Question:
I have a part (actually multiple parts) that can be made by 2 different manufacturers: in-house and an outside source. Parts from both sources are functionally identical and treated as interchangeable in assemblies. What is the best way to handle this? Is it possible to have a part with multiple manufacturers? Could I create two parts and have Aligni treat them as interchangeable?
– H.D. at Overwatch Imaging
Answer:
The short answer is to use Aligni’s Part Alternates feature. Here’s a bit more detail…
You’ll get the most out of Aligni if you maintain your database to be consistent with Aligni’s Manufacturer / Vendor relationships model. In summary:
- Every item (part) has a unique Aligni P/N (SKU)
- Each item has a single manufacturer
- Each item’s manufacturer P/N is unique to that manufacturer
- Each manufacturer has one or more vendors
In this post, we consider two distinct situations in the current case because the two situations justify different treatment within Aligni:
- Two commodity parts are manufactured by two different manufacturers that are functionally equivalent. An example of this would be electronic resistors.
- One part is specified but is manufactured by two different service providers. An example of this would be a machined part built-to-spec by a machine house.
Part Alternates are shown and managed on the details tab of the Part page. This part in our online demo database is a good example with three part alternates defined.
First Case: Different Manufacturers
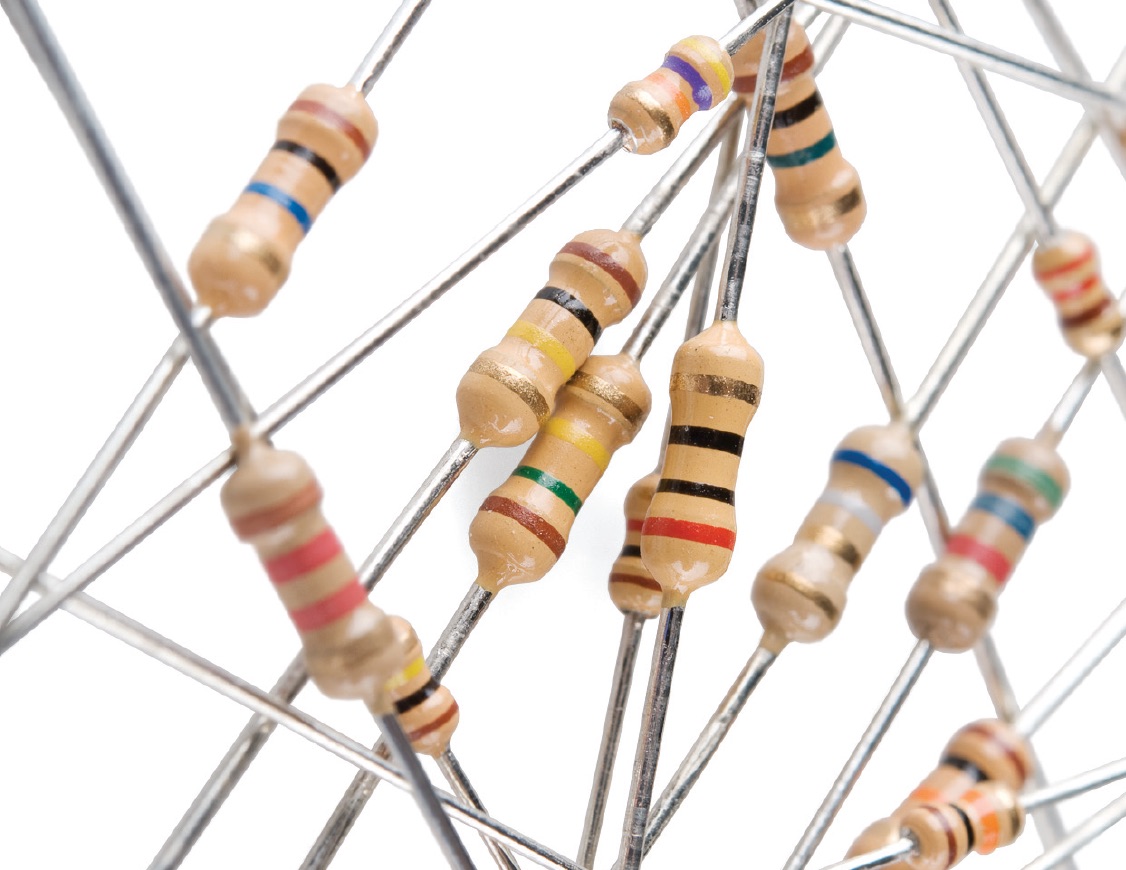
In the first case, let’s consider two electronic resistors that are manufactured by two different manufacturers. In the electronics industry, these are commodity parts that are available from many sources. They are sometimes colloquially referred to as “jelly bean” parts and are often considered “generic”. However, on our Part Alternates documentation page, we caution against configuring these parts in Aligni as generic.
