Managing change across the supply chain and the shop floor is an intensive process. Engineering Change Management (ECM) touches many aspects of each area. It involves several departments and groups within the organization. The process, when done correctly, also requires managing a large amount of information across several stages. With all of this in mind, it is no wonder why efficient production operations rely on purpose-built software to manage their ECM processes. For most small and medium sized businesses that software is their MRP system.
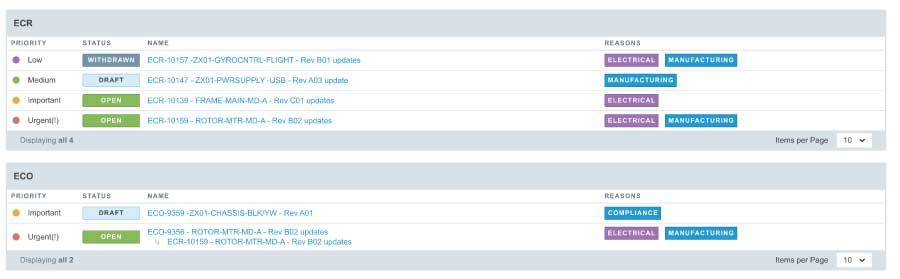
For those ready to level-up their product management, we’ve outlined the steps within the ECM process. This will provide a good understanding of why many firms rely on the system, as well explain in more detail the data and processes involved that need to be managed. This naturally leads to the need for a software solution to manage it well and why that software should be an MRP system, like Aligni MRP.
How the ECM Process Works for Manufacturing Products
The Engineering Change Management (ECM) process for manufacturing products is a structured approach used to handle changes and improvements to product designs, processes, materials, or other elements during the manufacturing lifecycle. It ensures that changes are evaluated, approved, and implemented effectively while minimizing disruptions to production and maintaining product quality. Here’s a step-by-step overview of how the ECM process typically works in manufacturing:
1. Initiation of Change Request (ECR)
The process begins with the identification of a need for change. This could be due to various factors such as product defects, customer feedback, design improvements, cost reduction opportunities, regulatory compliance, or supply chain issues. A formal Engineering Change Request (ECR) is initiated, providing detailed information about the proposed change.
2. ECR Review and Impact Analysis:
Cross-functional teams, which may include representatives from engineering, manufacturing, quality control, procurement, and other relevant departments, review the ECR. They perform a comprehensive impact analysis to assess how the proposed change will affect product functionality, cost, manufacturing processes, supply chain, and compliance.
3. Risk Assessment and Mitigation
Identified risks associated with the proposed change are assessed, and mitigation strategies are developed to address any potential negative impacts on product quality, production schedules, or costs.
4. Approval Process
The ECR goes through an approval process that may involve various stakeholders, including engineering managers, product managers, quality assurance, and even regulatory compliance personnel, depending on the nature of the change. Appropriate approval authority levels and workflows are defined based on the complexity and potential impact of the change.
5. Engineering Change Order (ECO) Creation
If the ECR is approved, it is translated into an Engineering Change Order. The ECO contains detailed instructions for implementing the change, including updates to design documents, bill of materials (BOM), manufacturing instructions, and any other relevant documentation.
6. ECO Review and Final Approval
The ECO is reviewed by the necessary stakeholders to ensure all aspects of the change are accurately documented. Final approval is obtained, signifying that the change is ready for implementation.
7. Implementation and Verification
The approved change is implemented in the manufacturing process. Verification steps may include testing, quality checks, and validation to ensure the change has been successfully integrated without introducing new issues.
8. Documentation and Communication
Comprehensive records of the change, including the ECR, impact analysis, approval documentation, and the final ECO, are maintained. The change is communicated to all relevant parties, including manufacturing teams, supply chain partners, and quality control.
9. Continuous Improvement
After implementation, the impact of the change is monitored, and feedback is gathered to assess the success of the ECM process and identify opportunities for further improvement.
Throughout the ECM process, communication, collaboration, and documentation play vital roles in ensuring that changes are managed efficiently while maintaining product quality, meeting regulatory requirements, and optimizing production processes. This point is the reason for using purpose-built software to manage the engineering change process more effectively – MRP. These systems also provide many more advantages beyond pure ECM.
But First, What is an MRP System?
A Material Requirements Planning (MRP) system for manufacturing is a software system that streamlines the management of production-related activities. It helps manufacturers effectively plan, schedule, and control the procurement and production of materials and components needed to meet customer demand.
The MRP system, like Aligni MRP, uses data from various sources, such as sales forecasts, customer orders, inventory levels, and lead times, to generate a comprehensive production plan. The system then breaks down the plan into detailed material requirements by analyzing the Bill of Materials (BOM) for each product. It calculates the net requirements for raw materials and components by considering the available inventory, scheduled receipts, and safety stock levels. The MRP system generates recommendations for purchase orders and production orders, ensuring that the right materials are available at the right time to meet production schedules and customer demand. In some systems, like Aligni MRP, it helps manage vendors and the purchasing process, as well.
In short, MRP systems optimize production planning, minimize inventory costs, and improve overall operational efficiency for manufacturing companies. Since an MRP is deeply intertwined with both production and inventory management, this interconnectedness makes it the perfect system to manage engineering changes to products, parts, and materials.
Why Use an MRP System to Manage ECM?
