When part and material shortages happen, it can be embarrassing as well as expensive. As a company begins to juggle multiple production jobs, shortages have an even greater potential to occur. The way to escape from this possibility is to have a reliable, integrated production and inventory management process in place, as well as the tools needed to execute it properly.
Getting Your Data in One Place
The first step in reducing shortages is to have a complete understanding of what’s needed – both right now and in the future. This combination of knowledge extends past what’s needed for in-process builds to how those build requirements will affect materials on hand, as well as the consumption of parts ordered for future builds.
For many organizations, the difficulties stem from their data being spread across different departments. This situation presents challenges in synchronizing data between the “source” location and any other departments that need the information. These departments will need to extend their current processes to accommodate maintaining the shared repository of information. That requires continued cooperation to maintain this information in two locations: where it currently resides and the new, shared location. All this means far greater buy-in and oversight is needed to ensure the new data sharing processes are followed and the information remains current enough to be trusted.
These hurdles make it increasingly difficult to use spreadsheets or other file types. Updating information and sharing files opens opportunities for human error transcribing between files or overwriting changes. The increase in process steps invites skipped or forgotten steps, as well, both of which can lead to old or incorrect data. This is vector for undesirable shortage challenges.
The better option is to utilize a database system to house the data. MRP systems like Aligni are usually built on an item master database that’s designed to centralize production and inventory information. These systems are built to streamline the associated management processes as well. Combining both process and data in one system helps make sure all in the organization are working off the most up-to-date information. This increases collaboration and reduces errors. At the same time, it helps to guarantee that up-to-date information is used for planning production needs and important changes are identified quickly.
Starting from a Production Schedule
After the data is organized and in one place, the next step is to get an understanding of what needs to happen and when. This requires charting out all production builds by production date on what is typically referred to as a production schedule.
Broadly, a production schedule is a detailed plan that outlines the activities of a manufacturing process over a certain period. It specifies which products need to be produced, the quantity of each product, the sequence of production activities, and the timeline for completing each task.
When all builds are listed in the production schedule, the manager can better understand how and when stock is consumed and plan for future demand. More importantly, the manager can analyze how the needs of each job interrelate with one another. For instance, the production schedule can show where builds that require the same materials happen around the same time. This knowledge helps buyers better plan inventory levels and reduce stock outs from stacked demand – something that can be lost when managing jobs in individual spreadsheets.
While a simple production schedule can be built within a spreadsheet or other file, keeping the information current within that file can be almost impossible. As mentioned earlier, this information comes from several different sources within an organization and requires each to make necessary manual changes to the spreadsheet when they occur to the production schedule. This is especially true when the number of builds or complexity increases.
Relying on manual updates is dangerous when several groups provide the information. This is another reason a purpose-built system shared across all departments is crucial to ensuring smooth production. With an MRP system, any changes are pushed across the entire organization, including changes to order dates, order quantities, or what makes up the product itself.
Managing Inventory from the Production Schedule
Once the production schedule is laid out, the company can work through its parts and materials needs from the builds listed. The production schedule informs the inventory manager what parts are required and when. More importantly, it provides a complete picture of total product demand over time – the first step in becoming more proactive on what inventory is needed.
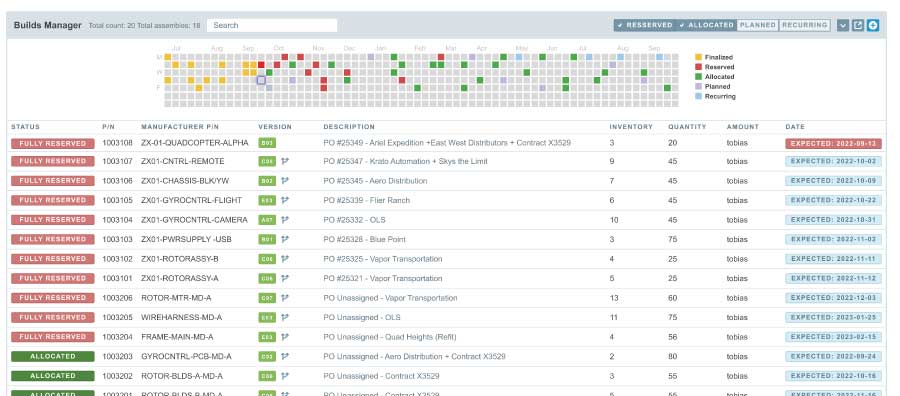
The next step is for the inventory manager to comb through all the jobs listed on the schedule and collate a list of all parts and the dates they’re needed. Then the manager compares the list to the stock on hand to determine what needs to be ordered to fulfill the build requirements.
What makes this process a bit easier is to stage this process for the most immediate jobs first. Regardless of whether needs are sectioned in shorter intervals or longer ones, this process needs to be executed flawlessly. Otherwise, any error or omission leads to a potential shortage situation.
The process described above may appear straightforward, but when there are large numbers of builds on the schedule or builds with extensive BOMs, it becomes extraordinarily time-consuming, if not seemingly impossible, to manage. Additionally, as the complexity increases, the likelihood of errors also rises. This is especially true when using homegrown tools or spreadsheets where triangulation between files and a heavy reliance on cutting and pasting cells is foundation to the process. Broadly, the greater the human process needed, the greater the potential for stockout events.
In Aligni MRP, all of the builds are in the same system, as well as their bills of materials and the company’s inventory records. The database system that stores the information makes it easy to connect each of these aspects together quickly. The process of sifting through jobs to find parts needed is an automatic function within Aligni. This vastly reduces the time necessary to develop the lists of materials needed. It also reduces the potential for human error in searching for, collating and developing inventory demands.
