Optimize Procurement Decisions
Turn part-level insights into smarter buys—linking past orders, current needs, and vendor performance in one place.
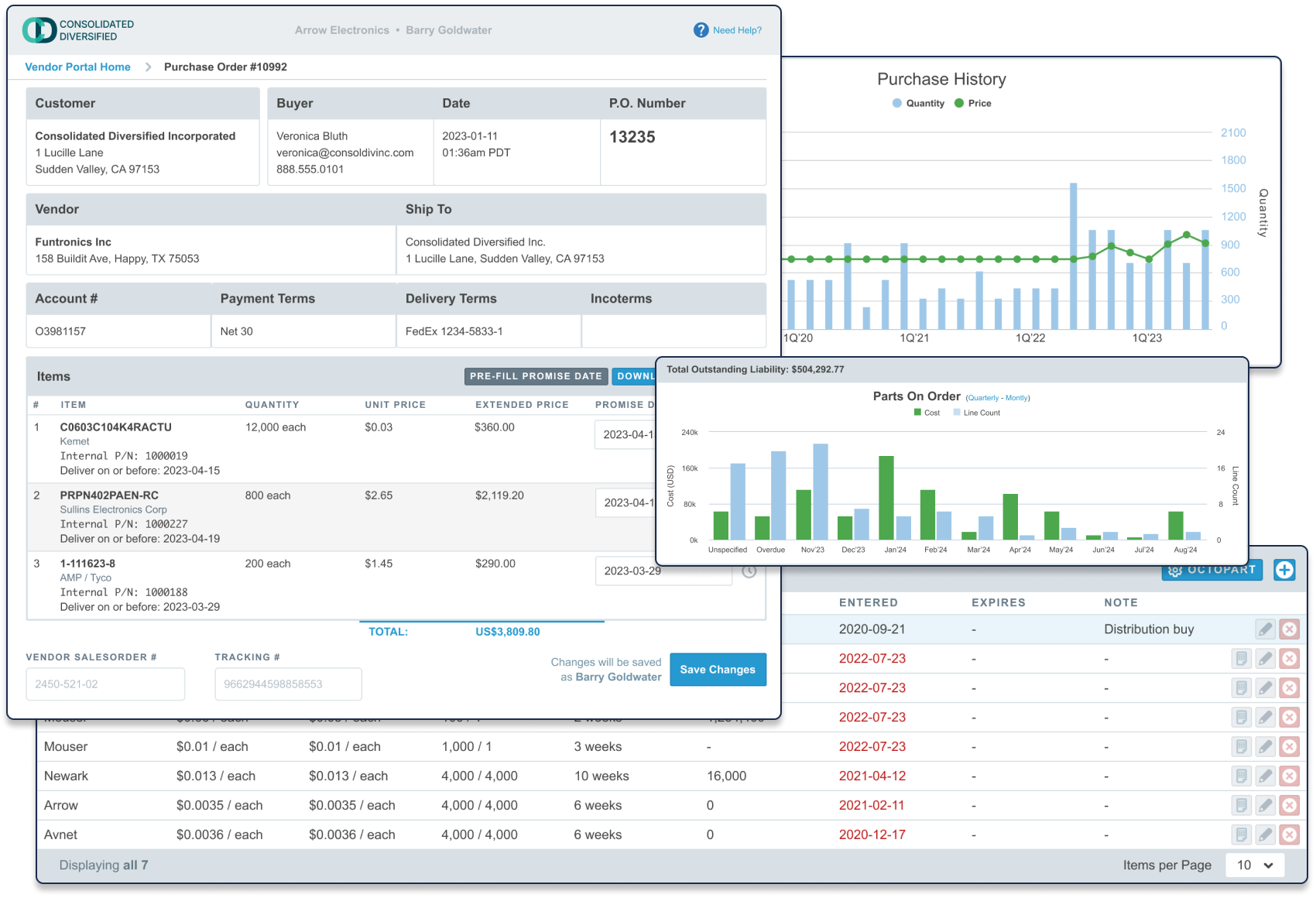
Integrated Quoting and Purchasing
Start where the data lives. Aligni’s item master is your direct line from part to purchase.
