When new features are available, it may not be evident how the feature should be added into an existing workflow. At Aligni, we get it. That’s why we’re walking through an example workflow for our Material Shortage Report (MSR). The goal is to show how the MSR will help organizations better track upcoming jobs, identify trouble spots and better plan for future needs – these are all areas where the MSR shines.
Benefits of Managing through the MSR
- Provides one location to see all part shortages
- Sortable and color-coded to find issues quickly
- Offers visibility to be strategic in part and vendor management
While certain industries or production scenarios may require modification of this workflow, we have provided here a baseline process to get the most out of Aligni’s MSR functionality.
Setting up the MSR for Success
First off, the MSR works best when all jobs are listed in the system. Inventory can only be managed properly when there are builds making claims on the inventory required. Jobs can only be properly managed when they’re all in the same system. Otherwise, the potential for lost jobs and dropped inventory needs is heightened.
A Quick Tour of Aligni’s MSR Features
1.
Visualize and prioritize shortages on a timeline or build-by-build basis.
2.
Intermediate build products and incoming inventory.
3.
See how lead time affects procurement priorities.
4.
Partial shortages mean that short batches could be considered.
5.
Safety stock indicators depict areas of concern for demand spikes.
The MSR is designed to be checked on a routine, even daily, basis according to production demands. This frequency helps make sure operations move as smoothly as possible. In Aligni, when details are updated, they’re updated immediately across the system. This includes changes being represented in the Material Shortage Report. Ideally, it should be one of the first items checked daily and for many users, it becomes the dashboard for inventory management.
Dialing in the MSR for Productivity
Start by filtering all shortages in the system by order date. Rearrange the report to place the jobs closest to production in the top left of the chart and orders into the future towards the lower left of the chart. This configuration gives focus to the jobs in the chart that will be happening soonest. These require the most immediate attention.
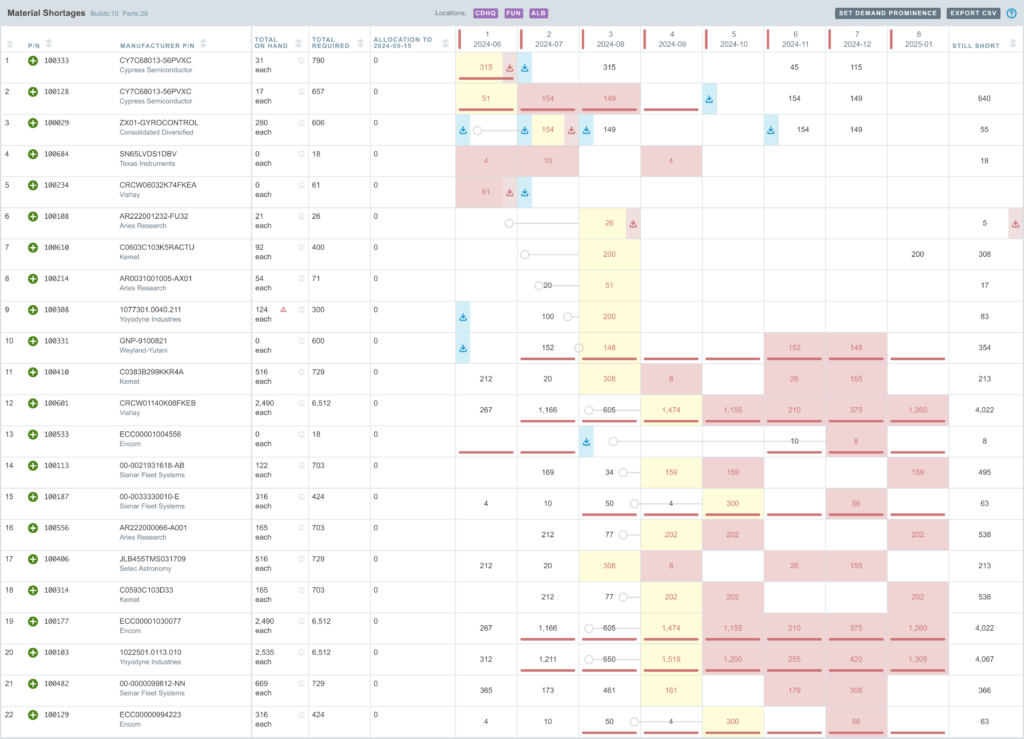
Tip: To get even more visibility on what needs to be treated first, use calendar mode to show lead times for the parts within the system. These lead times help make sure orders are placed with enough time to make sure the parts arrive before they’re needed in production.
