Focus on Building Better Products
Quality control is a critical part of delivering any product or service. From ensuring the final product is free of defects (Quality Control) to creating robust processes to prevent defects in the first place (Quality Assurance), quality drives customer satisfaction, operational efficiency, and brand reputation.
Today, we are excited to announce Aligni’s new quality control feature, designed to streamline quality management and seamlessly integrate with existing MRP and PLM workflows.
Whether upgrading from outdated (or ad-hoc) systems or simply seeking a fresh approach, this quality control feature provides guidance and flexibility to meet the needs of both small businesses and scaling operations.
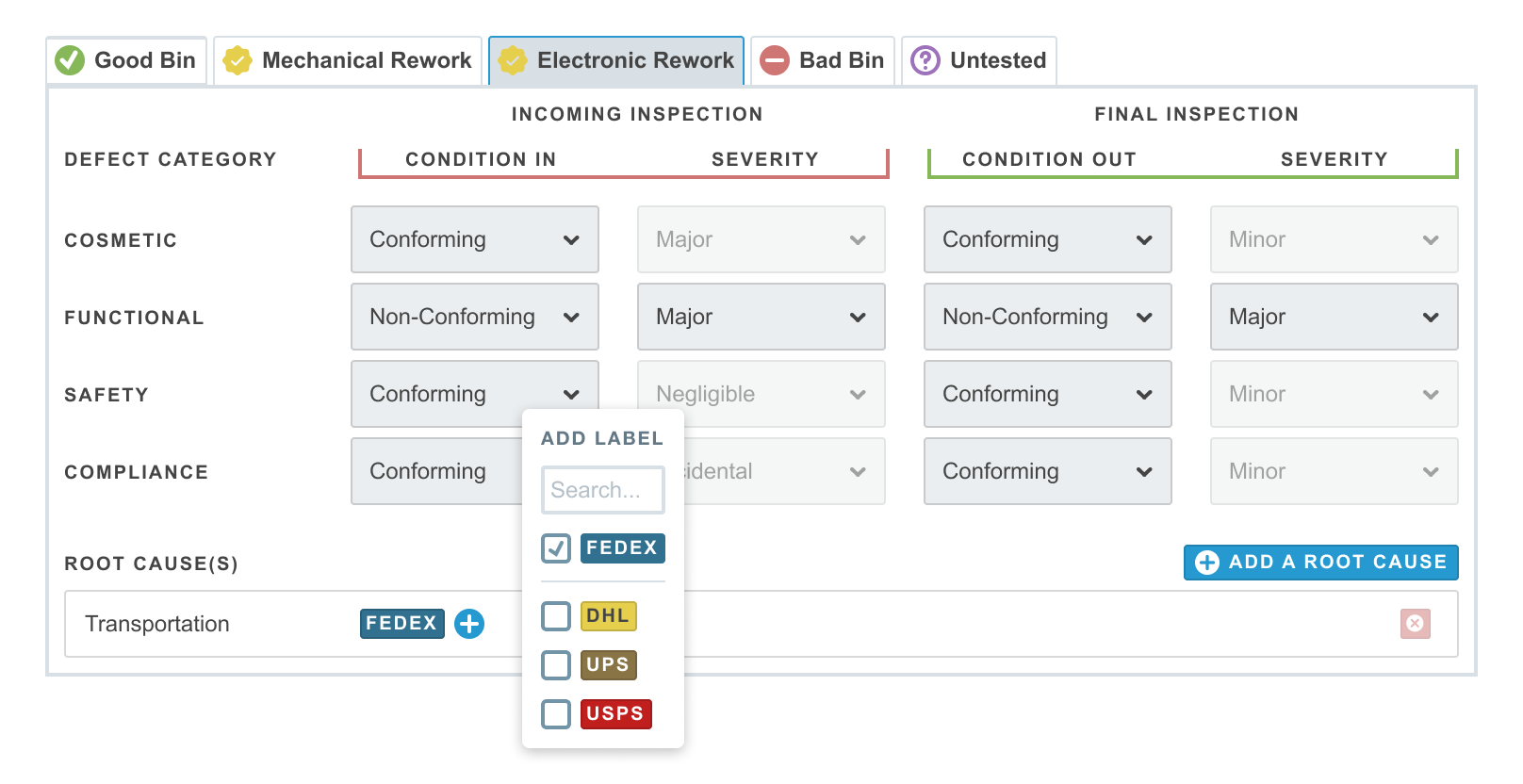
Fresh Approach to Quality
Most MRP quality control implementations feel like an afterthought—a bolted-on implementation intended to check a box. In collaboration with a key customer, we built Aligni’s approach from the ground up on three core objectives:
- Enhance collaboration
- Document process outcomes
- Aggregate results for analytics
By focusing on critical insights like inspection results, defect root causes, and material dispositions, we empower teams to unlock a deeper understanding of process performance — all through a platform that’s easy to use and enjoyable to work with.
