When things are simple, production and inventory can be managed with simple spreadsheets and copy and paste processes. As demand complexity grows, inventory management complexity grows along with it. That makes it difficult to see above the trenches long enough to plan ahead. But getting to the next level comes from planning, so what does it take to look further ahead?
Why Perform Longer-Term Forecasting?
Long-term inventory forecasting is crucial in manufacturing as it allows companies to anticipate future demand, optimize supply chains, and maintain production schedules without disruption. Accurate forecasting helps avoid last-minute “fire drills,” where a sudden shortage of materials or components forces manufacturers into emergency measures that can lead to downtime and missed shipping dates. These fire drills are not only costly in terms of lost production time, but they also strain labor resources and erode customer confidence when delivery timelines aren’t met. With a solid forecast and tools that manage inventory requirements like Aligni’s MSR below, manufacturers can ensure they have the necessary stock levels and can schedule production efficiently, reducing the risk of delays and improving overall operational flow.
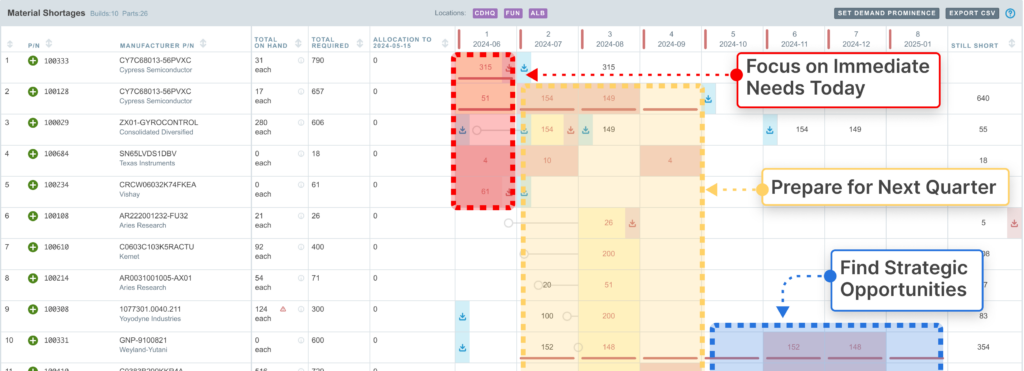
Moreover, long-term inventory forecasting puts manufacturers in a stronger position to negotiate better terms and pricing with suppliers. When businesses can accurately predict their needs months or even years in advance, they have greater leverage to secure bulk discounts or favorable payment terms. Suppliers are more likely to offer incentives when they know there will be steady, predictable demand. This can lead to significant cost savings, which is particularly important in industries with tight margins. By locking in better terms, companies can improve profitability and ensure they remain competitive in the marketplace.
Long-term forecasting enables better strategic planning for future needs. Manufacturers can use these insights to plan for capital expenditures such as investing in new machinery, expanding facilities or hiring additional staff to support growth. This proactive approach ensures that businesses are prepared to scale up without experiencing bottlenecks or capacity issues. Rather than reacting to sudden increases in demand, companies can plan and allocate resources well in advance, positioning themselves for sustainable growth. A forward-thinking mindset is essential for maintaining long-term competitiveness and financial health in the manufacturing sector.
Investment in Data Collection Is Key to Success
To build efficient and dependable forecasts, manufacturers need to gather large amounts of data from multiple sources and connect that data in meaningful ways. The goal is to transform raw figures into actionable insights that can drive decision-making and optimize inventory levels. Data collection spans everything from current production status to future projections, requiring a comprehensive approach to ensure accuracy and reliability.
A key piece of information manufacturers need is the status of all current and committed builds. This includes detailed records of work in progress, along with all planned builds that will be produced in the future. Additionally, it’s crucial to have a clear breakdown of every component required for each build so the company can accurately track its material needs.
Factoring Availability
In addition to tracking current and future builds, manufacturers must collect data on inventory quantities already on hand as well as pending and planned orders for new inventory. This includes understanding the lead times for each part or material which may vary significantly depending on the supplier or geographical location. Knowing these lead times allows companies to time their orders appropriately and ensures that materials are available when needed, rather than arriving too early or too late. All of this data forms the foundation of a robust inventory forecasting system where every component and material is accounted for in real time.
Staying Current
For accurate forecasting, it is also essential that the data is continually updated and adjusted. For example, as builds are completed and components are consumed, inventory levels need to be adjusted to reflect these changes. Similarly, incoming shipments must be reflected in updated inventory counts. A dynamic, real-time data integration allows manufacturers to analyze their operations holistically, taking into account consumption rates, delivery schedules, and future production needs. By maintaining an up to date, connected system, manufacturers can better plan for the future, avoid production delays, and optimize their supply chain to meet demand efficiently.
