Developing products for production can be a battle of functionality and quality versus cost and delivery. The key to getting this balance right is to have the right information at your fingertips during the process. Using stale part pricing data and relying on material availability assumptions is a sure way to run into trouble – not just for accurate product pricing but for guaranteeing that parts will be readily available for builds.
When businesses are just getting started, part and material selection can be managed through home-grown or spreadsheet-based methods. When the complexity increases, these systems and the companies that rely on them start to become burdened. The pressure develops from not only managing greater amounts of data, but from a lack of cohesion of that data between functional groups within the organization. Even the sharing of information becomes a process that needs to be managed to ensure everyone in the organization is using the most current information.
That means the first step in keeping product costs in line is getting the company’s data properly interconnected and shared. This is the time to migrate to a purpose built software system that’s designed to be the hub for part and material knowledge. For most manufacturing organizations, that solution is a Product Lifecycle Management (PLM) system and the hub for knowledge is known as the “item master”.
Using a PLM System: The Right Tool for the Job
A PLM system is a software solution that manages the entire lifecycle of a product from initial concept through design, development, manufacturing, and eventual retirement. The software serves as a central repository for all product-related information, facilitating collaboration, data management, and process automation across different departments and stages of the product’s life. This includes part and material costing, availability, and vendor information. In short, it acts as a bridge between product engineering and supply chain operations, providing two lines of communication where both sides can easily share information.
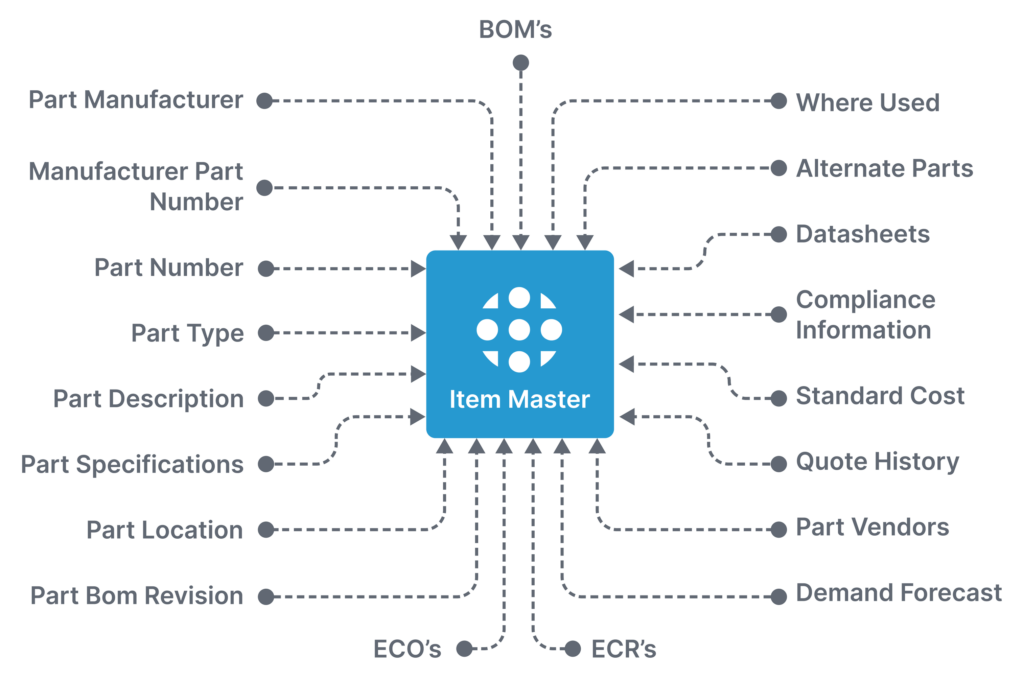
A PLM system provides its ability through consolidating all product-related data (designs, specifications, BOMs, CAD models, documents) into a single, accessible platform. This single source of truth ensures consistency and accuracy across the organization. The PLM manages the creation, modification, and approval of bills of materials (BOMs), ensuring that all necessary components and materials are documented and linked to the appropriate designs. This can include different configurations of a product, including variations and customizations.
Perhaps most importantly for this article, a PLM system tracks and estimates the costs associated with everything involved in building the product, helping to manage budgets and optimize cost-efficiency. Robust systems like Aligni PLM also integrate with procurement processes to track supplier costs and manage supplier relationships effectively.
So, how does an organization use a PLM system to better manage costs associated with bringing a product to market? Below we step through three of the most important aspects of product cost management and how they are handled with the help of a PLM system.
Building BOMs with a Focus on Total Cost
After designing a product, the next step is to ensure it lands within the pricing set by the market with enough left over for worthwhile margin. That includes managing component cost. Sometimes it entails making tradeoffs between not just part types but vendors, as well. To do this efficiently, engineers need to have up-to-date information available to make the right decisions.