Focus on Collaboration
Quality control activities often involve contributions from multiple teams: production, design, engineering, procurement, and quality. In designing Aligni QC, we focused on improving this coordination with centralized collaboration tied to the existing item master, build schedule, and procurement activities for more efficient communication and better record keeping.
This focus gives production, engineering, and testing teams an easy-to-use platform where everyone can stay on the same page. Better engagement means smoother operations and faster outcomes. Plus, every decision and chat gets logged automatically, so the organization always has a clear, digital paper trail for compliance and peace of mind.
QC discussions utilize the same engine as other records in Aligni for consistency and familiarity. With features like at-mentions, subscription options, attachments, and notifications, teams can stay connected and coordinate efficiently. Relevant events are also added to the activity timeline, providing valuable context at a glance.
Learn more about Aligni Discussions.

Documenting Process Outcomes
Aligni’s quality process breaks everything down into easy-to-follow states, stages, and categories, making quality management more straightforward. The flexible setup is perfect for growing teams, giving them the tools to create a solid digital paper trail while keeping everything visible, organized, and ready for seamless collaboration.
At its core, turning uncertainty into actionable outcomes is what quality control is all about. Materials are evaluated and sorted—conforming materials are approved, while non-conforming materials are either scrapped or flagged for rework or repair. Along the way, records of the process provide valuable insights, helping to refine operations and drive continuous improvement. This streamlined approach keeps quality management clear, efficient, and focused on what matters most.
Learn more about the QC workflow.
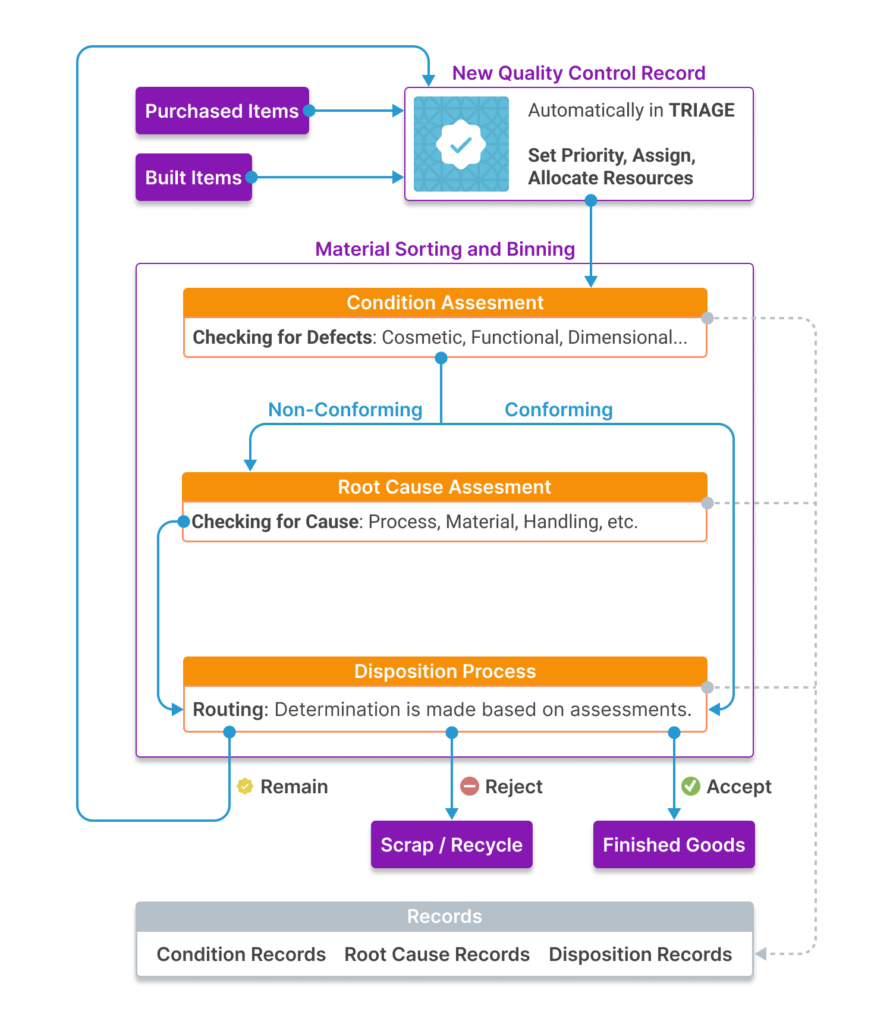
Historical records, like condition assessments and root causes, provide valuable insights into trends. And with a complete history of discussions, teams can resolve issues faster and stay ahead of future challenges. It’s all about using the past to help inform smarter decisions going forward.