Checking for Hot Spots
Next identify the jobs that are in need of parts. The builds that do not have enough parts available for the build show up on the MSR as red blocks (no parts available) or yellow blocks (some parts available).
Look for the production jobs that have no parts in stock. These jobs are the ones that need attention first, as they stand to hold up production.
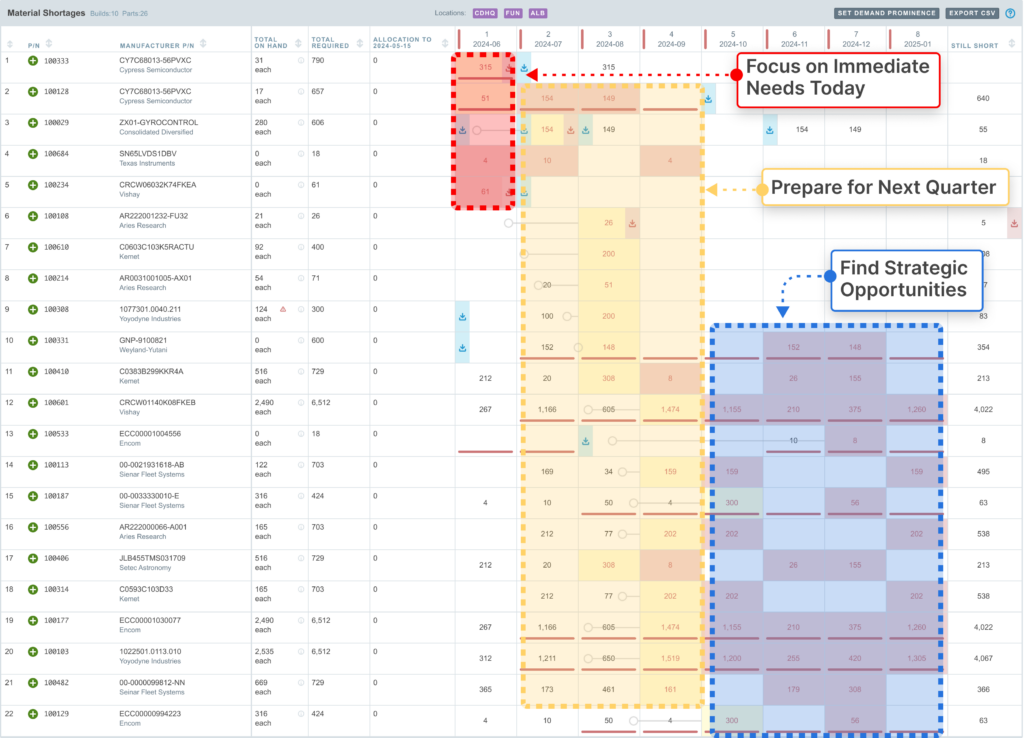
Prioritizing inventory needs by availability is the next step. This is where knowing a part’s lead time helps buyers make more efficient choices. It is best to select the jobs with the longest lead times to solve first and work towards the shorter times. This helps reduce rush orders to only where they’re absolutely needed, saving money in the process.
The jobs on the MSR with partially reserved parts should be next to treat. The same process should be followed by treating the longest lead times first.
What jobs won’t have parts available for their build date will need to be immediately related to production and sales. While an unfortunate situation, tracking this information in the MSR makes sure no jobs are lost. When unfixable situations arise, they can be dealt with quickly.
Looking Over the Horizon
Once the immediate needs are treated, it’s time to use the MSR as a guide to handle longer-range production and inventory needs. This is where more strategic actions can be managed using the report.