Aligni PLM enables engineers to make the best decisions on the total cost of a product by integrating cost-related data to each of the parts and quantities that make up the product itself. It centralizes the purchasing data of individual components and provides direct visibility within the BOM. Aligni automatically calculates the total product cost by aggregating these contributions.
As the supply chain data and processes are baked into the PLM, the system also tracks supplier performance and delivery metrics. This includes changes to unit prices from volume discounts, other parts supplied by the vendor, and other details to provide real-time updates to part pricing. Aligni PLM goes further by providing historical trends that could indicate the direction of prices in the future. Since this purchasing information is shared with engineers, they can make choices on which part to use and from which vendor to arrive at the best possible mix of parts and total cost in the development stage of the process. This can be done without lengthy interchanges between departments, streamlining the specifying process.
Factoring in Part Inventories and Lead Times
Hitting price targets is one thing. Choosing the parts that are in stock or have the greatest potential to arrive on time for production is just as important.
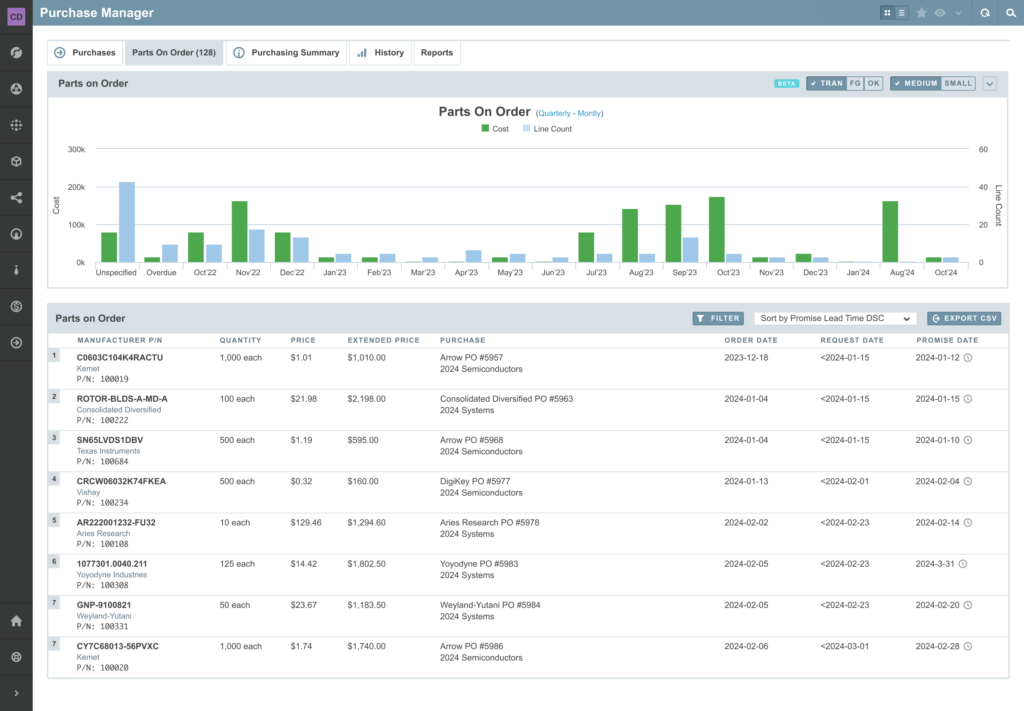
Organizations use product lifecycle management software to ensure part availability and delivery goals by centralizing and managing all information related to parts and suppliers. They also associate this information to the products that need to be built. The PLM system tracks part availability, lead times, allowing organizations to monitor and manage their supply chain effectively. Aligni PLM adds to this by integrating with procurement and inventory systems within Aligni MRP, providing real-time updates on stock levels and potential shortages, helping to avoid delays in production.
Additionally, Aligni MRP helps automate the workflow for ordering parts and managing supplier relationships, ensuring that orders are placed and tracked efficiently with its Vendor Portal functionalities. This proactive management of parts and suppliers through MRP software helps organizations maintain continuous production and meet their delivery timelines with a level of granularity that is difficult to achieve with homegrown spreadsheet-based systems.
Making Changes with Alternative Parts and Vendors
Sometimes the parts initially specified cannot be used. Perhaps they’re currently unavailable, have gone obsolete, or changes in customer requirements force the need for replacements. Regardless, replacing the part with another takes the same amount of time as specifying the first part, but there are opportunities to reduce the effort – if the organization has the right tools in place to manage the data they already have.