Aggregating Results for Analytics
Aligni collects root cause records and “labels” providing additional granularity. These records can be used to develop insights about systemic failures, initiate design improvements for revisions or new products, and lessons learned for continual improvement in processes and training.
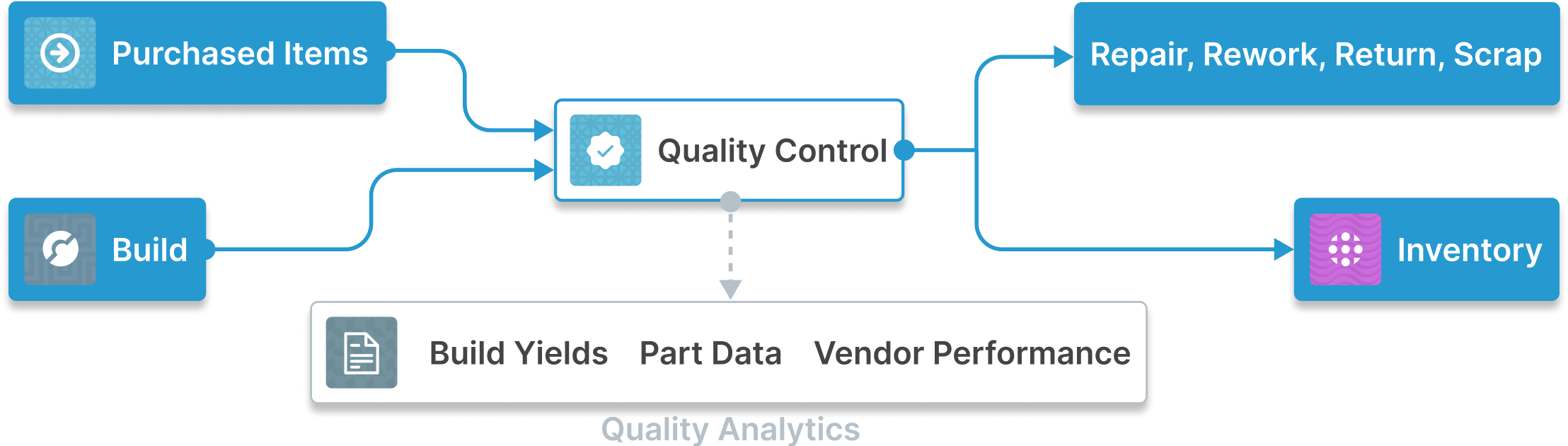
Seamless Workflow Integration
The QC module was designed to seamlessly integrating into existing day-to-day MRP and PLM workflows. Aligni connects quality management to design, planning, production, inventory, and supply chain, streamlining the entire process.
With intuitive features for quarantining, binning, labeling, and managing inventory, Aligni enhances inventory control and enables efficient quality assessments with just a few clicks.
