When sourcing anything from components to contract manufacturing, properly managing product data is paramount to reducing errors, maintaining quality, controlling costs, and hitting delivery dates. That all starts with the quality of the product’s Bill of Material (BOM). But it extends into how that BOM is maintained and shared among stakeholders. Doing so inside an organization is difficult. Sharing it with suppliers and contract manufacturers makes it even more demanding.
The Common Pitfalls in Sharing BOMs
From a product engineer’s perspective, navigating the challenges associated with sharing bills of materials with vendors requires a strategic approach. One concern is maintaining effective version control. A product engineer needs to ensure the vendor receives the latest version of the BOM. Its receipt is vital to avoid discrepancies and potential production errors. Implementing a robust versioning system and promptly communicating any changes in design or specifications is essential to making sure everyone is working off of the current revision level.
Data accuracy is another issue that arises when sharing bills of materials. It’s important to meticulously review and verify the information within the BOM to prevent errors that could compromise the quality of the final product. Providing detailed documentation alongside the BOM, including specifications, drawings, and any relevant notes, serves as a means to offer comprehensive guidance and minimize the risk of misinterpretation.
Communication challenges can arise due to complex technical details within the BOM. Bridging the gap between technical details and vendor understanding is a responsibility for the product engineer. Encouraging open lines of communication and facilitating clear and concise explanations can mitigate misunderstandings and promote a collaborative working relationship.
Addressing component availability and substitutions is also a concern. Product engineers must be proactive in communicating potential changes in materials or components and work closely with vendors to assess the impact on the final product. This involves a keen awareness of market trends, potential shortages, and the ability to suggest viable alternatives.
Finally, from a product engineer’s perspective, integrating technological solutions such as collaboration platforms or PLM systems can streamline the process. These tools facilitate real-time updates, centralized information access, and automated communication, reducing the likelihood of errors and enhancing overall efficiency in sharing BOMs with vendors.
Ironing out the Issues
Reducing issues associated with sharing bills of materials with vendors involves implementing a series of strategic measures. Firstly, establishing clear communication channels is essential for fostering effective dialogue between the manufacturer and vendors. Standardizing the format of BOMs can enhance compatibility and decrease the likelihood of errors during data transfer. Implementing a robust version control system ensures that both parties are working with the most up-to-date information. It also minimizes the risk of discrepancies.
Encouraging collaboration is another crucial aspect. Involving vendors early in the design and planning stages helps address potential issues proactively. The use of collaboration platforms like Aligni’s vendor portal or project management tools can facilitate real-time sharing and updating of BOM information, particularly if they are cloud-based, promoting seamless collaboration.
Addressing language and cultural differences, especially in international collaborations, is vital. Clear documentation accompanying the BOM, including specifications, drawings, and notes, enhances understanding and reduces the possibility of misinterpretation. Ensuring secure data transfer through encrypted channels and digital rights management tools protects sensitive information during the sharing process.
Finally, establishing clear terms and agreements regarding responsibilities and expectations sets a solid foundation for collaboration. By collectively implementing these measures, manufacturers and vendors can streamline the sharing of BOMs, creating a more efficient and error-resistant process within the production and supply chain.