- Build and issue RFQs or POs from BOMs, shortage reports, or builds
- Leverage historical orders and vendor terms—automatically pulled in
- Keep every purchase tied to demand and inventory outlook
- GPT: Reduce costly errors and eliminate double-entry workflows
- Email vendors directly from Aligni. Keep quotes in Aligni.
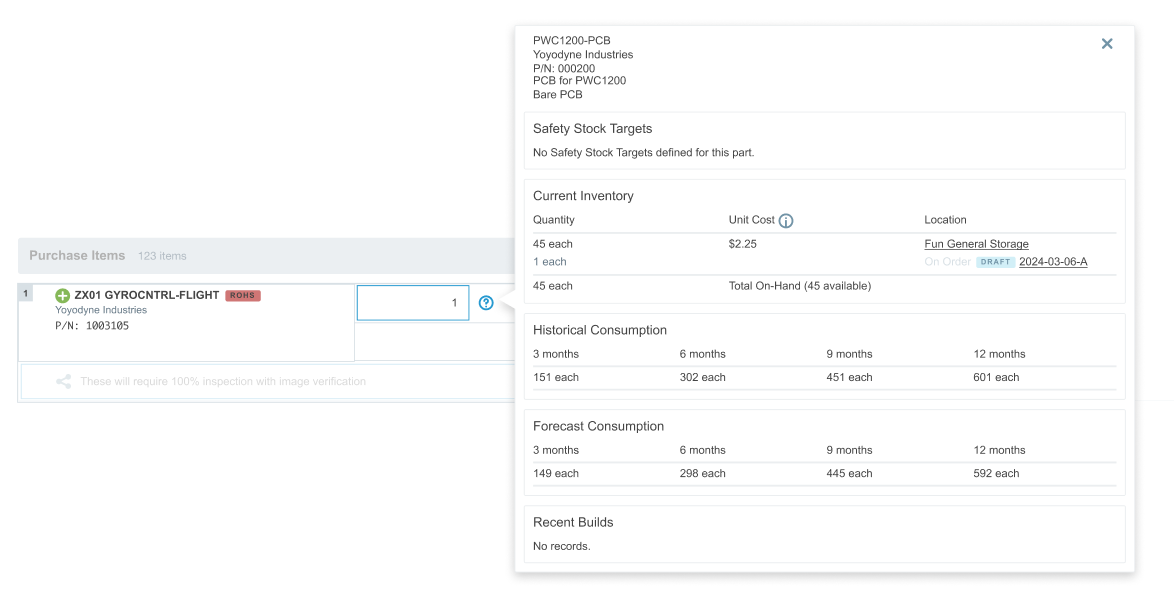
Let Shortages Drive the Action
Aligni’s Material Shortage Report (MSR) ensures you’re always buying what matters most.
- Know exactly what to order, when to order it, and why it matters
- Get instant visibility into inventory levels, inbound parts, and projected gaps
- Prioritize by urgency, lead time, or build impact—no guesswork required
Stop chasing parts. Start driving decisions.
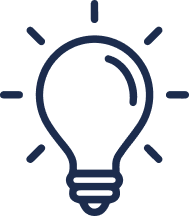
Challenges in Procurement for Manufacturing
Procurement is the process of buying the parts and materials needed to build your product. It’s where plans turn into purchase orders—sourcing the right parts, from the right suppliers, at the right time.
In Aligni, procurement is tightly connected to what’s happening in your BOMs, inventory, and production plans—so you’re always buying based on real needs, not guesswork.
Make Smarter Buys with Helpers
You can’t remember the history of every part—and you shouldn’t have to. Aligni gives you a 360º view of each item as you work, surfacing the right data at the right time to support confident decisions.