Managing quarantine is a breeze with three simple ‘gates’ that fit right into an existing workflow: build finalization, inventory receipt, and manual movement into quality control. These checkpoints make sure products get a thorough review at key stages. When a Quality Control Report (QCR) is created, it starts in the Triage state, waiting for activation—so everything gets a careful look before moving forward.
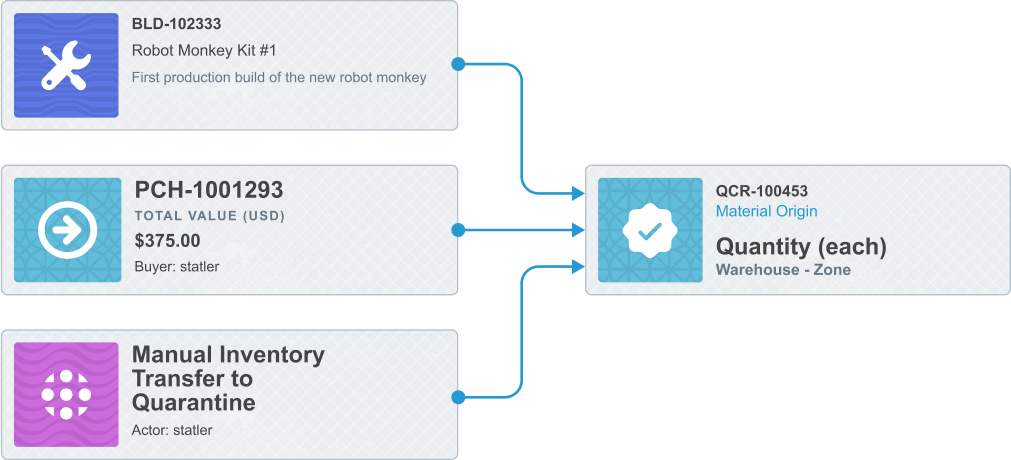
Sometimes the journey through quality control is complex. Effectively managing repairs, rework, and vendor returns requires good visibility of that material through its journey. We created a hierarchical status index to easily track material it is quarantine.
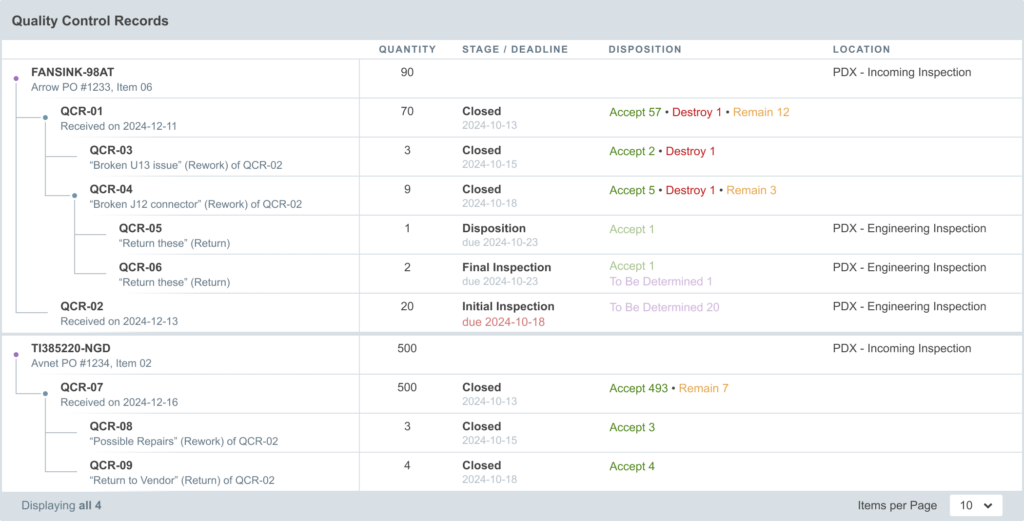
Quality control doesn’t work in a vacuum—it’s closely tied to inventory management, influencing how inventory moves through Aligni (and an organization). With a centralized database that connects products, suppliers, and production processes, users get real-time visibility and smooth tracking. This connected system ensures quality is maintained at every step, boosting inventory accuracy and helping manufacturing operations run more efficiently and reliably.