Getting BOM Help with a PLM System
A Product Lifecycle Management (PLM) system like Aligni’s PLM software can significantly reduce various issues associated with sharing Bills of Materials information with vendors. Here’s how:
PLM Systems Provide Centralized Data Management
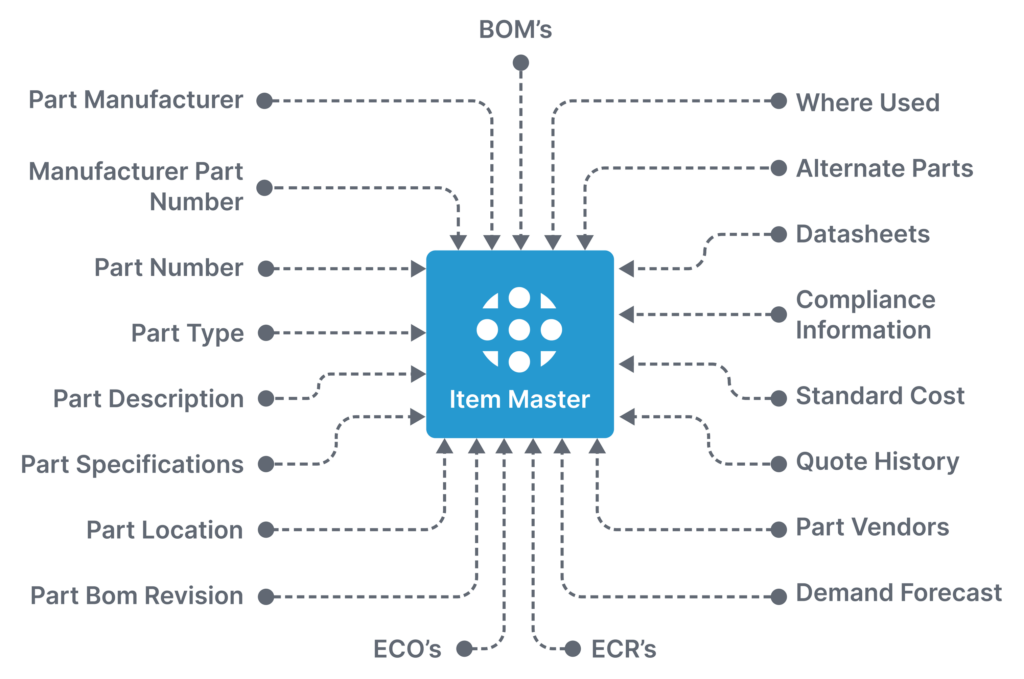
These systems provide a singular repository for bills of materials and their associated data, ensuring that all stakeholders, including vendors, have access to a single, authoritative source of information. This helps eliminate version control issues by ensuring that everyone is working with the most up to date BOM.
Providing Real-Time Collaboration
PLM systems allow multiple users, including product engineers and vendors, to work on BOMs simultaneously. This reduces delays in communication, promotes transparency, and ensures that changes are instantly visible to all relevant parties.
Integrating Change Management Processes
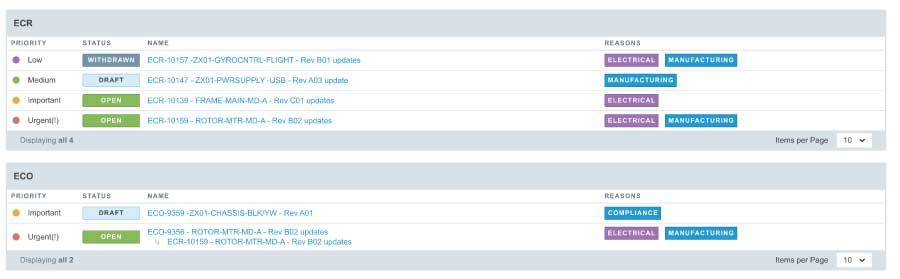
PLM systems typically include robust change management functionality. This allows product engineers to document and track changes made to the BOM, providing a clear audit trail. Vendors are immediately informed of any alterations, reducing the risk of misunderstandings and errors.
Streamlined Workflows
PLM systems can help automate workflows related to BOM sharing and approval processes. Automated notifications and alerts ensure that all stakeholders are promptly informed of pending actions, streamlining communication and reducing the likelihood of missed updates.
Integrated Documentation
These systems often integrate with document management modules, while some PLM systems provide their own abilities to connect stored data to bills of materials. This enables product engineers to attach detailed documentation, specifications, drawings, and notes directly to the BOM. Vendors can access this information seamlessly, reducing the risk of misinterpretation and ensuring comprehensive understanding.
