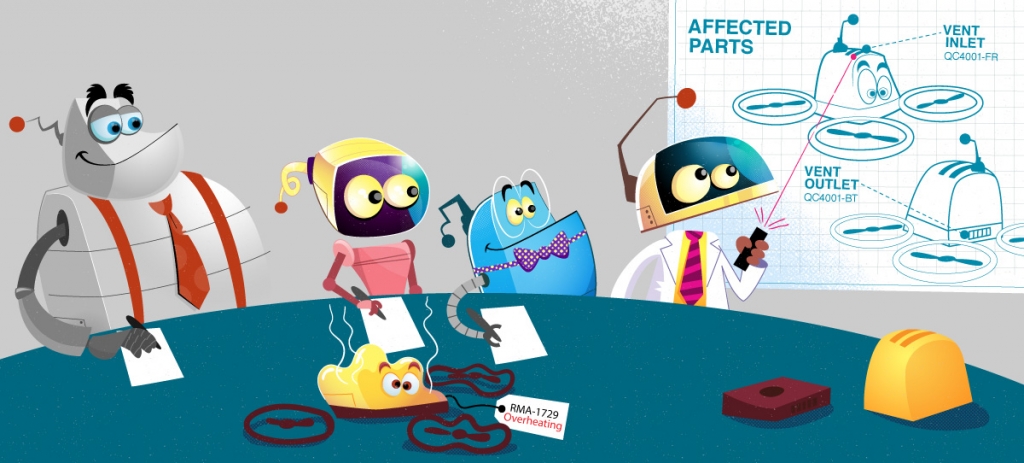
Larger manufacturing organizations employ a number of advanced processes to manage production operations. The processes help guarantee efficiency, quality, and on-time delivery. For smaller firms, these systems tend to be too burdensome to make sense implementing – until things get out of hand. Keeping track of product and material changes is one of those processes.
When production orders are small, or products are simple to build, adopting an Engineering Change Management (ECM) system may be more work than it’s worth, but how would a firm know when it’s time to seriously consider an ECM system for their operations?
Knowing the signs
A company may need to adopt an ECM system when it identifies certain signs or experiences challenges that indicate a lack of control and efficiency in managing engineering changes. Reaching into our over 15 years of experience of developing and implementing manufacturing systems, we’ve outlined some common signs that suggest the need for an engineering change management system:
Increasing Engineering Change Frequency
If the company experiences a high volume of engineering changes or change requests, it can become challenging to manage them effectively without a formalized system.
Increasing Production Delays
Unplanned or poorly managed engineering changes can lead to production delays, causing disruptions in the manufacturing process and potentially impacting delivery schedules.
Difficulty Managing Quality Issues
Inconsistent or improperly implemented engineering changes can lead to product quality issues, resulting in increased rework, customer complaints, or even recalls.
Lack of Change Visibility
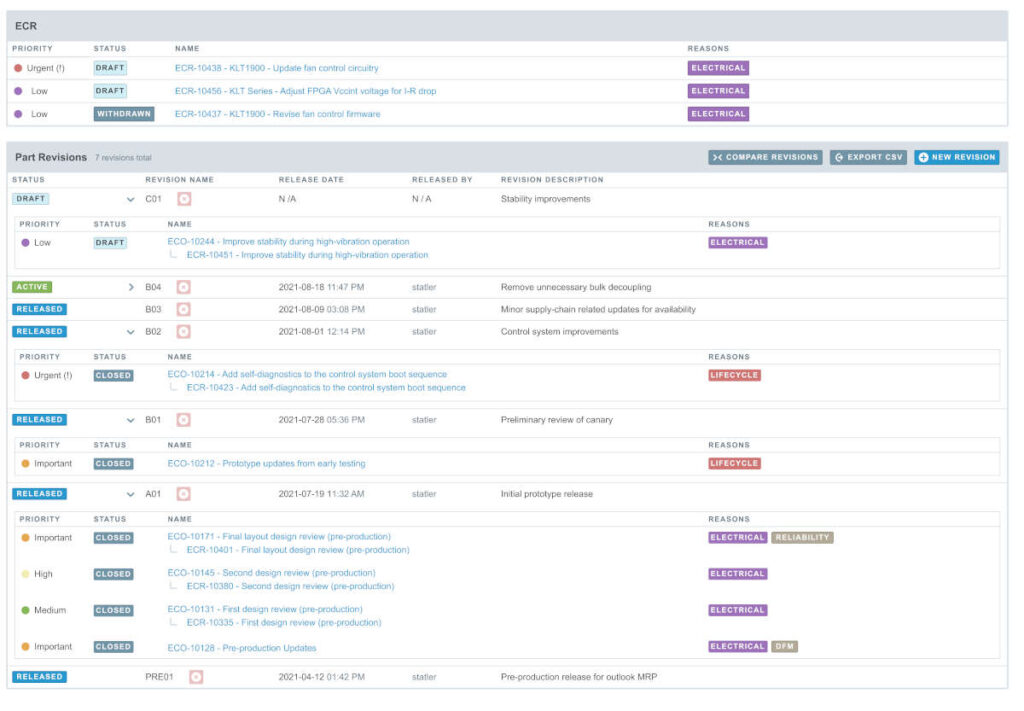
Without a centralized ECM system, it may be challenging to track the status of engineering changes. This situation leads to a lack of visibility into change requests, approvals, and implementation.
Document Control Problems
Difficulty in managing and versioning engineering documentation can lead to confusion about which version of a design or process is current and approved. This costs time to sort out and eventually money, when errors happen from this confusion.
Compliance and Regulatory Challenges
Companies in regulated industries may struggle to maintain compliance with industry standards and regulations without a structured ECM process in place. Losing track of what’s in compliance or within specifications could lead to chargebacks and missed deadlines.
Inefficient Change Review and Approval
A lack of a standardized process for reviewing and approving engineering changes can result in delays, duplicated efforts, and inconsistent decision-making.
Frequent Cost Overruns
Poorly managed engineering changes can lead to unexpected costs, such as rework, scrap, or additional raw material purchases, which can impact the company’s profitability.
