Smart planning tools. Smarter production.
Forecast demand, manage supply swings, and prevent material surprises so production stays on track and inventory stays under control.
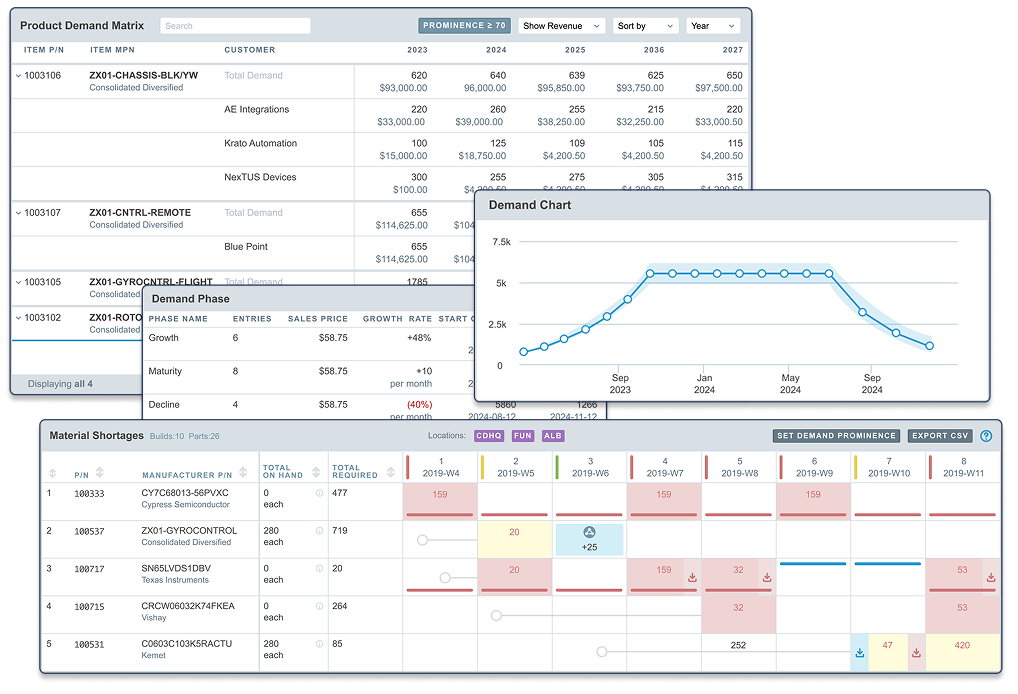
Build Your Own Oracle
See further. Plan faster. Adjust earlier.
Aligni gives you long-range visibility into part availability, shortages, and demand—all connected to your BOMs, builds, and supplier activity.
Tools like demand estimation, lead-time visualization, and inventory forecasting help you stay ahead of supply issues before they hit production.
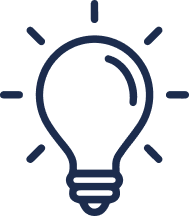
What is Material Planning?
Material planning ensures you have the right parts at the right time to meet production demand—without overstocking or missing deadlines.
In Aligni, material planning connects your forecasts, BOMs, builds, and supplier activity into a single, traceable workflow—so you always know what to buy, when to buy it, and how each decision affects the bigger picture.
Keep Production Flowing
Built-in world-class inventory management tools such as the material shortage report and inventory outlook offer a real-time pulse of your inventory health.
- Plot on-hand, inbound, and consumed inventory across time
- Spot shortages before they impact production
- Project stock levels across warehouses and builds
- Account for safety stock and long lead times
- Explore alternative scenarios with TimeWarp™
From Demand to Done
Turn material planning into a connected, step-by-step workflow. Aligni brings every piece of the planning puzzle into one coordinated process—tracking demand, builds, quotes, purchases, and inventory movements from start to finish. What used to be siloed and reactive becomes predictable, traceable, and repeatable. As conditions change, your workflow updates automatically—so you always stay one step ahead.
