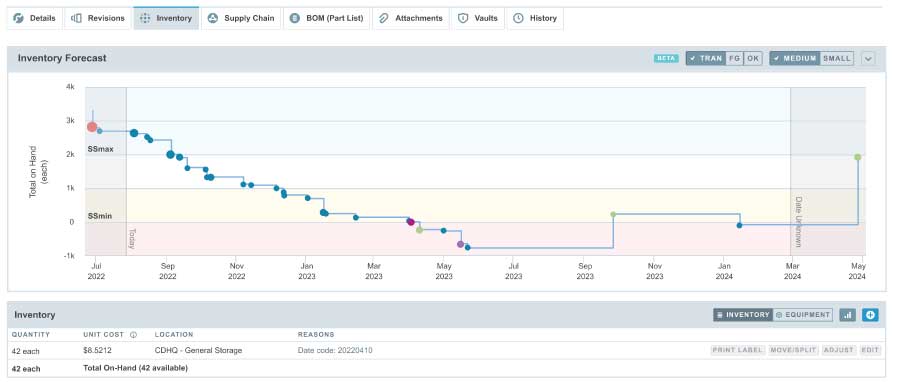
Puttint it all Together with Aligni
Just as organizations can see substantial benefit to combining the roles of buyer with production planner, so can they see significant advantages from migrating to an integrated system that brings together product data management, inventory management, purchasing operations and production management. With Aligni MRP, a company reaps the benefits of collocating their information as well as their most important business processes. They also make the role of buyer/planner much more productive and efficient.
If your buyer/planner is drowning in spreadsheets and emails, don’t wait for trouble to happen. Migrate to Aligni MRP today!