Keep Production on Track
Connect your BOMs to builds, usage, and costs—keeping your production schedules clear, responsive, and grounded in real-world inventory.
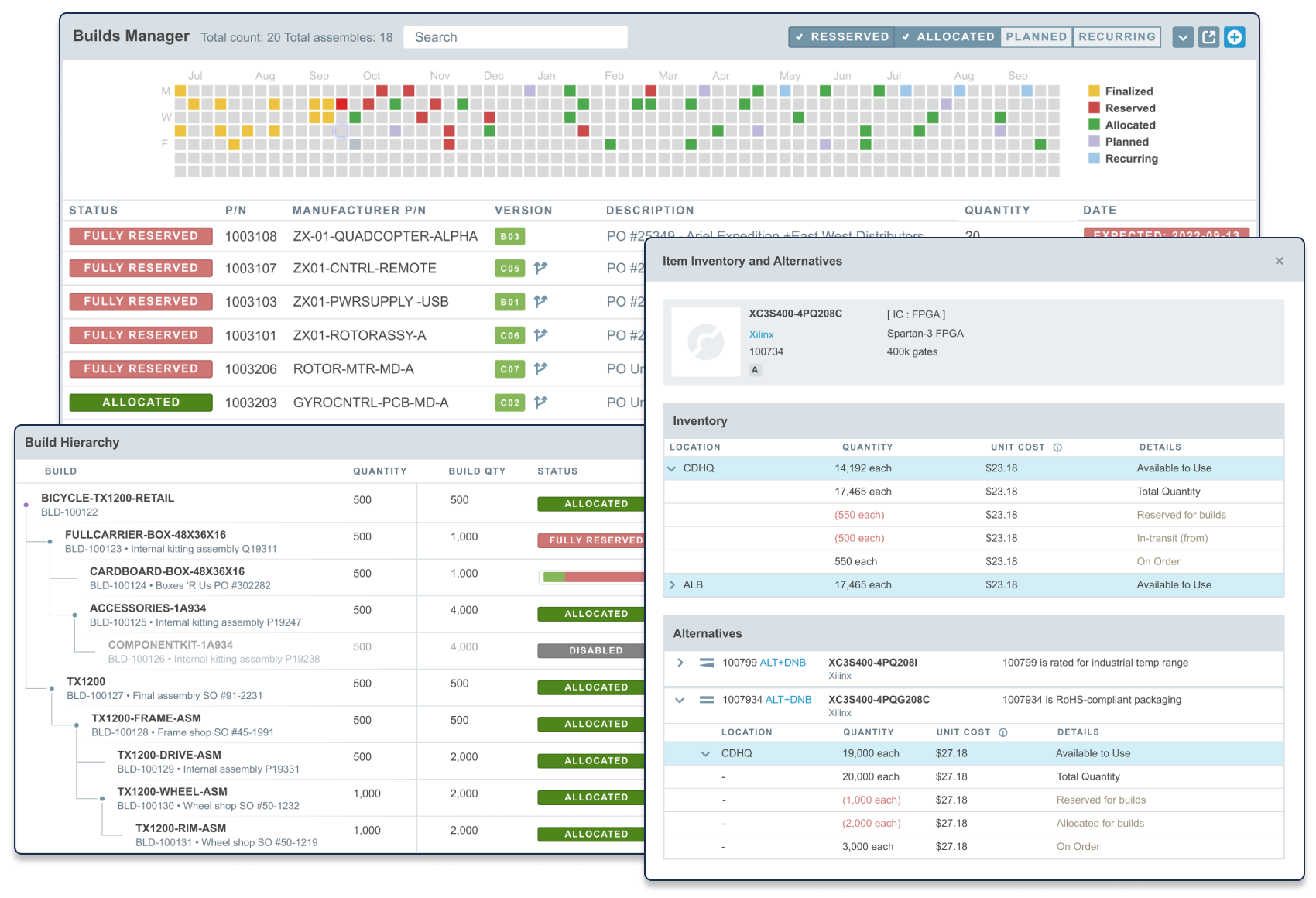
Execute with Confidence
Aligni builds transform your BOMs into actionable plans—tracking material usage, scheduling needs, and production progress in one place. What do builds do?
- Establish component demand to drive procurement of shortages
- Facilitate component deviations or substitutions
- Reliably adjust inventory as components are consumed
- Record which items were used and what they cost
Builds are the foundation for procurement, inventory, and production. They create a framework for smarter planning, better visibility, and faster decisions at every step.