Offering Supplier Collaboration Portals
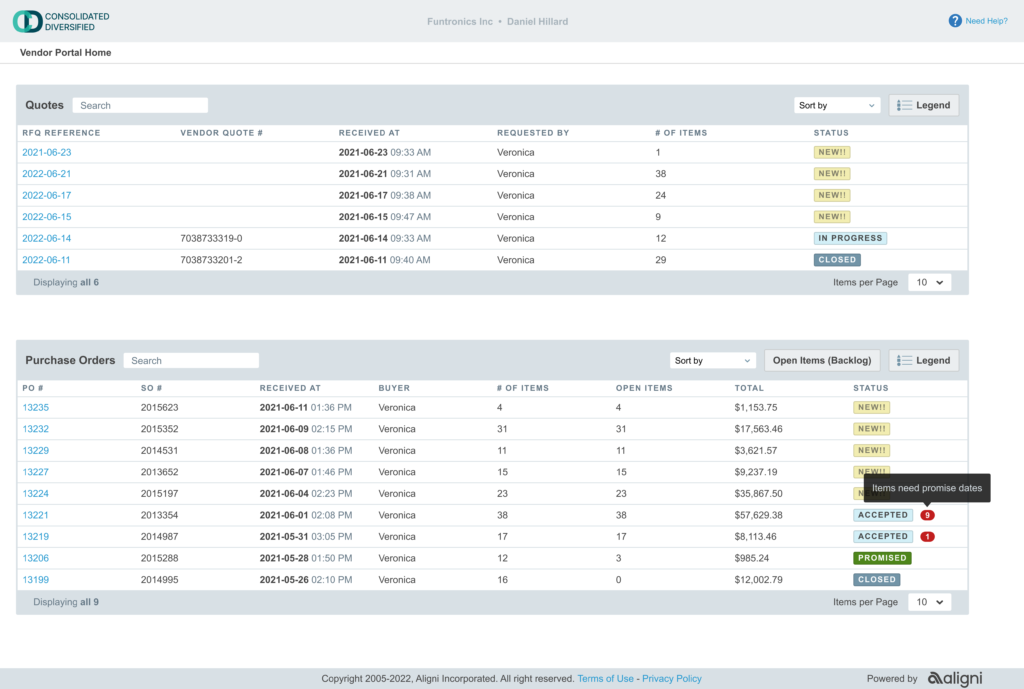
Many PLM systems, and especially Aligni PLM, offer supplier collaboration portals. These secure platforms allow vendors to access relevant BOM information without the need for direct communication. This promotes self-service and empowers vendors to stay informed about changes and updates.
Comprehensive Traceability
PLM systems provide comprehensive traceability features, allowing product engineers to track components, materials, and changes throughout the entire product lifecycle. This is essential for regulatory compliance and ensures that vendors have visibility into the entire history of the BOM.
Greater Data Security
Access controls and permissions ensure that sensitive information is shared only with authorized individuals to help PLM systems prioritize data security. This addresses concerns related to confidentiality and protects intellectual property when sharing BOMs with vendors.
Providing Analytics and Reporting
PLM systems provide analytics and reporting capabilities that allow product engineers to analyze BOM-related data. This insight can be valuable for identifying trends, optimizing processes, and addressing potential issues before they escalate.
Bringing It All Together
When it comes to moving bills of materials out of development and into production, a PLM system serves as a comprehensive solution to reducing errors in BOM management and collaboration with vendors. By addressing version control, promoting real-time collaboration, automating workflows, and ensuring data security, PLM systems contribute significantly to reducing issues and improving the overall efficiency of the BOM sharing process.
If you’re looking to streamline your vendor communication and information management, it’s time to move up to a software solution designed to perform this process. It’s time to sign up for Aligni PLM.
Start your 30-day free trial
Helping You Make Great Things…Better.