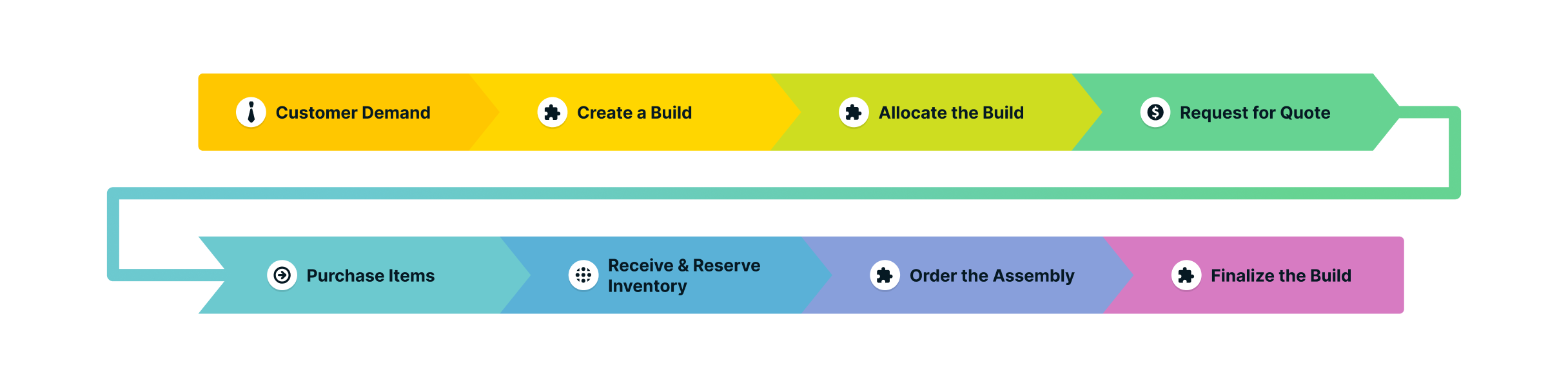
Demand-Driven Production
Know what’s coming—even before it’s ordered. Aligni’s demand estimator models expected material needs based on:
- Customer Buys: Feed in customer forecasts to project demand
- Flow Demand: Account for routine builds and replenishment cycles
- Component Planning: Share demand signals upstream with suppliers
Forecast smarter. Buy smarter. Build smarter.
Gain Insight from Every Shortage Signal
Aligni’s interactive material shortage report is designed to help you focus on what needs your attention the most and perform efficient procurement.
- Prioritize Shortages: Focus on what blocks production
- Lead-Time Visibility: Adjust sooner when delays hit critical components
- Track Incoming: Factor in expected deliveries and promise dates
- Respect Safety Stock: Maintain buffers without overbuying
- Procurement Integration: Add items directly from the shortage list to POs
With Aligni, shortages become signals — not surprises.
Expedite the Evaluation
Evaluating business software shouldn’t take months. Aligni makes it simple to go from login to live results — no complex setup, no IT support required.
- Test drive a live demo and experience Aligni’s workflows right away. Invite colleagues, load real data, and see how it fits your operations.
- Start a 30-day free trial with free onboarding to get your team moving fast. Importing services are available to help you hit the ground running.
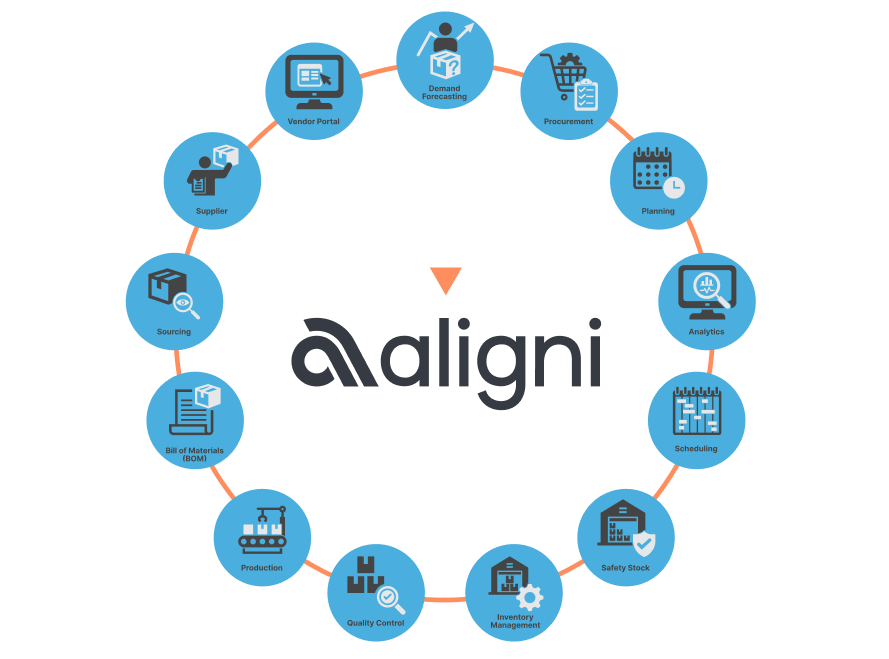