Moving a product from design and development to production may seem simple, but it’s really a complex process. There’s a lot of information that needs to be disseminated to several departments within the company. Or, that information needs to be packaged to send to external producers. Sometimes the product is perhaps a singular item, like a bracket or circuit board, things aren’t as complex. If it’s an assembly of components, each with their own production processes and specifications, managing all the data and where it needs to go can become a nightmare.
When it comes to managing hand-offs of complex products, successful firms turn to software purposely built to handle all the steps and intricacies. That software is Product Lifecycle Management (PLM). Systems like Aligni PLM are the information repositories designed to not only safeguard and revision control the files and specifications, but to make it easy to share that information to other departments including production, purchasing, inventory and quality. This sharing may also include vendors who provide components or a portion of the production process.
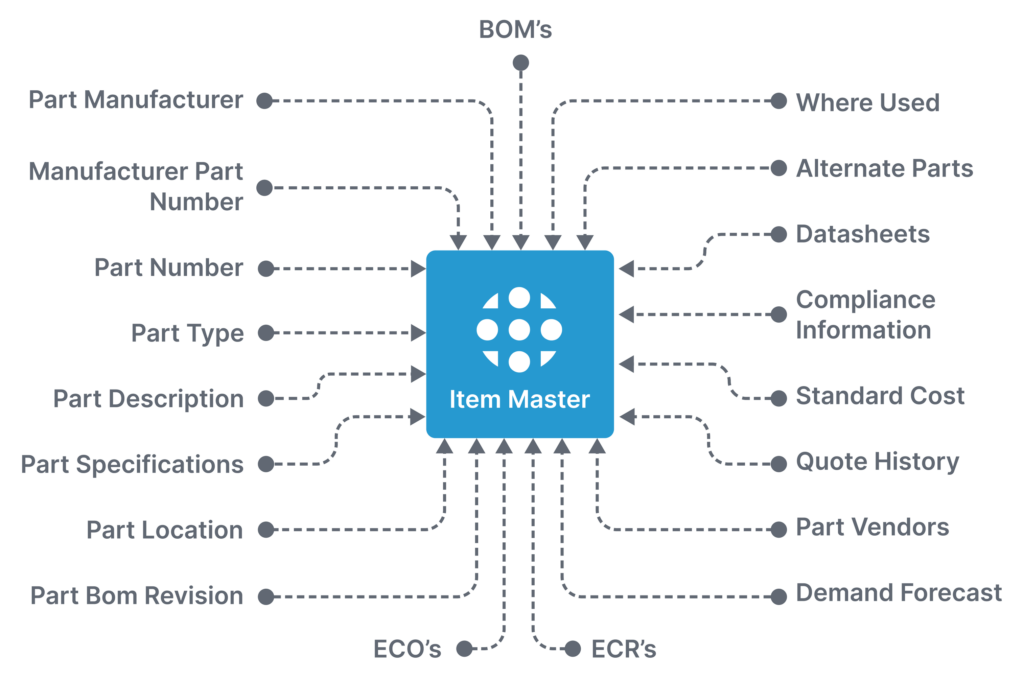
During the handoff process, the product development department typically provides a variety of product information and files to ensure accurate and efficient production. They do this by moving the production-intent version of the product into the PLM’s item master database. Later on, the PLM system becomes the collection point for any changes to the product or the parts that make it up. This makes it available to the people who need it, as well as making sure there’s only one location where the files are kept. This ‘single source of truth’ reduces errors and old information from causing issues.
What Information PLM systems Manage
The specific documents and files may vary depending on the organization and product, but here are some common types managed by product lifecycle management systems during the development, manufacturing and stages beyond:
1. Engineering drawings: These are detailed drawings that illustrate the product’s dimensions, specifications, and tolerances. They provide a visual representation of the product’s components, assembly, and manufacturing requirements. When it’s time to move the product into production, these files are transferred out of a company’s PDM system into PLM for distribution. If the product has been developed across several design software systems, like those that specialize in mechanical, hydraulic or electrical design, this is when all those files are combined into one location.
2. Bills of Materials (BOMs): BOMs list all the materials, components, and sub-assemblies required to manufacture the product. They include part numbers, descriptions, quantities, and sometimes supplier information. BOMs ensure that the manufacturing team has a complete understanding of the necessary parts for production.
3. Assembly instructions: These instructions guide the manufacturing team through the step-by-step process of assembling the product. They include detailed descriptions, diagrams, and possibly images or videos to clarify the assembly process.
4. Manufacturing specifications: These specifications outline the specific production processes, techniques, and equipment to be used. They may include details on machining, molding, assembly techniques, surface finishing, and any other critical manufacturing operations.
5. Quality control standards: The product development department provides information on the quality standards that need to be met during production. This includes specifications for dimensions, tolerances, performance criteria, and any testing or inspection requirements to ensure product quality.
6. Test and validation documentation: This includes any test plans, test procedures, and test results from the product development phase. It provides insight into the product’s performance, functionality, and reliability, helping the manufacturing team understand critical test requirements and ensure consistency in production.
7. Material specifications and samples: The product development department may provide specifications for the materials and finishes used in the product, such as metal alloys, plastics, coatings, or adhesives. They may also note actual material samples to serve as references for the manufacturing team.
8. Packaging and labeling requirements: If applicable, the product development department provides guidelines for packaging and labeling the final product. This includes details on packaging materials, dimensions, labeling content, and any legal or regulatory requirements.
9. Compliance and regulatory documentation: If the product needs to meet specific regulatory standards or certifications, the product development department provides the necessary documentation and guidance to ensure compliance. This may include safety certifications, environmental regulations, or industry-specific standards.
Bringing it all together
By managing these comprehensive product information and files within a PLM system like Aligni, the product development department enables the manufacturing team to understand the product design, materials, assembly processes, quality requirements, and any other critical aspects needed to produce the product accurately and efficiently. They also create a collaborative environment where changes can be made and all involved are notified of the changes, as well as making sure everyone is working off the same files.
If you’re looking to make the transition from product design to production more streamlined, it’s time to sign up online for Aligni PLM today!
Start your 30-day free trial
Helping You Make Great Things…Better.