A Material Requirements Planning (MRP) system like Aligni is the hub of managing manufacturing operations. That includes being involved with the Engineering Change Management (ECM) process. Using an MRP system to help manage the process is the optimal approach for manufacturing because it ensures a seamless and coordinated response to the engineering changes across the organization.
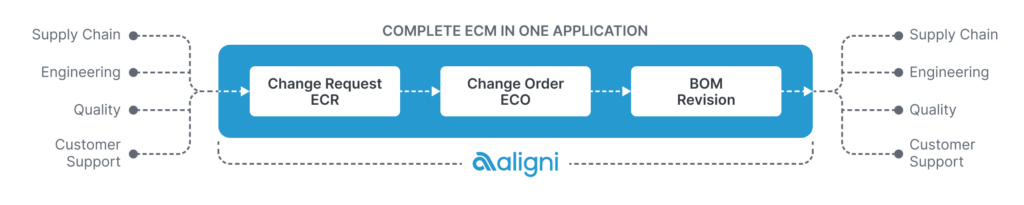
By integrating material planning and production scheduling with the ECM process, manufacturers can swiftly adapt to design modifications and improvements while maintaining operational efficiency. This results in reduced production delays, minimized material shortages, and improved product quality. These benefits ultimately enhance the competitiveness of the firm.
Looking specifically at how these systems integrate, an MRP system is used at certain steps in the ECM process during the manufacturing process. We’ve broken down where an MRP system is typically involved at different stages of the ECM process:
ECR Initiation
At the very beginning of the ECM process, when a change is proposed through an Engineering Change Request (ECR), the MRP system may not be directly involved. However, it indirectly plays a role in assessing the feasibility and potential material impact of the proposed change. For instance, if the change involves a new component or material, the MRP system can provide information on material availability and lead times.
With a system like Aligni MRP, the ECR process is integrated within the MRP software. This provides direct connection with the product requiring updating, as well as the parts and materials and the vendors that are used. When the process originates, the relevant personnel who manage each of these aspects are made aware of the situation.
ECR Review
During the impact analysis phase of the ECR review, the MRP system becomes more directly involved. It is used to help evaluate how the proposed change will affect material requirements, lead times, and production schedules. This analysis stemming from the MRP’s interconnectedness to the materials and departments who manage them is crucial for understanding the practical implications of the change on the manufacturing process.
ECR Approval
If the ECR is approved, it leads to the creation of an Engineering Change Order (ECO). A highly integrated MRP like Aligni also can manage this stage as well. The MRP can track the order and alert the necessary people to make the change permanent, as well as set into motion the actions needed to fulfill the order.
During this phase, the MRP system specifically plays a critical role in updating the BOM to reflect the approved changes accurately. This ensures that the manufacturing process uses the correct materials and components. Aligni goes further by communicating the change to supply chain personnel. This ensures the right components are ordered going forward.
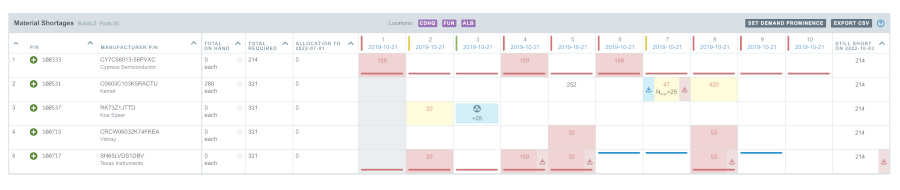
With changes to parts comes changes to material availability. These can impact the lead times for materials and components. The MRP system is responsible for updating lead times to account for any changes, ensuring that production scheduling remains accurate.
Although resource allocation and capacity planning are not typically managed directly by many MRP systems, Aligni MRP has the tools to manage the changes that result from the changes. It stores and provides the data that is essential for decision-makers to assess whether the manufacturing facilities have the capacity to handle the changes introduced through the ECM process.
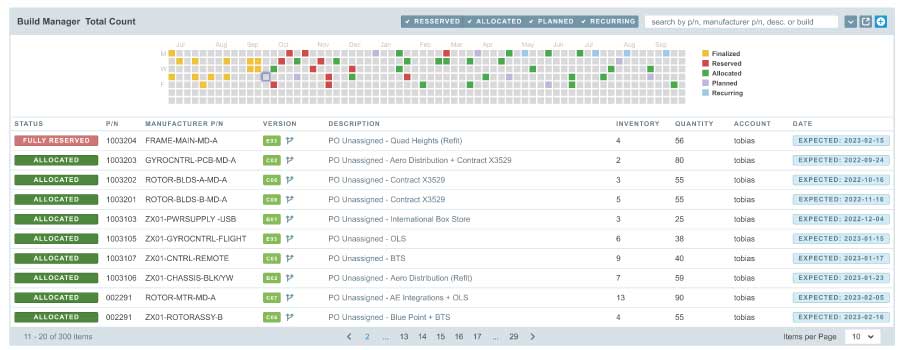
Once the ECO is approved, and the MRP system has been updated, production schedules are adjusted to incorporate the changes. The MRP system helps ensure that the shop floor operates according to the latest design and process modifications.