Ineffective Communication
Inadequate communication among cross-functional teams involved in the change process can hinder collaboration and lead to misinterpretations, missed deadlines, or more rework and scrap.
Lack of Auditable Records
Without a formal ECM system, it may be challenging to maintain auditable records of engineering changes, which can be crucial during customer audits or for regulatory compliance.
Difficulty in Scaling Operations
As a company grows or diversifies its product portfolio, managing engineering changes manually becomes increasingly challenging and error-prone. This steals time and energy away from growth.
If a company is experiencing one or more of these signs, it’s an indication that implementing an Engineering Change Management system would likely bring significant benefits. An ECM system can help the company gain better control over change processes, improve collaboration, reduce errors, enhance product quality, and ensure compliance with industry standards and regulations.
Getting more from a combined ECM and MRP solution
While firms could strike out on their own and build a homegrown system or try standalone ECM systems, typically ECM systems are integrated into other business systems. For small and medium sized manufacturing companies, MRP and PLM systems like Aligni MRP and Aligni PLM provide ECR and ECO oversight along with other production and inventory management processes. Implementing an engineering change management system built into either PLM or MRP offers a lot of flexibility and benefits standalone or homebrew systems cannot easily provide.
To give some background, MRP systems are responsible for planning and managing the materials and resources needed to produce products, ensuring that production schedules align with demand and inventory levels are optimized. Integration between MRP and ECM is highly beneficial for maintaining accurate and efficient manufacturing processes. This integration ensures that all departments involved in the manufacturing process are working with the most up-to-date information, reducing the risk of errors, production delays, and excess inventory.
Ultimately, the seamless integration of MRP and ECM operations optimizes the manufacturing process, enhances collaboration between engineering and production teams, and enables manufacturers to respond quickly to changing market demands and product improvements. Implementing both systems at the same time also makes good business sense. If a manufacturer begins to need ECM functionality, the expanded functionality MRP provides will be necessary as well.
If the product or material change management issues are on the list above, it’s time to explore Aligni MRP. Try out our demo for free or sign up online today to get started!