When businesses move away from struggling to run themselves through spreadsheets, the first purpose-built system they reach for is Material Requirements Planning (MRP). For many businesses, MRP systems act as the hub for product, production and inventory management. It connects production, quality, engineering, and purchasing departments through a combined item master database. The question is what do companies store in the item master?
The answer is: a lot. When done properly, the data is collected from across the organization.
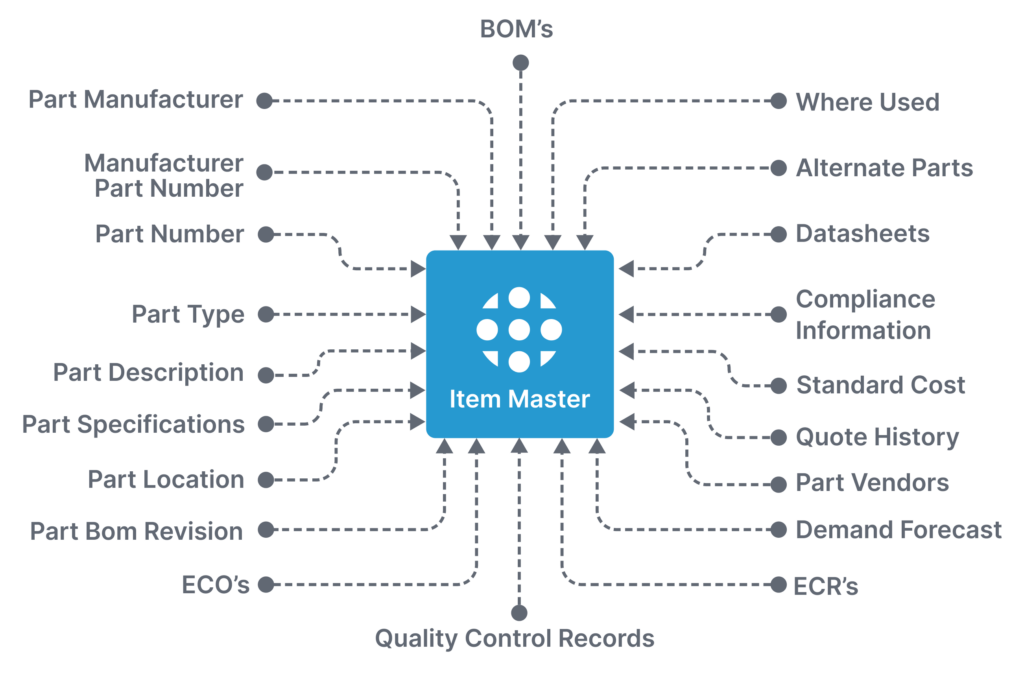
Each department contributes specific information to the MRP product database based on their respective roles and responsibilities. This collaboration on product, supply chain, and production information is core to the value provided by MRP systems.
To take a deeper dive into the types of information, we’ve outlined the more common data successful companies store and operate on within an MRP system and the departments that provide and maintain it.
Engineering Department:
- CAD Models and Drawings: The engineering department contributes CAD models, assemblies and subassemblies, 2D drawings, and associated files that represent the design and technical specifications of the product.
- Product Specifications: The engineering department adds product specifications, including functional requirements, performance criteria, design guidelines, and other technical details that define the characteristics and behavior of the product.
- Design Changes and Revisions: Engineers contribute information about design changes, updates, and revisions made during the product development process. This includes documenting the reason for the change, the affected components, and the updated specifications or drawings.
- Bill of Materials (BOM): The engineering department provides detailed BOMs that list all the components, sub-assemblies, and raw materials required to build the product. This includes part numbers, descriptions, quantities, potential vendors, and any associated specifications or parameters.
Purchasing Department:
- Supplier Information: The purchasing department provides data on approved suppliers/vendors. This includes supplier names, contact information, lead times, pricing agreements, and preferred supplier rankings.
- Supplier Contracts and Agreements: They contribute contract and agreement documentation related to procurement activities such as supply contracts, service level agreements (SLAs), and non-disclosure agreements (NDAs).
- RFQs, Quotes, & Purchase Orders: The purchasing department adds information about purchase orders raised for procuring materials, components, or services. This includes purchase order numbers, quantities, delivery dates, pricing, and supplier details. Systems like Aligni MRP also make that data available for analysis to find historical trends and be better prepared for changes going forward.
Manufacturing Department:
- Work Center Information: The manufacturing department provides data on their capacities, capabilities, and scheduling constraints.
- Routing Information: They contribute routing information that defines the sequence of operations and processes required to manufacture the product. This includes details such as operation codes, machine requirements, labor resources, and standard times for each operation.
- Production Schedules: The manufacturing department provides information on planned production schedules, including start and end dates, quantities, and resource allocations for each manufacturing order or batch.
Quality Department:
- Inspection Requirements: The quality department contributes data on inspection requirements for materials, components, and finished products. This includes quality control specifications, testing criteria, and sampling plans from the organization’s Quality Assurance process.
- Quality Metrics and Non-Conformance Data: They also provide quality control data related to quality inspections, test results, non-conformance reports (NCRs), engineering change management processes, and any other quality-related information generated during the manufacturing process.
This outline only provides a general overview of the data found in an MRP system. The amount of data stored within an MRP system can vary according to the processes and requirements of each production operation, as well as how deeply a company plans to integrate the system. Many firms spend time and effort to customize the fields within the system to more accurately match their current processes.
Each department’s contributions to the MRP product database are vital for accurate material planning, production scheduling, and inventory management. By incorporating their specific data into the MRP system, it enables effective coordination and optimization of the supply chain processes. This ensures the right materials are available at the right time to meet production requirements while considering supplier lead times, engineering changes, and quality control measures. When all these departments work from the same data sets, firms find reduced errors and more throughput from the same operations.
Ready to connect all your departments with a single source of truth? Then it’s time to migrate to a purpose-built product and inventory management system. It’s time to sign up for Aligni MRP!
Start your 30-day free trial
Helping You Make Great Things…Better.