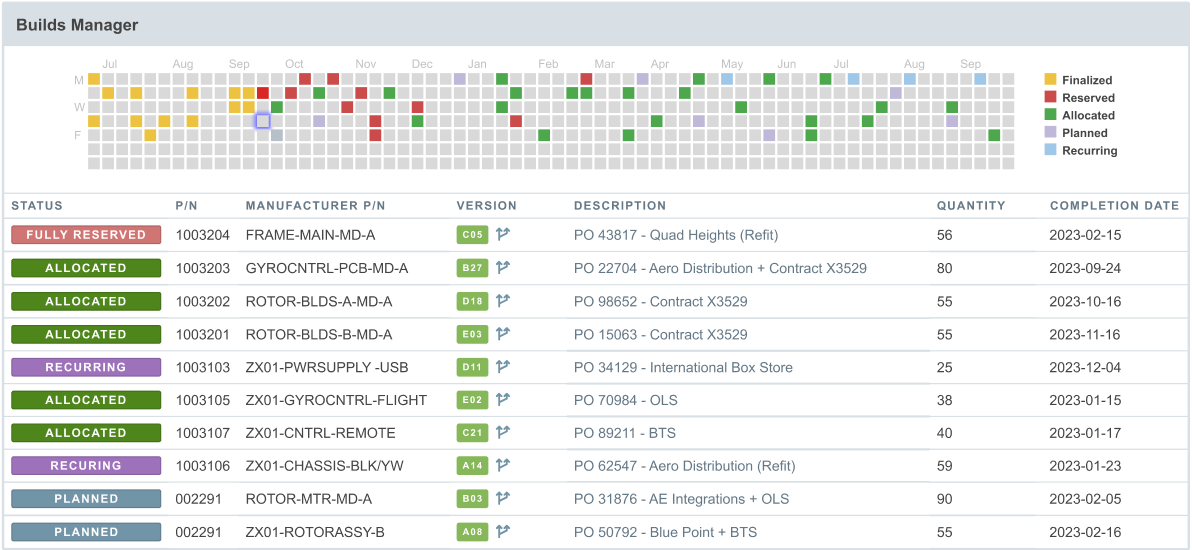
Build On-Time
On-time production demands accurate knowledge of material shortages. Aligni’s Material Shortage Report helps you prioritize what matters.
- Identify critical shortages across all active builds
- Sort by lead time, urgency, or part category
- Filter by manufacturer, vendor, category, and even production period to keep your purchasing focused
- Drive procurement with live demand data
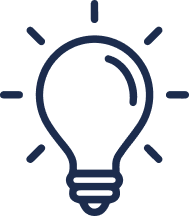
What is a Build?
A build represents the process of consuming components from a BOM to create a finished assembly. It connects your inventory, procurement, production, and quality control within a single record and traceable events.
In Aligni, every build records which parts were used, what alternates or deviations were made, what the build cost, and the final quality outcomes—giving you full visibility into the real-world execution of your production plan.
Track Usage and Cost
Each build becomes a detailed record of what was used, substituted, and spent—down to the unit cost.
- Capture part-level usage and cost details
- Log alternates or deviations as they happen
- Preserve full traceability for future audits and analysis
You get a historical, audit-ready record of each production run.