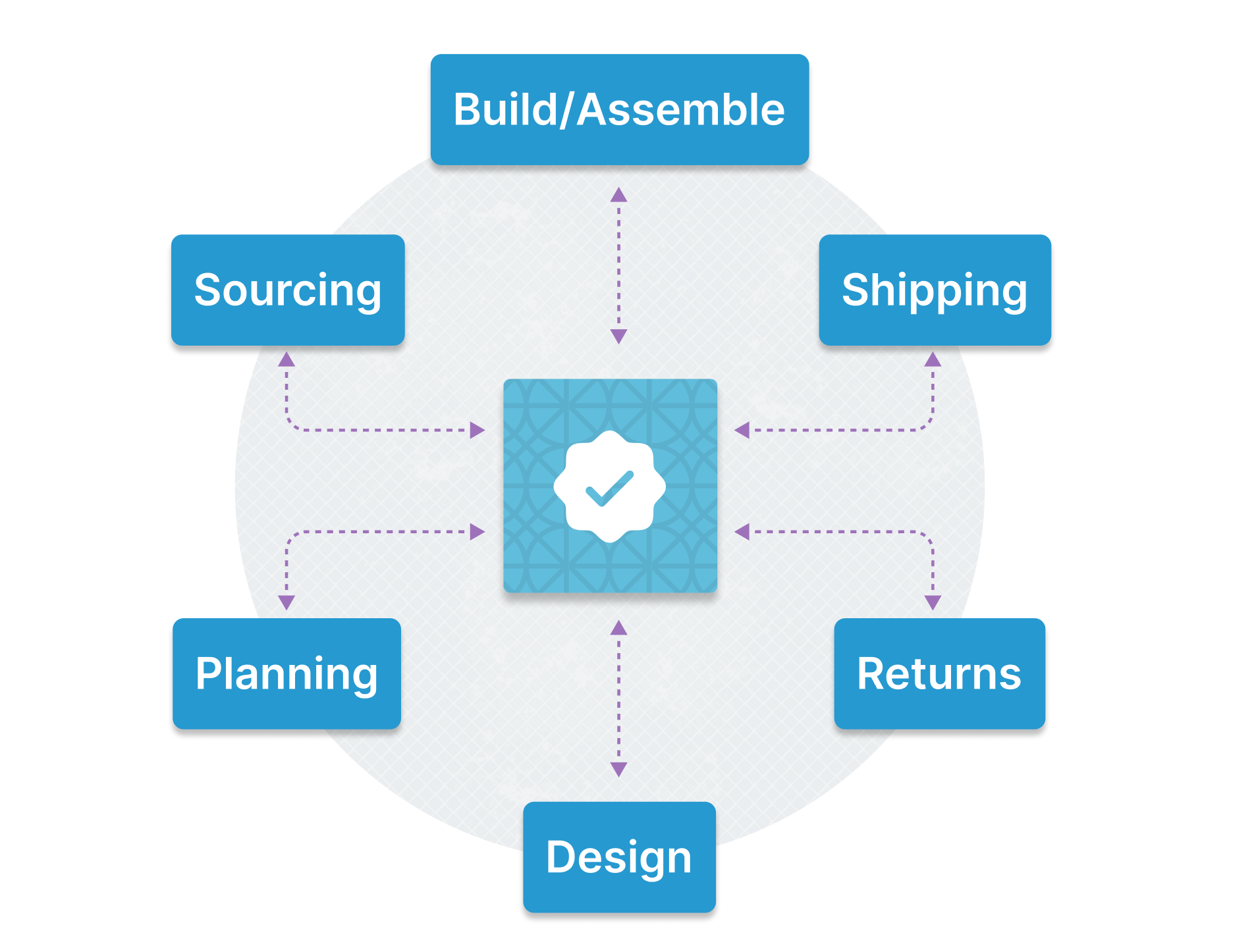
Introducing Quarantine Areas
To support the notion of segregated inventory (as required by ISO 9001:2015 and other quality management systems), we’ve introduced a new operations area for inventory warehouse zones: quarantine.