- Recent Price & Quantity: Quickly review order history for better context
- Vendor Quotes: Compare price, lead time, and availability in seconds
- Upcoming Demand: Anticipate future needs beyond today’s build
- Inventory: Confirm on-hand inventory to prevent overstock
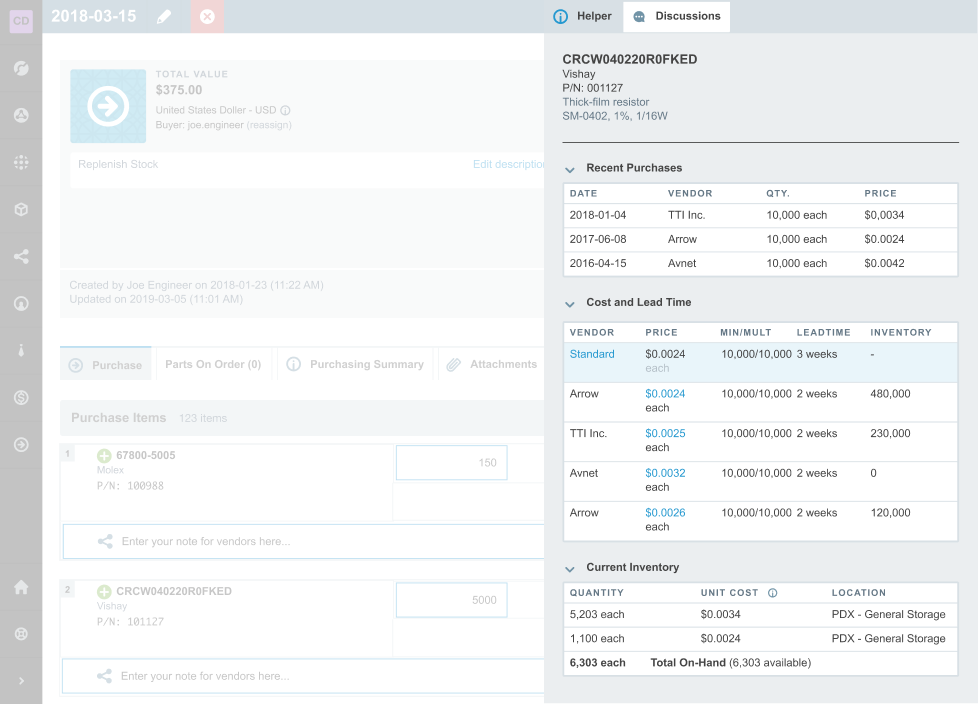
Work With Vendors, Not Around Them
Communicate more effectively with vendors without the “Inbox Overload”. Aligni’s centralized vendor portal gives suppliers direct access to what matters:
- Share RFQs and POs through a simple, no-login-required portal.
- Vendors update pricing, lead times, and delivery promises directly.
- Every action is tracked with full visibility and audit logs.
Easy for vendors. Powerful for your team.
Keep Delivery Dates Accurate and Actionable
Track and maintain delivery commitments with confidence, so production stays on schedule.
- Vendors update promise dates directly in Aligni
- Inventory forecasts update across your procurement and production views if delivery dates shift
- Every update is visible to your team—no delays, no confusion
Accurate delivery dates mean fewer surprises and smoother builds.
