When a company gets to a certain scale of production, it becomes increasingly important to maximize its assets and resources. It has to make sure to count every minute of production time. A half hour of downtime is tough to deal with. A half-day or more is unconscionable.
The answer for many firms is to get strategic about all the operations that go into manufacturing their products. That means understanding the time it takes to build products, receive materials, and sketch out potential issues before they arise. All this information is installed within a manufacturing production plan. Manufacturing production plans serve as a blueprint for efficient, cost-effective, and high-quality production operations.
Why production plans?
Production plans offer a host of advantages to organizations in terms of operational efficiency and cost reduction. These plans optimize resource allocation, streamline processes, and minimize waste, resulting in lower operating costs and increased throughput. By aligning production with customer demand, they improve on-time delivery rates and enhance customer satisfaction. Additionally, production plans facilitate effective quality control measures, ensuring consistent product quality and reducing defects. They also assist in managing inventory levels efficiently, minimizing excess inventory and associated carrying costs.
These plans also contribute to risk mitigation by identifying and addressing potential disruptions in advance, thereby reducing their impact on production. They enable structured communication among departments, support continuous improvement initiatives, and provide a foundation for sustainability efforts. Compliance with industry regulations and quality standards is also facilitated.
With data-driven decision-making at their core, production plans empower organizations to make informed adjustments based on real-time data, fostering agility and adaptability. In essence, manufacturing production plans are indispensable tools that not only optimize operations but also enhance competitiveness, enabling organizations to meet customer demands swiftly and efficiently.
What goes into a production plan?
A manufacturing production plan should include a comprehensive set of details to guide the production process effectively. These details help ensure that production activities are coordinated, resources are allocated efficiently, and products are manufactured to meet quality and quantity standards. Here are the key details that should be included in a manufacturing production plan:
1. Production Schedule
Specify the production schedule, including start and end dates for each production order or batch. Detail the sequence of production for different products or product variants.
2. Product Specifications
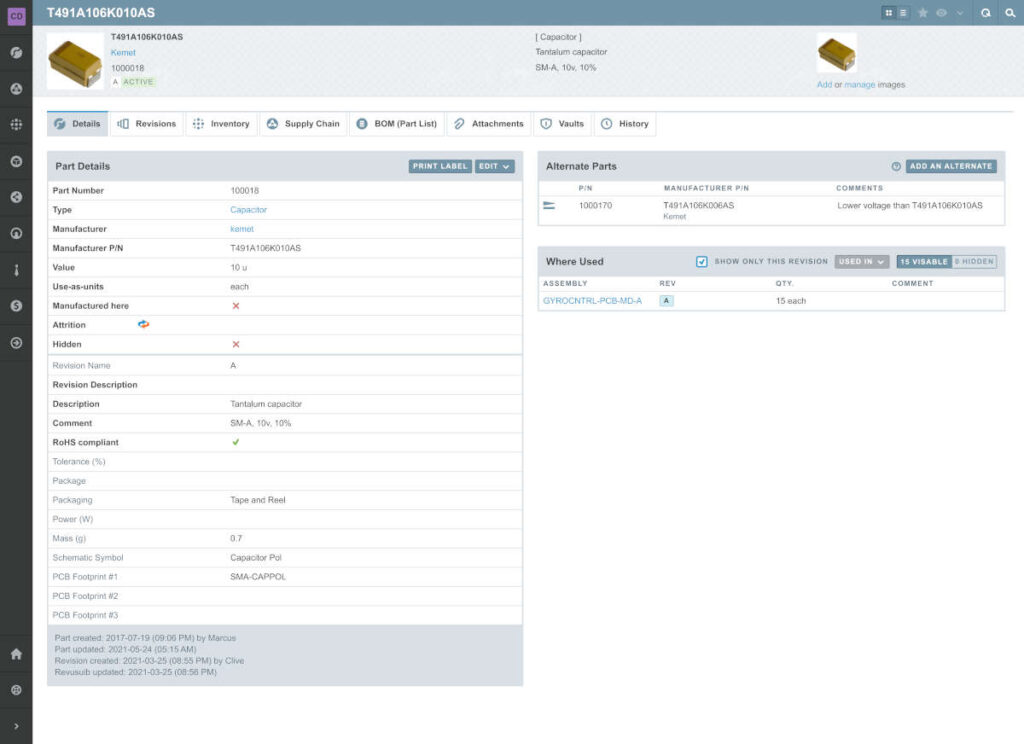
Provide detailed specifications for each product, including materials, components, dimensions, and quality standards. Include any special instructions or requirements for manufacturing.
3. Bill of Materials (BOM)
List all the materials and components required for each product or product variant. Include quantities, part numbers, and descriptions for each item in the BOM. Learn what goes into a BOM!