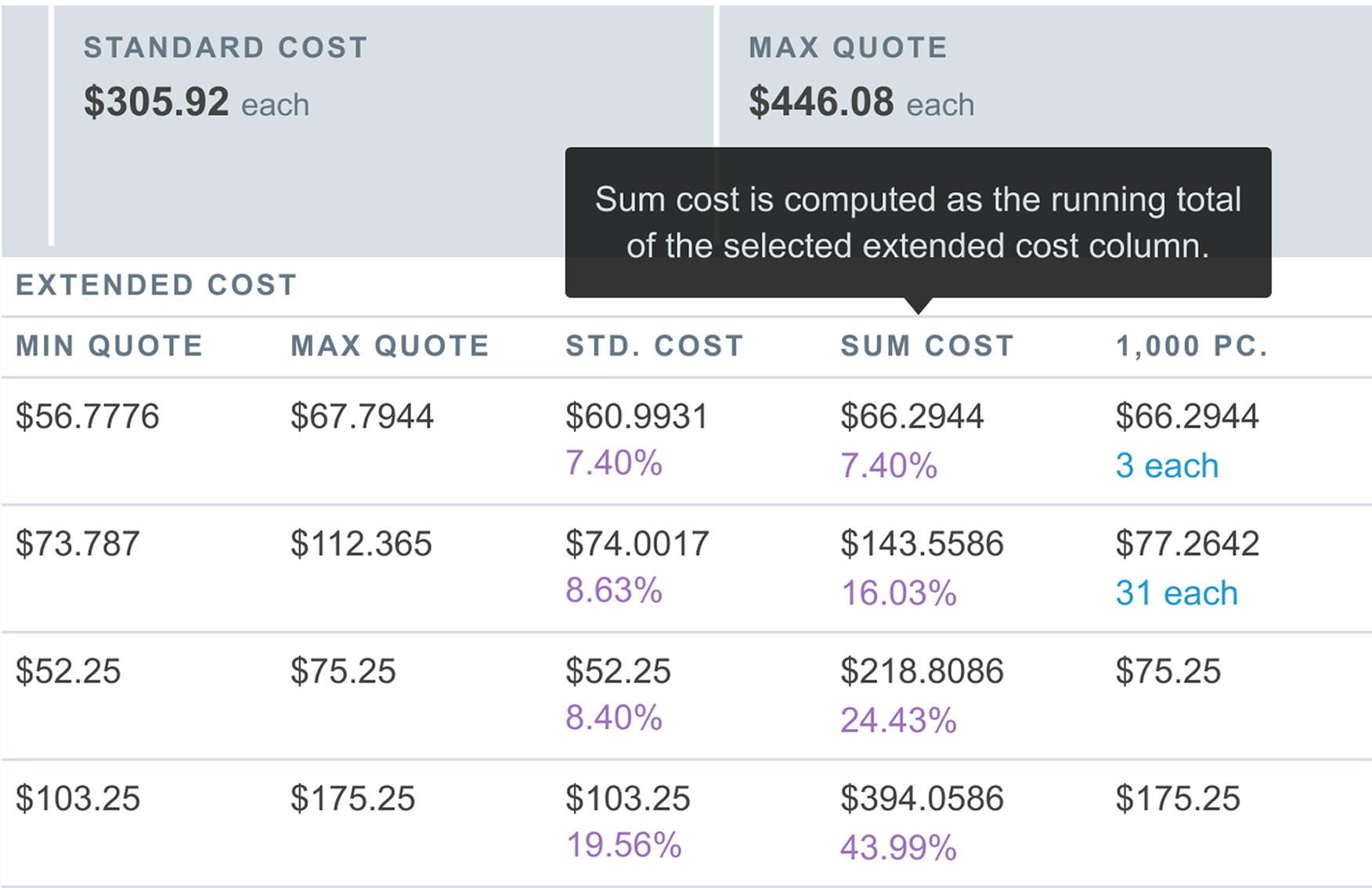
Drive Action with Inventory Forecasts
Get a live forecast of available stock, expected deliveries, and anticipated inventory gaps—so you can make smarter, faster decisions before issues hit your production schedule.
- Prioritize Shortages – Focus procurement on what’s truly urgent
- Manage Partials – Know when partial inventory covers short-term builds
- Track Incoming Inventory – See what’s ordered and when it’s expected
- Monitor Safety Stock – Stay above buffer levels without overstocking