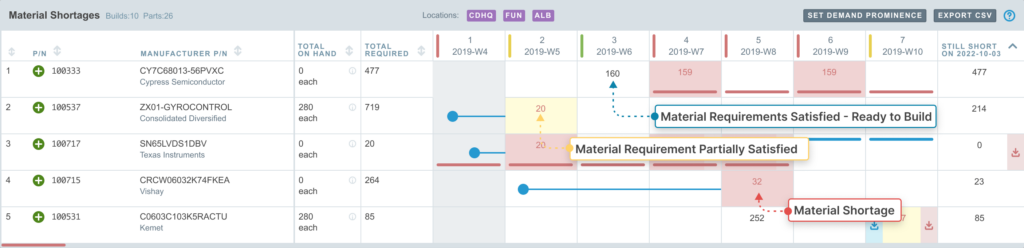
Keeping It Safe with Safety Stock
While doing all of the above goes a long way to reducing shortages, it’s good practice to have extra parts and materials on hand. Organizations often hold a certain percentage of inventory above what is initially planned. The extra inventory accounts for a number of potentialities including quality issues, delayed part deliveries, variance in inventory counts, and even unaccounted-for product demand. This term for this overage is called ‘safety stock.’
Safety stock levels also need to be managed closely to get the greatest value out of carrying the extra materials. They have to be overseen to guarantee that there is enough inventory, as well as watched to make sure the organization does not tie up too much funds in buffer stock.
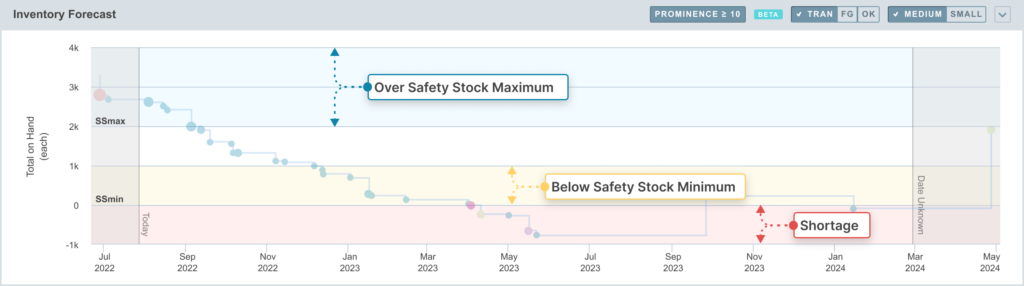
Well-managed safety stock levels require understanding the average demand requirements of the organization. That includes collecting historical inventory consumption data and being able to forecast what demand requirements in the future. From here, a manager can arrive at a level of stock that will help ensure production runs smoothly without overbuying materials.
Once again, with smaller order volumes or recurring orders, this can be a rather simple process, and one that could be done with basic tools. As the quantities and complexity increases, the amount of data needed to parse to arrive at viable safety stock quantities can become next to impossible without the right management tools.
Where an MRP system like Aligni shines is being able to easily collect and present this historical data in a less time-consuming manner. Aligni also includes forecasting functionality that can help estimate future demand. Both of these abilities help managers utilize their data to be proactive in making sure there’s enough safety stock on-hand, even for future events or for common issues.
Maintaining a Competitive Edge with Dashboards and Alerts
Like all dynamic systems, inventory management requires constant vigilance. It’s good practice to oversee part consumption, orders, and deliveries on a daily basis. Systems like Aligni provide a dashboard where managers can understand all these aspects at a glance.
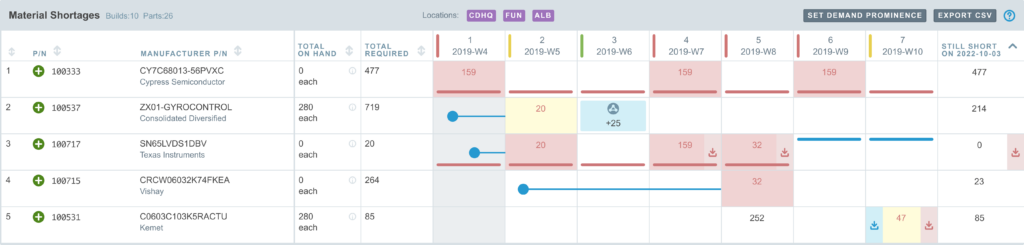
This Material Shortage Report displays all current builds in one place, their part needs and lead times for ordering required components. In Aligni, this report is updated in real time as others in the organization change information related to each build. Checking the report daily ensures managers are abreast of any changes and can make adjustments quickly.
Going further, putting in place alerts when certain scenarios are about to happen can also provide an extra measure of security in reducing shortage events from occurring. Managers can do a lot with putting tasks into calendars but using an MRP system provides the ability to place conditional alerts when event thresholds are nearing. Alerts that are set to specific inventory or demand actions provide greater utility to managers than disconnected calendar tasks. In Aligni, these alerts can be set to information from other departments like purchasing or quality. This gives even greater exposure to condition changes that might need attention before calamity strikes.
Taking the Next Step
Overall, the key to managing shortages is to better manage your organization’s data. Putting processes in place to collect, centralize, and update production and inventory data is necessary to truly understand what is needed and when. This foundation is needed to properly plan for future needs.
When the organization’s needs are still relatively simple, this can be done with spreadsheets. Once complexity increases, the company will need to migrate to purpose built solutions to better collaborate and manage greater volumes of frequently changing information.
If your organization is drowning in data and stumbling on shortages, then it’s time to get the right tools for the job. It’s time to sign up for Aligni MRP!