So per our suggestion, these two parts would get separate Aligni part records, each associated with its respective manufacturer. You would then associate the parts to each other using Aligni’s Part Alternates. You have two options for this association:
- Equivalent – This means that two parts are suitable for any installation. They have identical parameters and differ only by manufacturer.
- Alternate – This means that two parts are similar, but substitution requires consideration.
At this point, the choice becomes industry or application specific — your organization will need to decide to what level “functionally identical” may be interpreted. For example, components intended for spaceborne instruments may be functionally identical to others for terrestrial applications, but may require special consideration for use in space.
Second Case: Generic Manufacturers
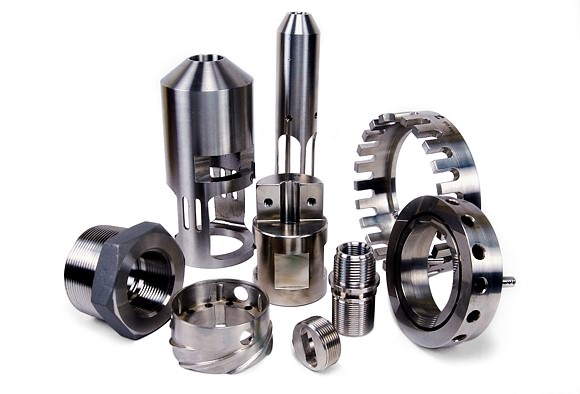
Let’s consider a different class of part, machined parts, and suggest one possible way to set things up for that scenario. Here, you’re the designer of the part and you provide drawings, schematics, and other specifications about how the part will be constructed. You provide this information to a machine shop and they build the part to your specifications.
To best fit the Aligni relationships model, we’ll create a manufacturer called Generic Machined and we may have multiple vendors (machine shops) associated with this manufacturer. With the relationships defined this way, RFQs and POs entered in Aligni can be routed correctly to your machine shop vendors when you have parts for this Generic Machined manufacturer.
When setup this way, there really is no need to use Aligni’s Part Alternates feature. In fact, it cannot be used since there is only one part in consideration.
Inventory, SKUs, and Nuance
The astute reader will recognize an important nuance in the results achieved by the two approaches above. Notably, in the first approach, we end up with two Aligni parts (SKUs) that will be inventoried separately whereas, in the second approach, we have two vendors for the same Aligni part and therefore only one SKU.
In the first case, we decided that it was important to keep the items separated. This is open to debate, but we feel that it is not good practice to use generics in this situation. Here are some reasons to consider:
- Buyers should not be making engineering decisions. While the specifications may be identical to a buyer’s eye, an engineer may think differently. The results of an incorrect application can range from benign to havoc in the final product: loss of performance, field failures, reduced lifetime, expensive rework, or scrapped material.
- Separate parts should be lifecycle managed separately. Two manufacturers operate differently and likely have very different schedules for obsolescence or other lifecycle events such as engineering change notifications. As separate parts, these can be monitored more easily and reliably.
- Partner communication is more precise. When generics are used, there can be some ambiguity when communicating a BOM to manufacturing partners. Since parts and packaging is typically marked with the manufacturer’s information it makes sense to have BOMs reflect these markings.
- Traceability. With two separate part records, everything from RFQ to purchasing to builds and inventory is tracked more accurately. If you ever need to review or audit for usage, you’ll know exactly which parts were used for which assemblies.
The second case is a good example of a legitimate and unambiguous use of generics. In this case, the generic manufacturer is an abstract concept used to fit operational behaviors to the Aligni relationship model but without compromising efficiency or clarity. If the two machine shops can genuinely create parts that are form, fit, and function compatible, then their outputs can be mixed in inventory and they should fall under the same SKU.
Start your 30-day free trial
Helping You Make Great Things…Better.