- Visualize Lead Time Risk – Identify which parts threaten your schedule if delays occur
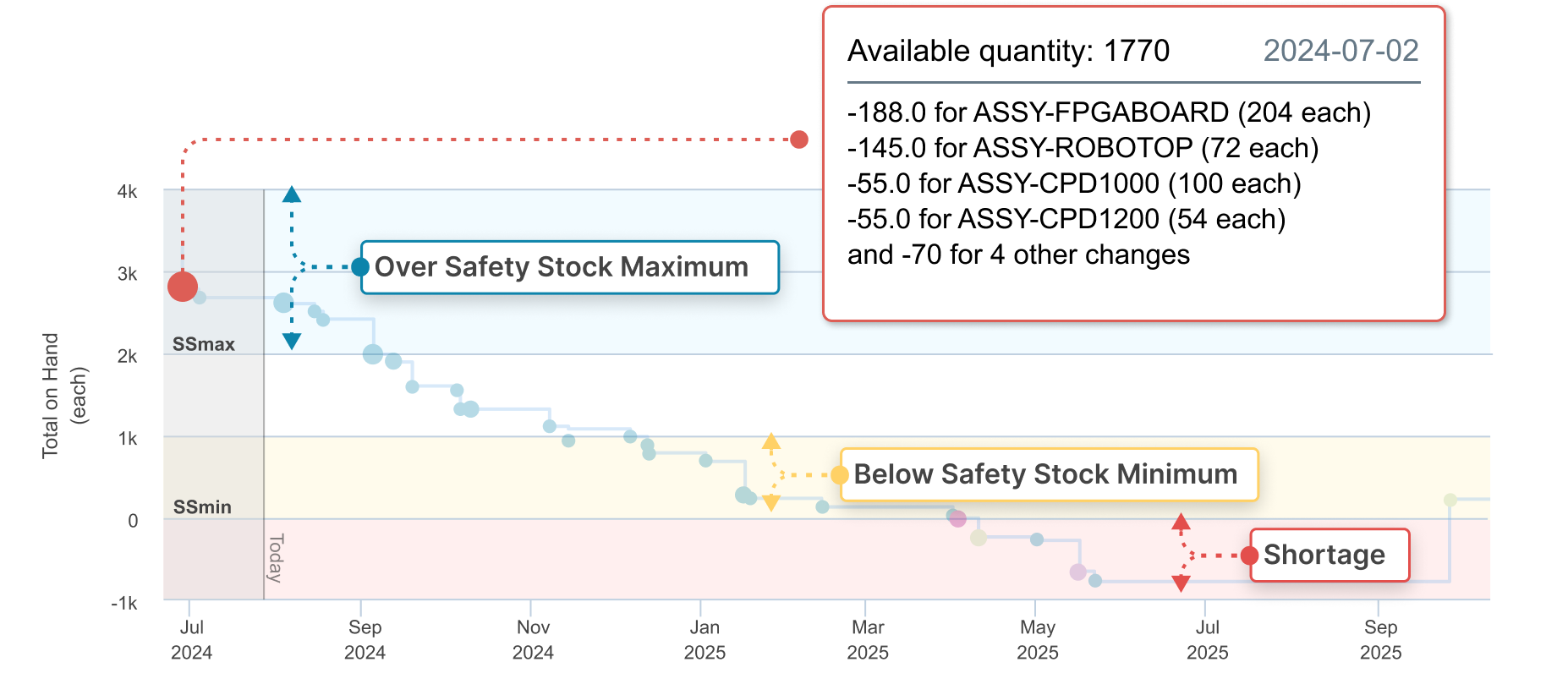
Adapt with Alternative Parts
Substitute approved alternates and apply build-specific deviations with clear documentation — all without slowing down production.
- Swap components without disrupting workflows
- Record substitution reasons and approvers
- Handy helpers provide insights into available alternate inventory
Maintain momentum without sacrificing quality.
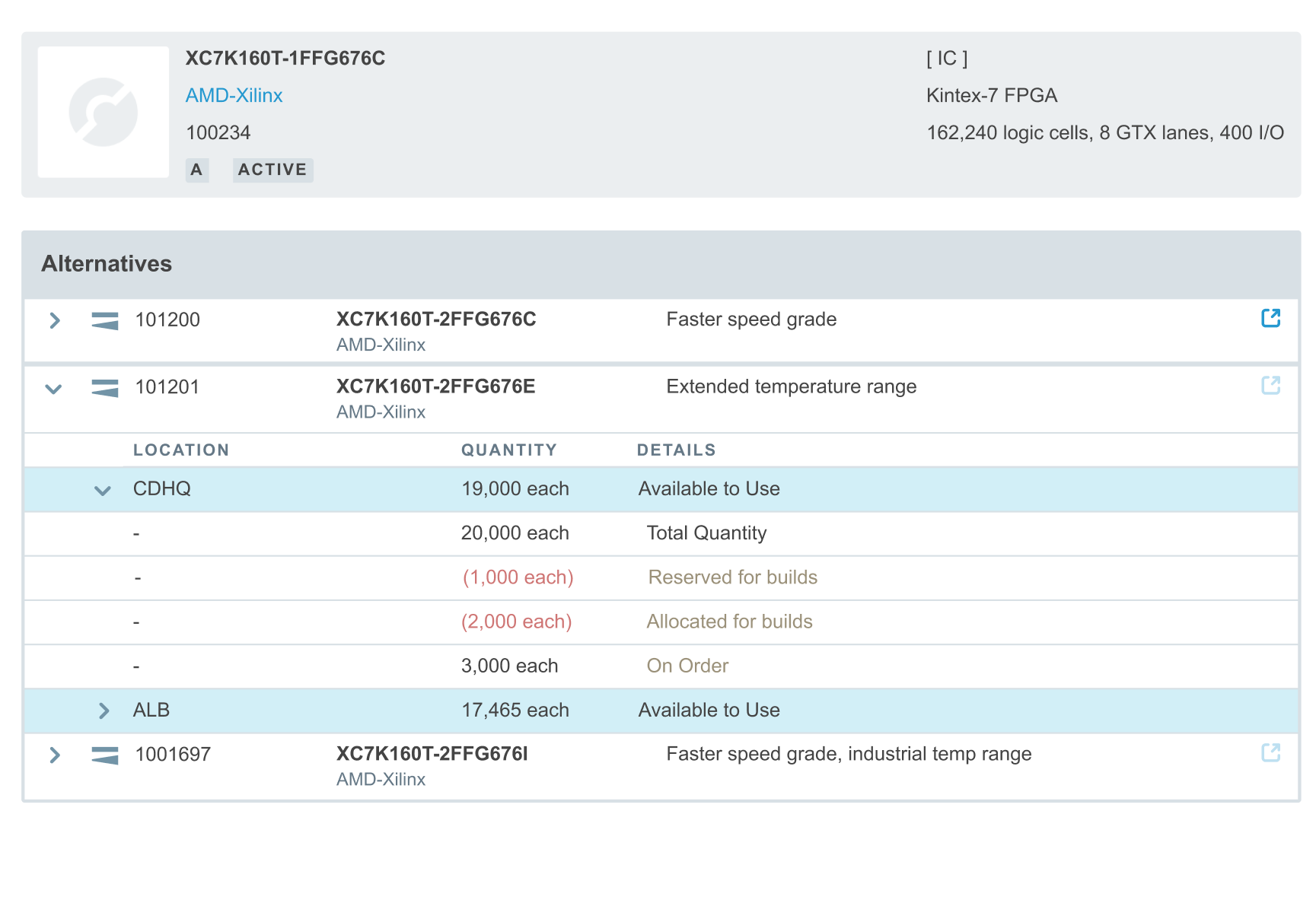