4. Routing or Process Flow
Outline the steps involved in the manufacturing process for each product. Include information about workstations, machinery, tools, and labor requirements for each step.
5. Resource Allocation
Specify the allocation of machinery, equipment, and labor to different production tasks. Include information on shift schedules and staffing requirements.
6. Inventory Requirements
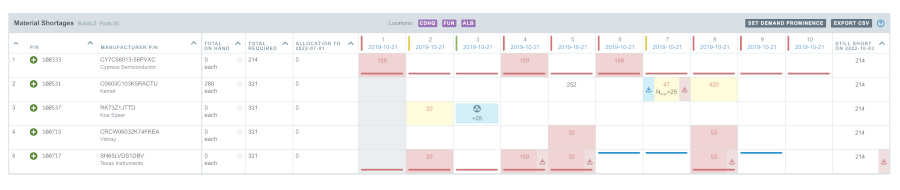
Detail the inventory levels of raw materials, components, and finished products required to support production. Identify reorder points and safety stock levels.
7. Production Capacity and Constraints
Describe the available production capacity for each production line or workstation. Identify any capacity constraints or bottlenecks that may affect production.
8. Lead Times
Specify lead times for materials and components to ensure they are ordered in advance of production needs. Include lead times for setup, changeovers, and transportation if applicable.
9. Quality Control Measures
Describe quality control checks and inspections to be conducted at various stages of production. Include acceptance criteria and procedures for addressing quality issues. Looking for ECM management? Check out Aligni MRP.
10. Maintenance and Downtime
Outline planned maintenance schedules for machinery and equipment. Specify procedures for addressing unexpected equipment breakdowns and minimizing downtime.
11. Packaging and Labeling
Provide details on how products will be packaged, labeled, and prepared for shipping. Include any special packaging requirements for specific customers or markets.
12. Contingency Plans
Develop contingency plans to address unexpected disruptions in the supply chain, production process, or market demand. Specify alternative suppliers, production facilities, or production methods, if available.
13. Communication and Reporting
Define communication channels and reporting structures for production-related issues. Specify who should be notified in case of production delays or quality problems.
14. Key Performance Indicators (KPIs)
Identify KPIs that will be used to measure the performance of the production plan, such as on-time delivery, production cycle time, and inventory turnover.
15. Document Control
Establish document control procedures to ensure that the production plan is kept up-to-date and that all stakeholders have access to the latest version.
16. Approval and Sign-off
Include a section for approvals and sign-offs by relevant parties, such as production managers, quality assurance teams, and senior management.
The right tools for the job
The above details constitute a very large amount of data to manage. Many firms start off by overseeing the production planning aspects though one or several spreadsheets. While this can be effective initially, as operations and demands grow, the tabular data format starts to buckle under the strain. When that happens, smart companies migrate to purpose built software to more effectively manage their data and operations. While large organizations utilize ERP systems, the software of choice for small to medium-sized manufacturers is usually a Materials Requirements Planning (MRP) system.
Manufacturing production plans are more effectively managed within material requirements planning systems compared to spreadsheets for several compelling reasons. MRP systems provide automation and integration, streamlining complex manufacturing planning tasks by automating calculations, scheduling, and procurement processes. In contrast, spreadsheets rely on manual data entry, making them less efficient and prone to errors.
Another significant advantage of MRP systems lies in their ability to operate in real-time, offering up-to-date insights into inventory levels, demand fluctuations, and production progress. Spreadsheets, on the other hand, often rely on static data, quickly becoming outdated which can lead to inaccurate planning decisions. MRP systems are also adept at handling the intricacies of manufacturing planning, such as multi-level Bill of Materials (BOMs) and lead time management, which can overwhelm spreadsheet-based approaches.
MRP systems provide resource optimization capabilities by considering production capacity and constraints when generating production plans. Spreadsheets typically lack these resource optimization features, which can result in less effective planning. Additionally, MRP systems offer enhanced collaboration among different departments, support alerts and notifications for exceptions, and ensure version control and data integrity. These features collectively make MRP systems the preferred choice for manufacturing production planning in both small and large-scale operations.
Bringing it all together
A well-detailed manufacturing production plan serves as a valuable reference document for everyone involved in the production process. It helps ensure that production activities are coordinated, resources are allocated efficiently, and products are manufactured according to the desired specifications and standards. For larger operations or more complex processes, doing the planning well necessitates using software designed for the task like an MRP system.
If you’re looking to get better command over your production processes, it’s best to start with the right software – Aligni MRP. Sign up today.
Start your 30-day free trial
Helping You Make Great Things…Better.