Managers and buyers can use the MSR to look forward to builds planned for further on the horizon. They can use the report to evaluate upcoming needs in larger chunks like months, quarters, or even years. When demand is far enough out, buyers can start to group needs by other means than the builds themselves. This provides the opportunity to negotiate better delivery terms and potentially lower prices on materials.
Buyers can use the functions in Aligni to group these long-range needs by vendor. This view can help buyers combine orders into one, larger order for each supplier. With delivery dates set well into the future, buyers need only present one RFQ for the list of parts and combine into one order for easier management.
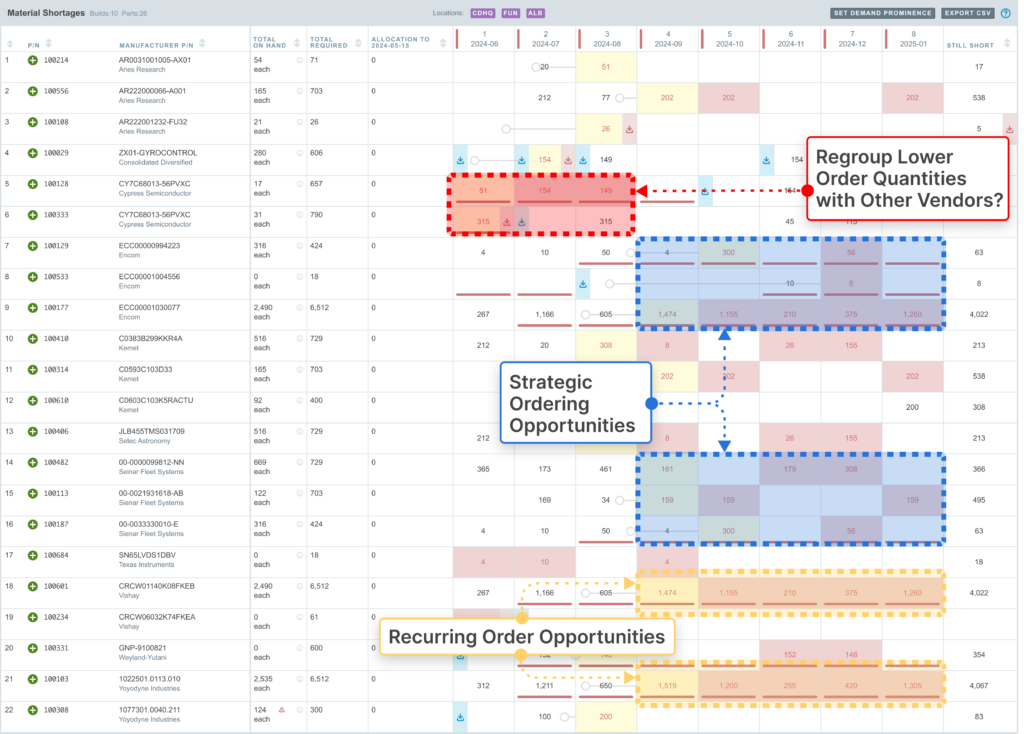
Consolidating orders by material rather than build creates larger volume orders for parts. Typically, buyers can extract better pricing with larger quantities. Having the ability to combine needs through the MSR makes this easier for buyers.
All of this functionality stems not only from a better, more concise user interface for the information but it’s being built on the foundation of the data handling the Aligni already provides with its item master database. Buyers and managers can better understand the current and future conditions and better act on the data they have to help reduce issues, be more efficient, and save money. Best of all, Aligni’s MSR is already available for all Aligni MRP users – just steer to the Aligni Home Screen and press the ‘Material Shortage Report’ link and get started today!

Summing it up
At Aligni, we understand there’s many different ways to run a manufacturing operation – and that means there are many ways to manage its inventory. With our material shortage reporting functionality, organizations have the flexibility to follow the processes that work for their operations while getting far better visibility into those processes. They also are now able to capture greater efficiencies and value integrating into their current processes, the unique abilities Aligni’s Material Shortage Report can provide.