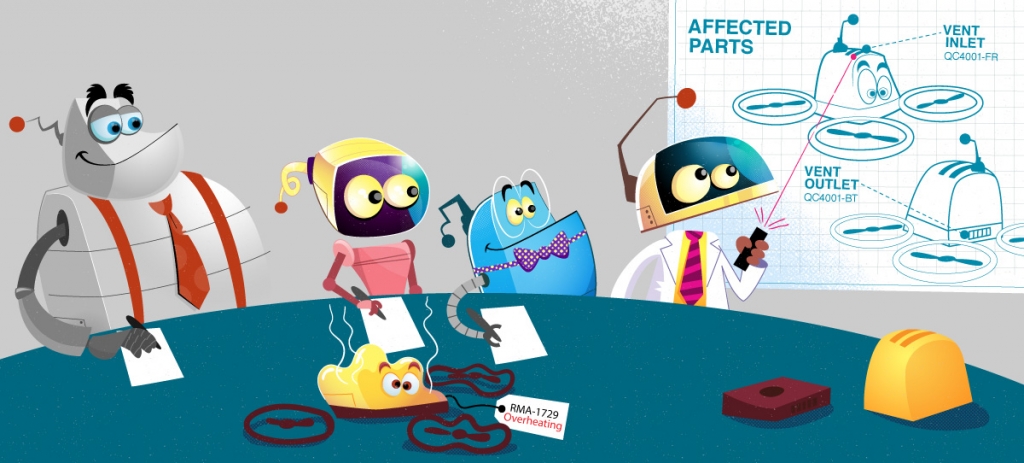
Collaboration is often touted as the solution for business performance issues. Increasing that collaboration seems to be something that’s easier said than done. Many end up scheduling more meetings in the hope that better interaction improves results. A better solution might be to focus on the details of the manufacturing process and work to share those more effectively. One area where that can occur is managing Bills of Materials (BOMs).
Departments in a manufacturing company collaborate on bills of materials by sharing and utilizing BOM data as a central reference point. The engineering and design department creates the initial BOM, which is then shared with other departments such as production, procurement, and quality control. Production relies on the BOM to plan manufacturing processes, procurement uses it to source materials, quality control establishes standards based on it, and finance calculates production costs. Sales and marketing teams leverage BOMs to understand product configurations, while maintenance and repair teams use them for service planning.
Effective communication and data sharing among these departments ensure that BOMs accurately represent the product’s composition, meet quality standards, and support efficient production processes, ultimately contributing to the company’s success in delivering quality products to customers. This is what makes BOM management an excellent place to start increasing collaboration.
Getting to know how BOMs are used
The first step in the process is understanding exactly how each department utilizes a BOM and what information they need from it to do their jobs well. We’ve broken out the broad strokes of how each department typically uses BOMs:
Engineering and Design
It all starts with engineering and design teams creating BOMs as part of the product development process. They use BOMs to define the structure of the product, specify components, and ensure that the design meets functional and quality requirements. BOMs serve as a blueprint for the product’s physical composition.
Production and Manufacturing
The production department relies on BOMs to plan and execute the manufacturing process. They use BOMs to determine the materials and components needed, establish assembly sequences, and allocate resources. BOMs guide production workers in assembling the product accurately and efficiently.
Procurement and Supply Chain Management
These groups use BOMs to identify the materials and components required for production. BOMs help in generating purchase orders for sourcing these items from suppliers. Additionally, supply chain management uses BOMs to track inventory levels, manage lead times, and optimize the supply chain for timely material availability.
Quality Control and Assurance
Quality control and assurance departments refer to BOMs to establish quality standards and inspection criteria for each component and assembly step. BOMs provide a basis for quality checks and ensure that the final product meets predefined quality specifications.
Maintenance, Warranty, and Repairs
Maintenance and repair teams refer to BOMs to identify components and parts that may require maintenance or replacement during the product’s lifecycle. BOMs assist in maintaining equipment and ensuring product longevity. Warranty claims are compared against the parts lists to determine whether alternate components should be used to lower repair costs.
Documentation and Compliance
BOMs serve as critical documentation for compliance with industry regulations and standards. Regulatory departments use BOMs to verify that products meet safety, environmental, origination, and quality standards.
Sales and Marketing
Sales and marketing teams may use simplified BOMs to understand product features and configurations. BOMs help them communicate product details to customers, provide accurate quotes, and tailor sales pitches to meet customer needs.
Cost Accounting and Finance
Cost accounting and finance departments rely on BOMs to calculate the cost of producing a product accurately. BOMs provide a breakdown of material costs, labor costs, and overhead, helping in cost estimation, budgeting, and pricing decisions.
As can be seen, BOMs are integral to the functioning of a manufacturing company, serving as a common reference point that different departments use to fulfill their specific roles and responsibilities, ultimately contributing to efficient and quality production processes. This makes bills of materials an excellent candidate for increasing an organization’s collaborative capabilities, but what holds a company back from doing it?
The right tools for the job
The biggest factor that holds up BOM collaboration is not having the proper platform to share information through, as many firms still rely on spreadsheets to manage their parts lists. This causes a number of issues.
Collaborating with spreadsheets can be challenging due to inherent limitations in spreadsheet software. Firstly, version control becomes a significant issue when multiple users need to edit the same spreadsheet simultaneously. Without a clear mechanism to manage changes and track revisions, it’s easy for errors to propagate, leading to data inconsistencies and confusion about which version is accurate. This lack of version control also makes it difficult to maintain an organized and reliable record of changes made by different team members.
Secondly, data integrity is a concern when using spreadsheets for collaboration. Human errors, such as accidental data deletion or formula modifications, can occur frequently, particularly in complex spreadsheets. These errors can compromise the accuracy of the data and calculations, potentially leading to incorrect decisions and actions based on flawed information. Moreover, without stringent access controls and audit trails, ensuring the security and accountability of sensitive data in shared spreadsheets can be challenging, posing risks in terms of data privacy and compliance.
Getting a BOM collaboration hub
To get around spreadsheets’ limitations, many manufacturing firms employ purpose-built software to manage and provide access to their BOMs. That software tends to be a Material Requirements Planning (MRP) system.
An MRP plays a pivotal role in enhancing collaboration on BOMs within a manufacturing company. It provides a centralized platform where departments can access and work on a single, up-to-date version of the BOM. This eliminates the issues associated with using outdated or conflicting BOM versions typically found in spreadsheets. This fosters a unified understanding of product structure. Cross-functional teams, including engineering, production, procurement, and quality control, can simultaneously view and update the BOM, ensuring that it reflects the most current information. This real-time collaboration streamlines communication, minimizes errors, and reduces the need for manual data sharing and reconciliation, fostering a more efficient and synchronized workflow.
Secondly, MRP systems often offer role-based access control, allowing departments to access only the BOM information relevant to their responsibilities. This security feature ensures data integrity and confidentiality while encouraging focused collaboration. Departments can work on their specific aspects of the BOM while trusting that other teams are doing the same, leading to increased productivity and better utilization of expertise. Additionally, MRP systems can track and document changes to the BOM, providing a transparent history of modifications and their justifications. This not only aids in collaboration but also supports accountability and effective change management, ensuring that all stakeholders are aligned and informed throughout the product lifecycle.
Overall, an MRP system acts as a unifying platform that promotes collaboration, efficiency, and accuracy in BOM management across diverse departments within a manufacturing organization. If you’re looking to increase your interdepartmental collaboration, start with managing your BOMs in Aligni MRP!
Start your 30-day free trial
Helping You Make Great Things…Better.