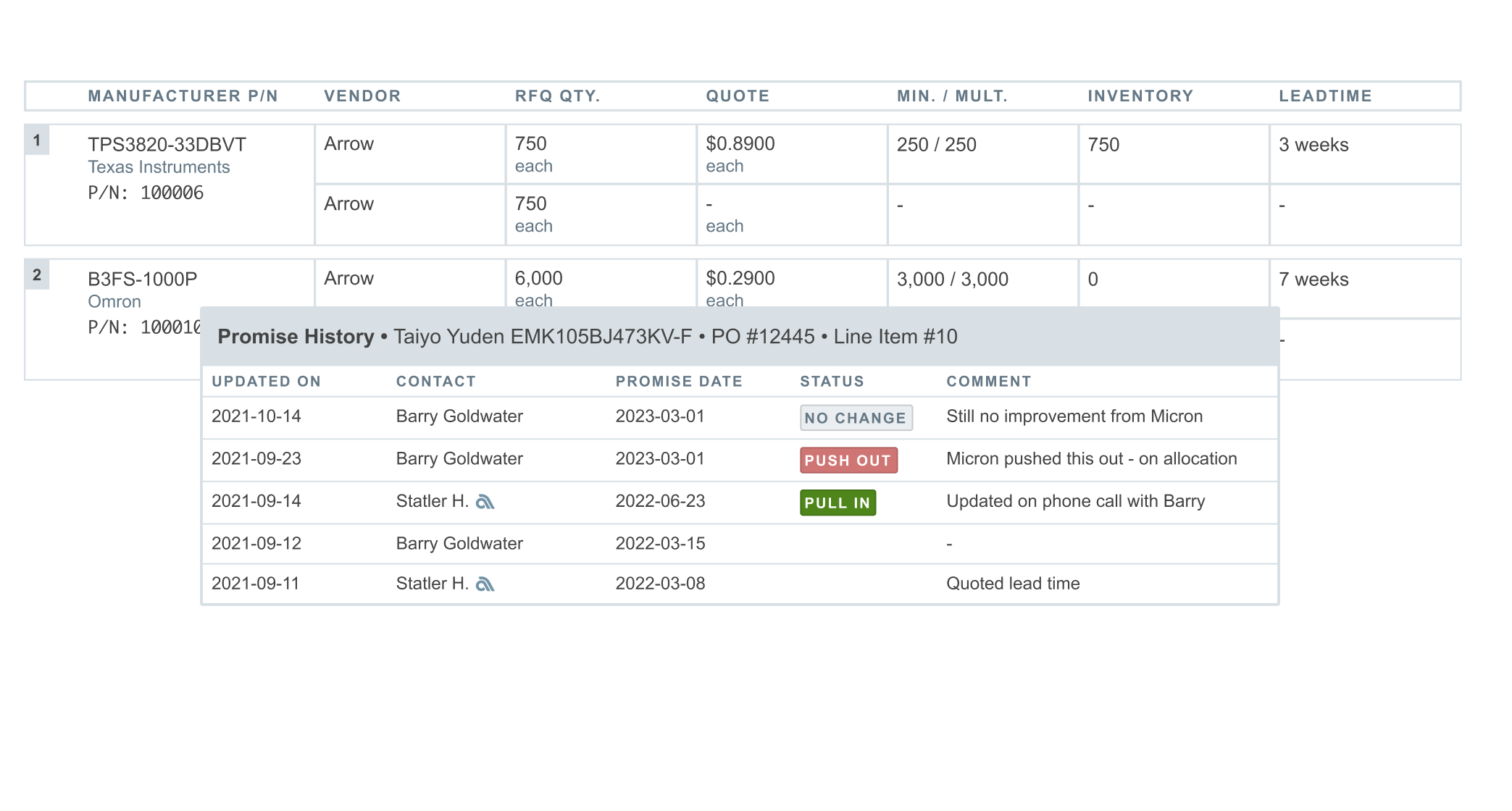
Secure, Searchable, Always Up to Date
Share specs, drawings, and inspection criteria with confidence — Vaults keep your documentation protected, accessible, and current.
- Pulls live up-to-date data from Aligni’s item master
- Role-based access and audit trails keep sensitive info protected
- Get notified when vendors view or download attachments
- Automatically notify vendors if content changes
Better Buys. Fewer Delays.
Procurement doesn’t have to be slow or reactive. Aligni connects purchasing to what’s actually happening in your inventory and production schedule—so your team always knows what to buy, when to buy it, and who to buy it from.
No spreadsheets. No second-guessing. Just better decisions, faster.
Start your 30-day free trial
Helping You Make Great Things…Better.