Knowing When Better Tools Are Needed for the Process
One major challenge manufacturers face with traditional tools like spreadsheets is the need to integrate data from different departments. When this information is fragmented across multiple files and systems, significant time and effort is consumed searching through servers or requesting updates from colleagues. Even when this information is located, there’s no guarantee that it’s the most current version, which can lead to errors in forecasting and planning. Purpose-built software provides a single source of truth, where data from every department is integrated and automatically updated, reducing the chances of miscommunication and ensuring decisions are based on accurate information.
As production scales, so does the complexity of tracking materials and parts. Manual systems have difficulty scaling to meet the new realities of inventory management. Managing future inventory requirements across multiple tabs or files is not only cumbersome, but it also increases the risk of data being entered incorrectly or not updated in all necessary locations. That’s why manufacturers turn to purpose-built software tools for inventory forecasting and planning. A specialized software solution like Aligni MRP streamlines this process by centralizing data into an item master database, ensuring that all information is consistent and accessible in real time.
Tracking part usage and predicting future inventory needs across several jobs is also difficult to achieve with disconnected processes. Manual methods struggle to integrate inventory demands across various projects, leading to inefficiencies in ordering and shortages that could delay production. Once again, Materials Requirements Planning (MRP) software provides comprehensive visibility into both current inventory levels and upcoming needs of all builds in the system, allowing manufacturers to plan more effectively. By having all data in one place, manufacturers can optimize inventory levels, avoid bottlenecks, and ensure smoother production workflows.
The Path to the Effective Management of Multiple Builds
Manufacturers need the right inventory management system to gain a clear understanding of their production needs to proactively manage inventory. For a business to operate strategically, managers must have full visibility into inventory usage, upcoming build requirements, and the current stock levels. Instead of wasting valuable time hunting for this data across different systems or spreadsheets, they need it to be instantly accessible in one place. Material requirements planning systems are designed to provide this critical visibility, systems like Aligni MRP show the status of all jobs and their material requirements in real time.
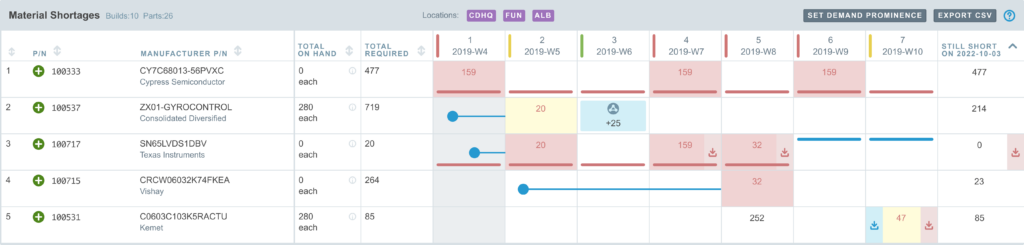
By displaying all jobs and their material needs on a single screen, tools like Aligni’s Material Shortage Report (MSR) help manufacturers understand total inventory demand at a glance. This consolidated view allows managers to prioritize jobs by identifying which builds are at risk of material shortages and which need immediate attention. With sorting features in the MSR, managers can quickly act to mitigate shortages, ensuring that critical production lines remain on track and that materials are ordered in time to avoid disruptions. This level of insight helps manufacturers move from reactive problem-solving to proactive inventory management, reducing costly production delays.
Additionally, the right inventory management system helps manufacturers manage order timing with precision. Aligni’s MSR, for example, also includes estimated lead time indicators that show when parts need to be ordered to ensure they arrive before production begins. These “drop-dead” order dates provide clarity for both buyers and production managers, highlighting when to focus on specific orders and when builds may need rescheduling due to potential stock shortages.
Efficient Oversight of Material Replenishment and Ordering
To effectively forecast demand, manufacturers must integrate purchasing into their inventory and production management systems. It’s not enough to simply monitor production demand; the organization also needs to track materials on order, considering how quantities and delivery dates impact upcoming builds. Without this integration, it becomes nearly impossible to assess the full effect of purchasing decisions on production requirements. Relying on separate systems—such as handling purchasing through email and managing inventory in spreadsheets—creates gaps in communication, delays, and mismanagement of critical data.