Expedite the Evaluation
Evaluating business software shouldn’t take months. Aligni makes it simple to go from login to live results — no complex setup, no IT support required.
- Test drive a live demo and experience Aligni’s workflows right away. Invite colleagues, load real data, and see how it fits your operations.
- Start a 30-day free trial with free onboarding to get your team moving fast. Importing services are available to help you hit the ground running.
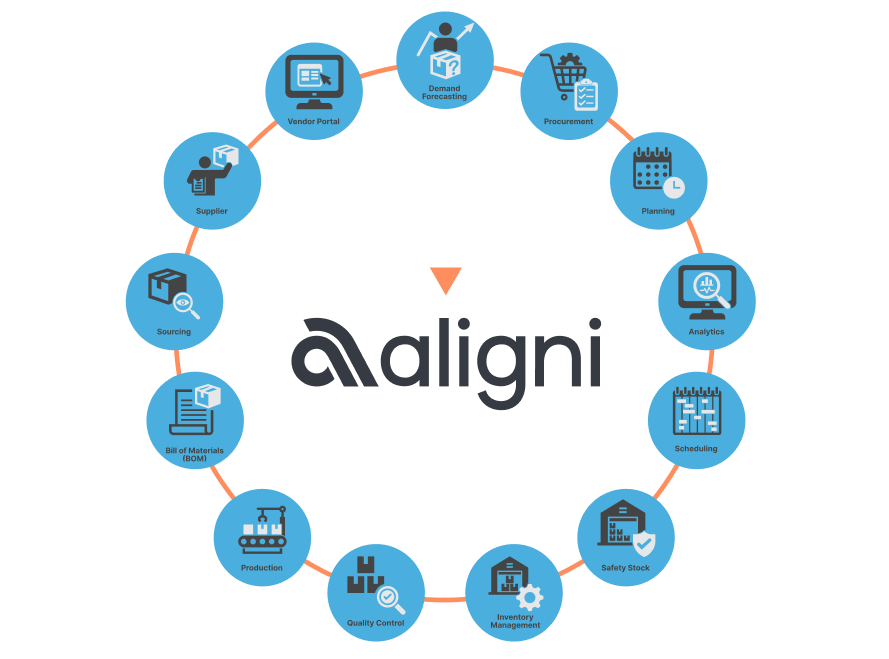