Aligni MRP provides this ability through its Build Manager, which performs the functions of a Master Production Schedule (MPS) for many organizations. Using this tool, manufacturers can understand what the changes mean for production as well as for supply chain functions.
Where Aligni MRP helps further
Having the right MRP system to help manage your ECM process can bring in even more resources to managing change. Where Aligni excels is bringing departments together and making data easily accessible.
Communication and Collaboration
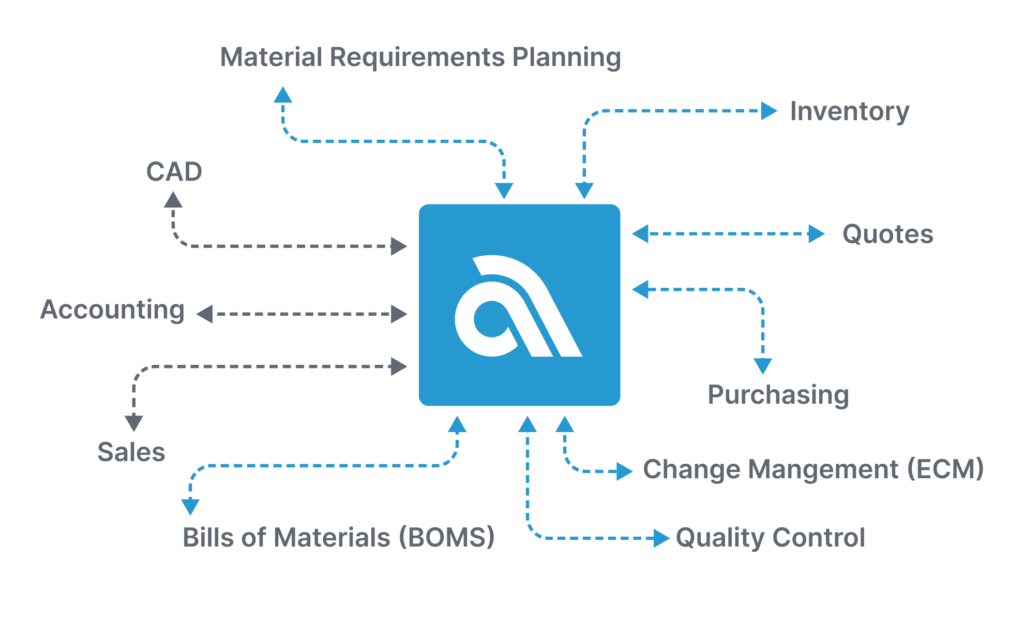
Throughout the ECM process, an advanced MRP system like Aligni enhances communication and collaboration between various departments involved in the change, including engineering, production, and procurement. It ensures that everyone has access to real-time data and that changes are implemented smoothly. This stems from Aligni’s structure that’s built from the ground up to be not only accessible for the departments in a manufacturing organization but also make their processes more efficient.
Aligni’s enhanced interdepartmental integration benefits also come from the software’s foundation being built upon an Item Master database. This foundation makes it easy to store and retrieve large quantities of information that manufacturers generate to more efficiently find insights and keep the organization up to date with the correct data.
Real-Time Updates
The Aligni MRP system provides several methods for alerting groups within the organization of changes. These capabilities allow manufacturers to monitor how engineering changes affect material requirements and production schedules in a more timely manner. This real-time visibility supports proactive decision-making and minimizes disruptions, as well as to provide the ability for greater agility as an organization.
Bringing it all together
When a firm is using the right MRP system, it streamlines multiple steps in the ECM process. primarily to ensure that material planning and production scheduling align with approved engineering changes, but an MRP like Aligni can provide a lot more benefit to a small and medium-sized manufacturer. It can track the process and play a vital role in assessing the impact of changes, updating material data, and maintaining production efficiency and product quality.
If you’re looking to facilitate a more substantial engineering change management process, then it’s a good time to consider making the transition to a material requirements planning system like Aligni MRP to properly manage ECOs, ECRs and the greater effects of product change within the production and supply chain processes. Sign up today for a 30-day free trial of Aligni MRP!
Start your 30-day free trial
Helping You Make Great Things…Better.