With tools like Aligni’s vendor portal, manufacturers can centralize all purchasing and delivery-related information, making it easier to manage these processes alongside inventory and production. The vendor portal handles requests for quotes (RFQs) and purchase orders (POs), giving vendors direct access to update quote and delivery information in real time. This includes the ability to update delivery dates, quantities, and any changes in orders as they happen. By integrating this purchasing data with production systems, manufacturers can better understand how procurement decisions affect production timelines and adjust as necessary.
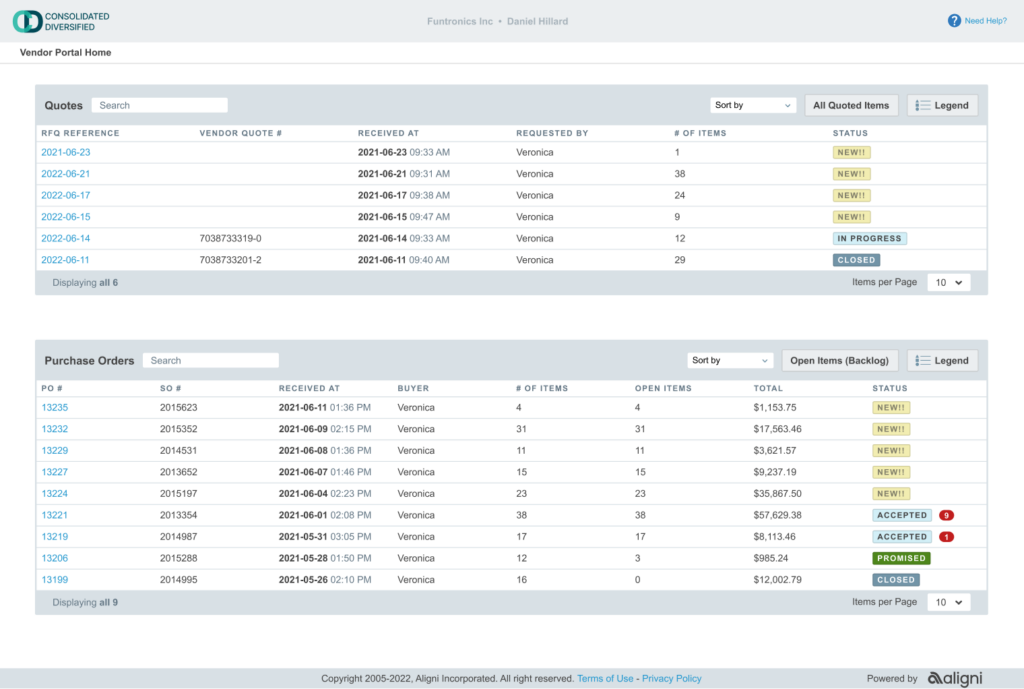
This integration provides greater control and visibility over inventory changes, both in the short and long term. Managing expected delivery dates, tracking changes in delivery schedules, and handling backordered parts all become more efficient when purchasing is directly tied into inventory management. With better insight into when materials will arrive and how delays or changes will impact production, businesses can plan ahead, avoid disruptions, and make adjustments to schedules or orders before issues arise. This proactive approach ensures smoother operations and more accurate forecasting of inventory needs.
The Long View of Build Planning and Inventory Requirements
To move from tactical to strategic inventory management, manufacturers need to forecast beyond just the next few weeks or months, gaining long-term visibility into supply chain and inventory demands. This approach is needed for maintaining greater control over materials and optimizing the benefits of efficient inventory management. Extending forecasts into the future with accuracy requires a system capable of handling vast data and providing meaningful insights. Without the right tools, it becomes difficult to track these changes, especially when managing large volumes of inventory.
Aligni MRP’s inventory forecasting tools enable manufacturers to manage this complexity by collecting and organizing the data needed for long-term forecasting. One of Aligni’s key features is the Inventory Outlook chart, which collates the demands of all current and future builds as well as incoming material (from procurement) into one comprehensive forecast for each part in the system. The tool automatically graphs the consumption and replenishment of materials against inventory on hand, providing visibility into where inventory levels might fall below safety stock thresholds. This makes it easier for managers to see potential gaps and take proactive steps to prevent shortages.