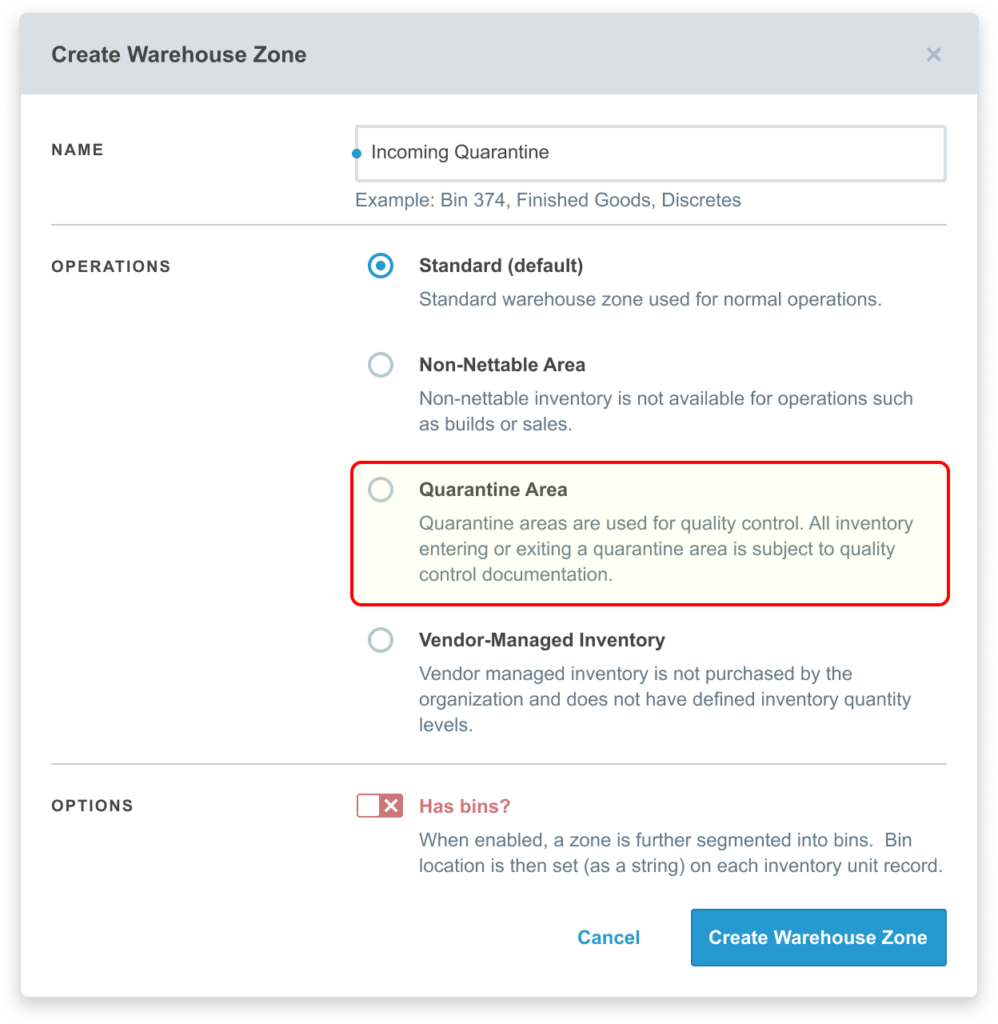
Quarantine areas have rules for entering and exiting them that help ensure that inventory undergoing quality control is unavailable to other processes but is still free to move within the organization and even between different warehouses.
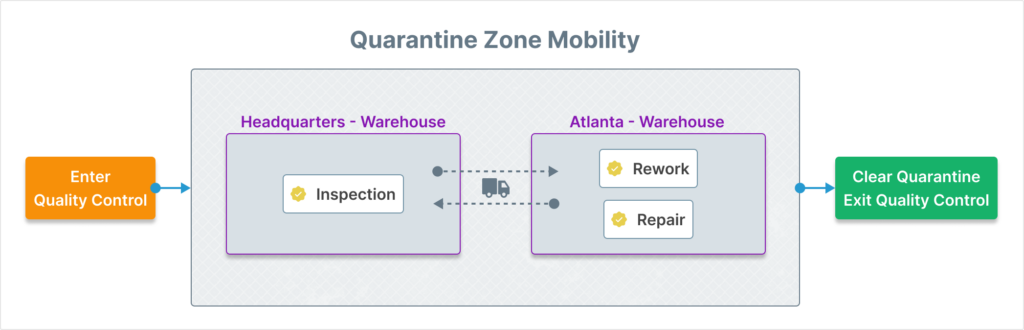
Simple for Small Teams, Flexible for Larger Teams
The perfect balance of structure and flexibility, Aligni’s quality control system adapts seamlessly to each team’s workflows. While some parts of the Quality Control Record (QCR) are standardized, organizations can define defect categories and severities to match their specific processes and products. These customizable categories power analytics and material decisions, ensuring quality control metrics are precise and relevant.