Using a Manufacturing Resource Planning system to manage the Engineering Change Management process offers manufacturers several significant benefits. Firstly, MRP systems streamline the material and resource planning aspects of ECM, ensuring that changes introduced through the ECM process are seamlessly integrated into production plans and material requirements. This integration helps prevent material shortages or excess inventory, optimizing inventory levels, and reducing carrying costs. By maintaining accurate and up-to-date material data, MRP systems ensure that engineering changes are reflected in the bill of materials and lead times, reducing the risk of production delays and disruptions.
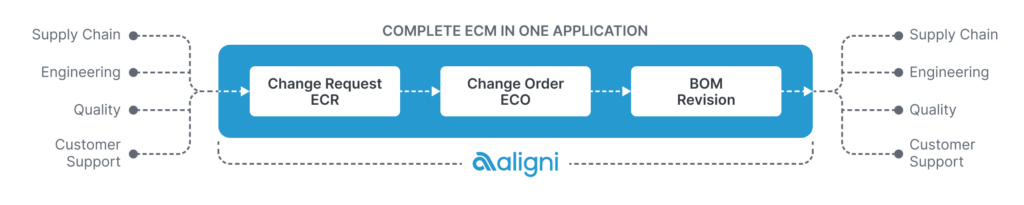
Secondly, MRP systems enhance visibility and coordination between the ECM and production planning teams. The ability to incorporate approved changes directly into the production schedule ensures that the shop floor is aligned with the latest product designs and process modifications. This alignment minimizes the chances of manufacturing products based on outdated specifications, leading to higher product quality and reduced rework. Additionally, the MRP system’s capacity planning capabilities allow manufacturers to assess resource availability, helping determine if the manufacturing facilities have the capacity to accommodate the increased demand or any changes introduced through the ECM process. This coordination between engineering and production departments, facilitated by the MRP system, fosters collaboration, improves decision-making, and streamlines the implementation of approved changes, ultimately leading to more efficient operations and reduced lead times.
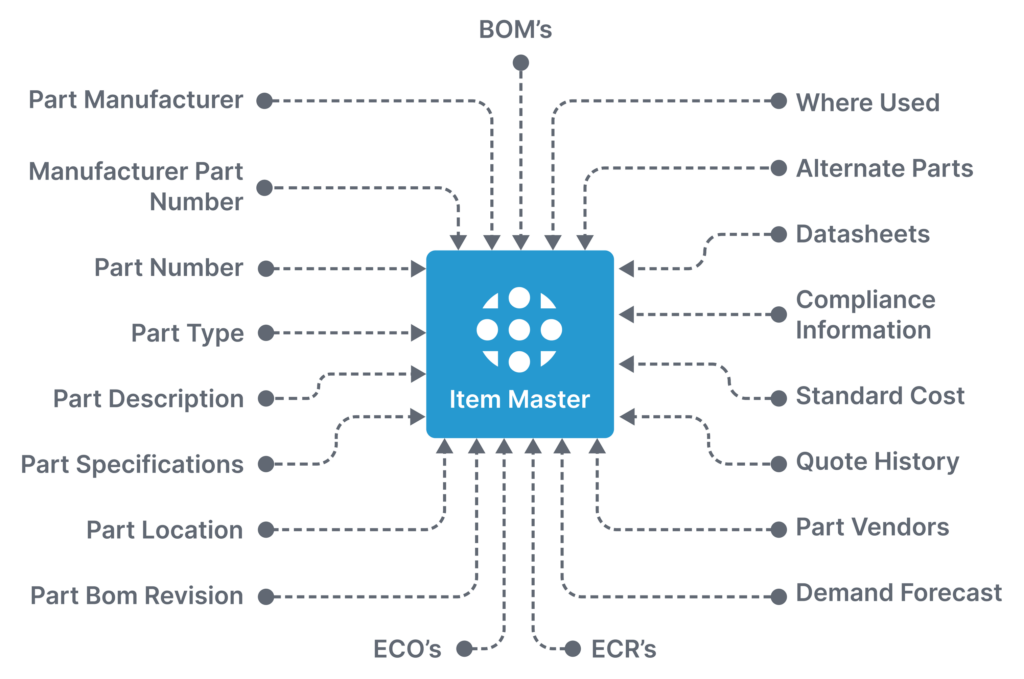
Perhaps the most important reason for managing ECM processes within an MRP system is how the system stores data. Material requirements planning systems are typically built upon an item master database. This centralized location for all production, inventory, and purchasing data makes it easy to not only retrieve information but to combine the data from across functional areas, as MRP systems are designed to be the hub for all the relevant groups. They play a crucial role in ensuring that material-related information is accurate, up-to-date, and integrated with production planning and inventory management, indirectly influencing the manufacturing ECM process for smoother implementation of approved changes. As any company who uses separate business systems or just a collage of spreadsheets to try and manage operations knows, this is a step-change in operational performance.
Leveraging an MRP system to manage the ECM process provides manufacturers with accurate material and resource planning, efficient production scheduling, and improved coordination between departments. These benefits result in reduced inventory costs, better utilization of resources, enhanced product quality, and increased agility in responding to engineering changes, making MRP an invaluable tool for manufacturers seeking to optimize their production processes while effectively managing product improvements and modifications.
If you’re looking to refine your change processes with ECM, then you should consider operating it through a materials requirements planning system. It’s time to sign up with Aligni MRP!
Start your 30-day free trial
Helping You Make Great Things…Better.