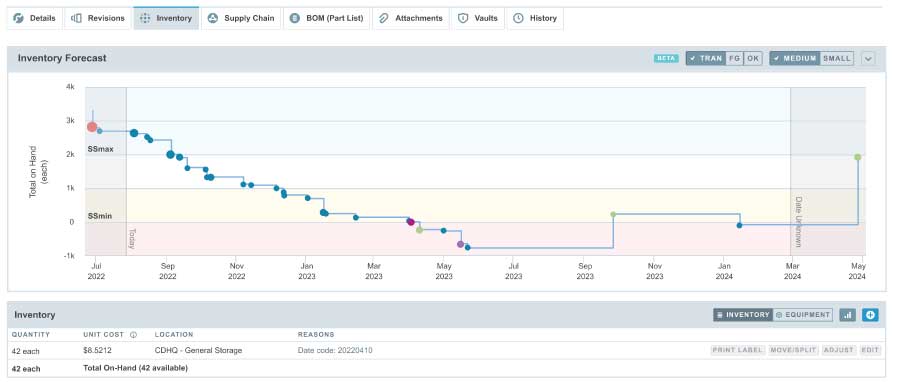
Aligni also offers tools like the product demand and component demand matrices, which allow manufacturers to view planned or recurring builds over extended periods, whether that’s quarters or years. These matrices are built from current and expected orders and show the parts and materials needed over the provided time horizon, helping buyers understand total demand over time. With this visibility, purchasing managers can make more strategic decisions, such as negotiating better terms by purchasing in larger quantities or spreading production demands across quarters to smooth out capital spending. This balanced approach reduces cash flow pressures and ensures that inventory management is both efficient and cost-effective over the long term.
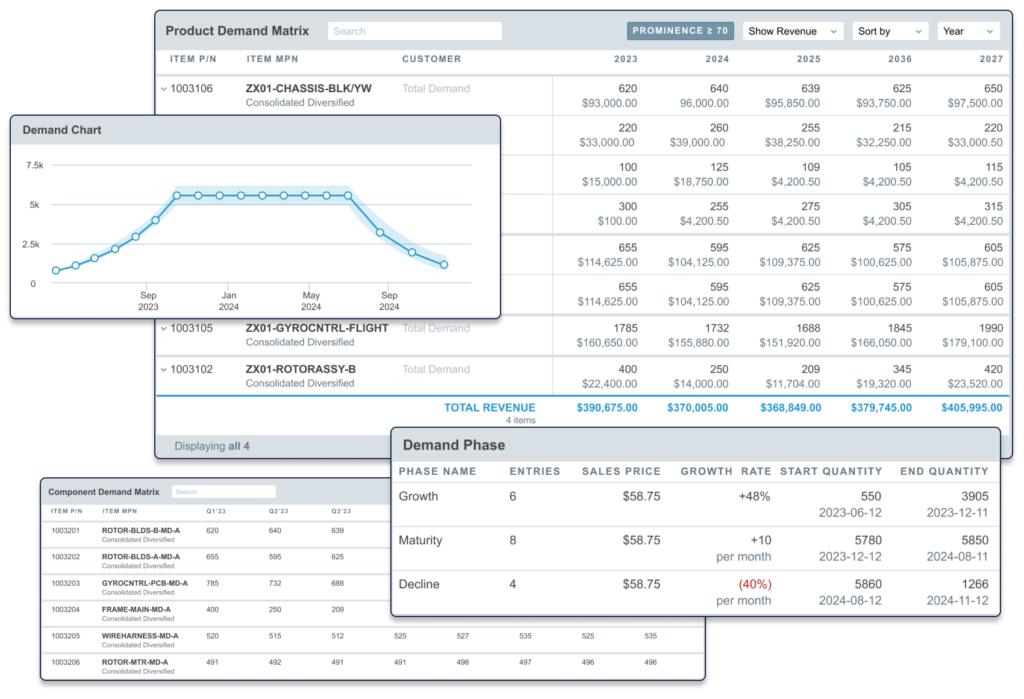
Summing It All Up
Long-term, strategic inventory demand forecasting provides manufacturers with key advantages, but achieving these benefits requires the right tools. Advanced forecasting tools like the ones Aligni MRP provide give manufacturers real-time visibility into future material needs, allowing them to anticipate demand fluctuations and avoid stock shortages that could disrupt production. These tools help optimize ordering schedules by consolidating data on current builds, future orders, and lead times, ensuring smooth production workflows. With accurate, long-term forecasts, manufacturers can negotiate better pricing and terms with suppliers, manage cash flow more effectively, and reduce the need for costly rush orders or last-minute adjustments. The right tools also align inventory management with broader business goals, helping companies plan for capital expenditures, scale operations efficiently, and ensure long-term growth.
If your spreadsheets are starting to fray and it’s getting harder to find the right data to make decisions with, it is time to get the right tools. It’s time to migrate to Aligni MRP.