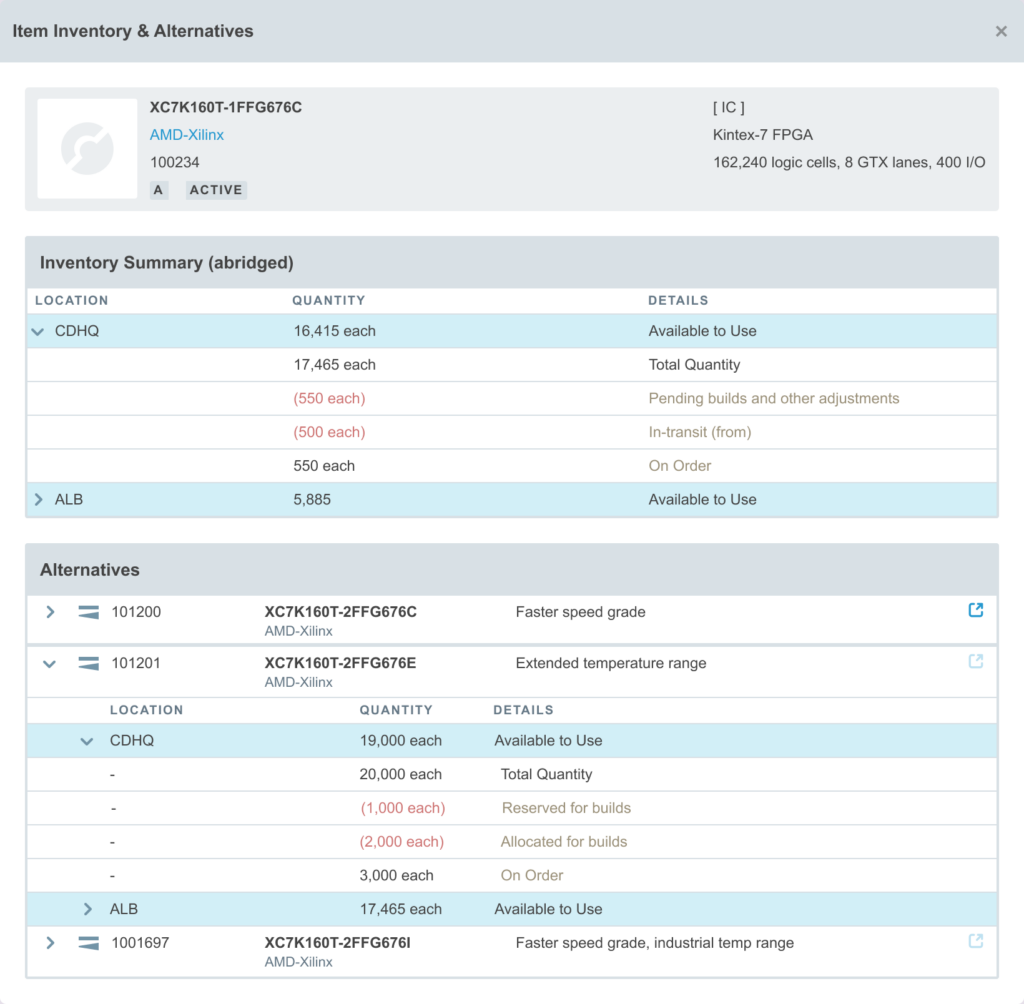
The process of specifying and purchasing parts yields a rich data set that can be impactful at a later date when change becomes necessary. During the initial quoting process, a company may weigh several parts and vendors. Only one will be selected for the product. Although others in the process may also suffice, they are not selected for various reasons. Retaining this information can help with quickly pivoting to an alternate part.
Some buyers also continue to quote currently used materials with new vendors hoping to locate more favorable pricing or purchase conditions. While many may not work out, the process may yield potential utility at a later date. Saving this information and making it readily available helps companies be more responsive to changes and reduces double work
Aligni PLM provides organizations a means to utilize the efforts of that initial process and the ongoing efforts of the purchasing team by continuing to make that information accessible. Aligni is built on a database, rather than a collection of files. This foundation allows the system to easily manage large amounts of pricing and vendor information. It ensures the data is collected in one location, systematized, and made accessible to make the process more efficient. This provides organizations with a set of potential alternate parts that have been previously vetted and at their fingertips if BOM changes need to be made..
Aligni PLM provides accessibility and storage of alternate part data inline with the day-to-day processes used by organizations to manage product development and sourcing operations. This alternate part information is available in several places within the software and where engineers and buyers need it most. For example, Aligni lists alternate parts and vendors for those parts within the part details screen. Alternates can also be found through the BOM screen on products in the system.
Bringing It All Together
Balancing functionality, quality, cost, and delivery during product development requires having accurate, up-to-date information. By closely monitoring and controlling part and material information, companies can optimize their costing strategies, maintain profitability, and stay competitive in the market. Ultimately, this helps in delivering high-quality products at competitive prices while meeting financial and operational goals.
Conversely, relying on outdated part data or assumptions about material availability can lead to problems with both pricing and production readiness. As businesses grow, managing part and material selection with basic methods like spreadsheets becomes inefficient due to increasing data complexity and poor information sharing across departments. This complexity and siloing leads to the aforementioned reliance on poor data and assumptions. To address this, it’s best to adopt a product lifecycle management system like Aligni PLM, which centralizes and streamlines the management of part and material data, ensuring better collaboration and cost control.