Aligni’s quality control workflow is designed to align with each company’s unique processes, enabling them to track essential data across a range of areas, including compliance documentation, root cause analysis, and vendor performance. With built-in best practices and sensible defaults, we’ve ensured that organizations can get up and running quickly.
Learn more about QC defaults and configuration.
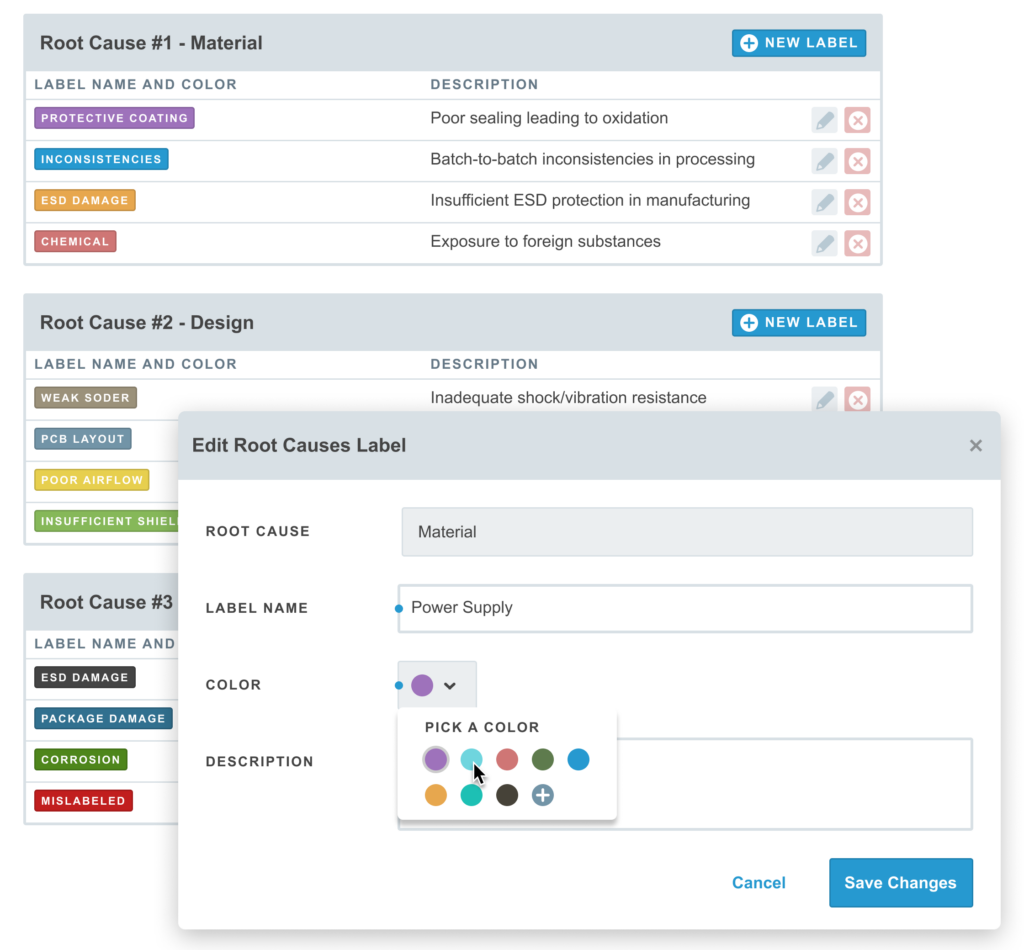
Looking to dive a bit deeper?
Check out the rest of our documentation to learn more about Quality Control, including but not limited to: