MRP
Aligni for Supply Chain Managers
Oversight of part and material needs is a complex operation. While it’s easy to think it is simply a matter of matching production needs to orders, executing well means going much deeper. Aligni is designed to help manage those depths for buyers and purchasing departments.
Here, we step through the supply chain management process to outline how Aligni streamlines the part procurement process.
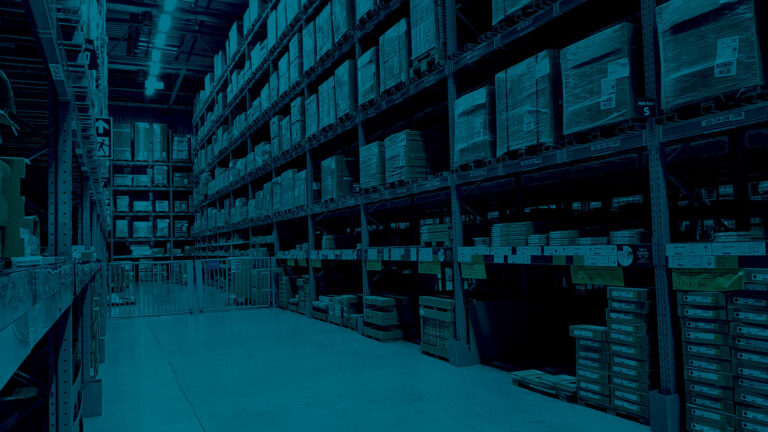
Knowing What’s On-Hand
At its heart, Aligni is a Materials Requirements Planning system. That means it’s been designed to manage inventory and do it at a high level of competency. This capability provides supply chain managers the ability to completely understand the quantities on-hand, as well as the consumption and replenishment of those parts and materials over time. Aligni can do this efficiently whether the company is managing 80 parts or 8000 parts. Its efficiency comes from Aligni’s item master database foundation and the interfaces designed specifically to access that information.
For each part, assembly or product in the system, Aligni renders a dashboard that explains the current condition of the inventory considered and some of the forces acting upon that condition. Going further, Aligni streamlines that information into charts that provide a faster read into these states, like the Inventory Outlook chart, below.
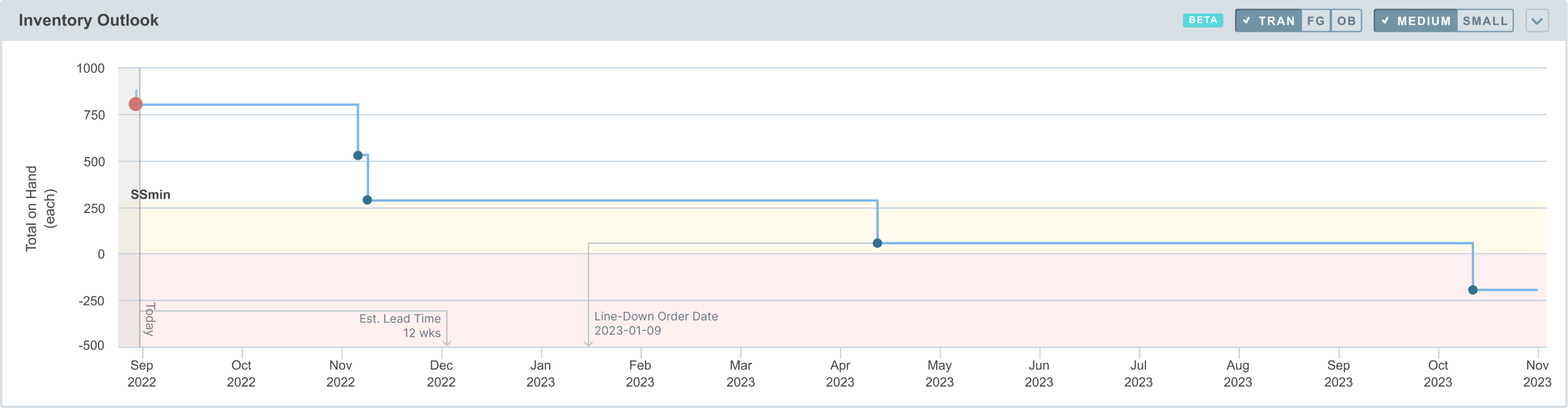
This chart explains the quantity of material available over time, dates where amounts are consumed, and expected dates when new inventory will arrive. The chart displays previously determined safety stock levels that have to be maintained, as well as pre-set re-order lead times for each part. The chart and the data the dashboard displays helps supply chain managers extract insights from the flood of data they process to make better decisions.
Learn more about Aligni’s stock management tools
Plan for What’s Needed in the Future.
Aligni MRP equips supply chain managers with powerful tools to take a more proactive approach in managing purchasing activities for discrete manufacturing operations. One of the key features is the Material Shortage Report (MSR), which offers a clear, at-a-glance overview of the near-term part and material requirements for every production build in the system. This enables managers to quickly assess which parts are needed to ensure timely production and avoid any potential delays.
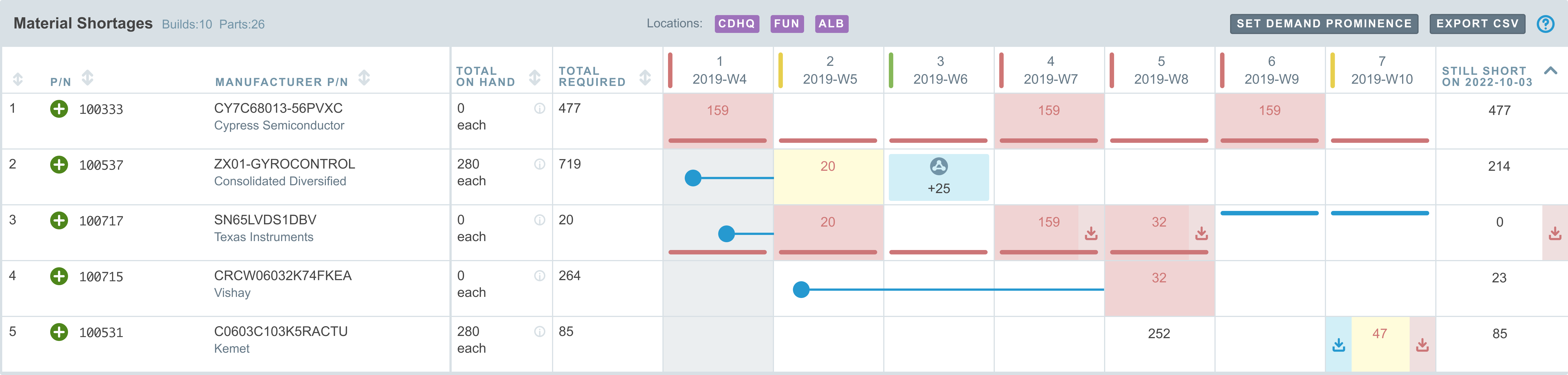
The MSR’s color-coded indicators provide an intuitive view of the status of all builds, showing which are ready for production and which are held up due to insufficient inventory. It also highlights the lead times required to procure necessary materials, giving supply chain managers a clear understanding of when to initiate purchasing activities. With this visibility, managers can better plan and negotiate with suppliers, reducing the likelihood of stockouts and production line stoppages. This enhanced insight helps streamline purchasing, improve supplier relationships, and ultimately reduce costs while ensuring smooth production flow.
Learn More about Aligni’s Material Shortage Report
Purchasing and Vendor Management in One System
Manage All RFQs from One Screen
When buyers utilize the built-in ActiveQuote capabilities, they not only see current quotes in process and their status – they can sort these by date created and by whom. Further, the quote view can be filtered by which stage of the process the quotes are in within Aligni. Buyers may choose to view only drafts, pending, open, or closed quotes – all within the Supply Chain dashboard pictured in the header at the top of the page.
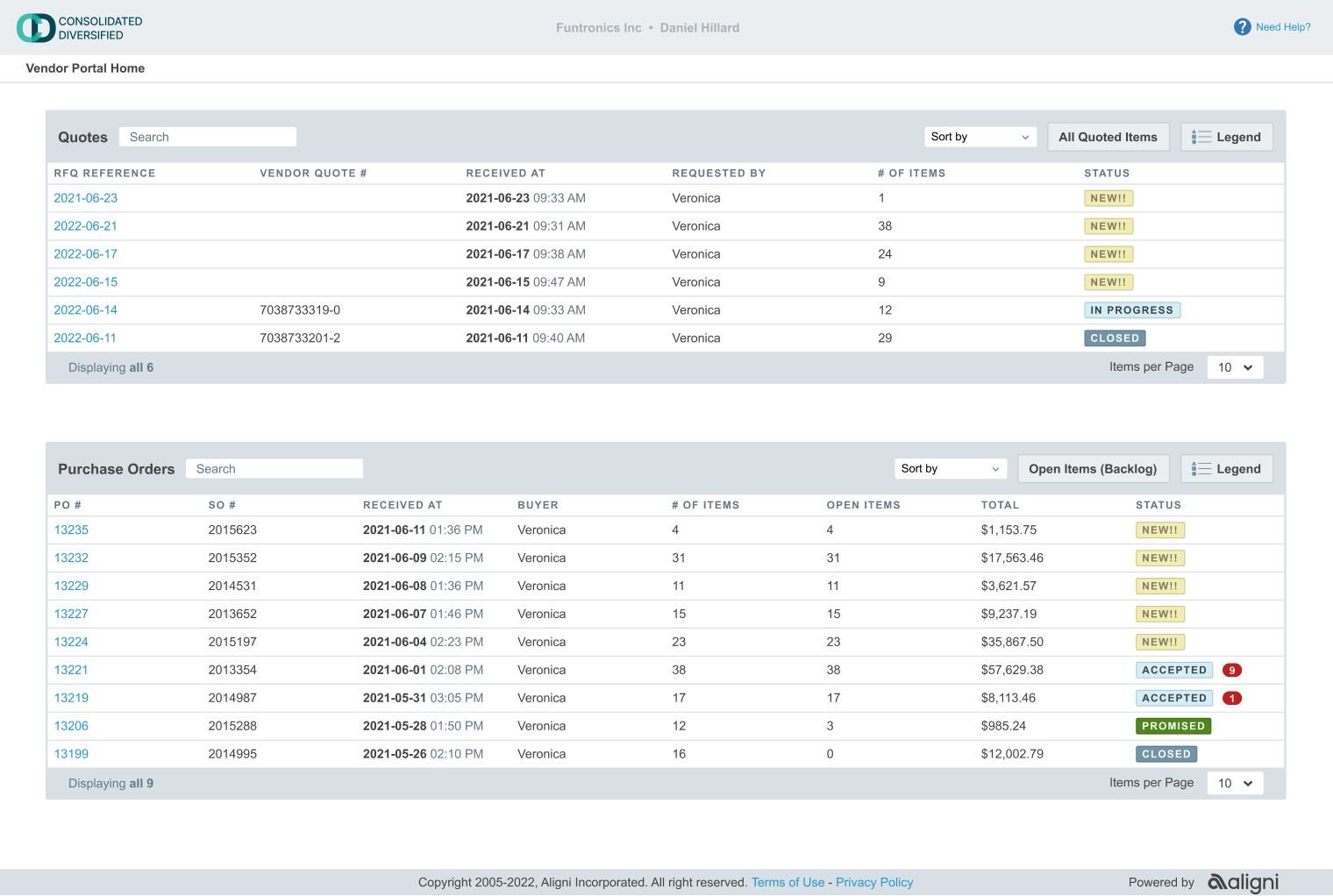
Track Purchases
Aligni also follows purchase orders and their process all the way to material receipt at the company’s facility. On the Supply Chain Dashboard, buyers can see all purchases, their issue date, the vendor, and the current status. Purchase order filtration operates in the same fashion as what can be done with quotes.
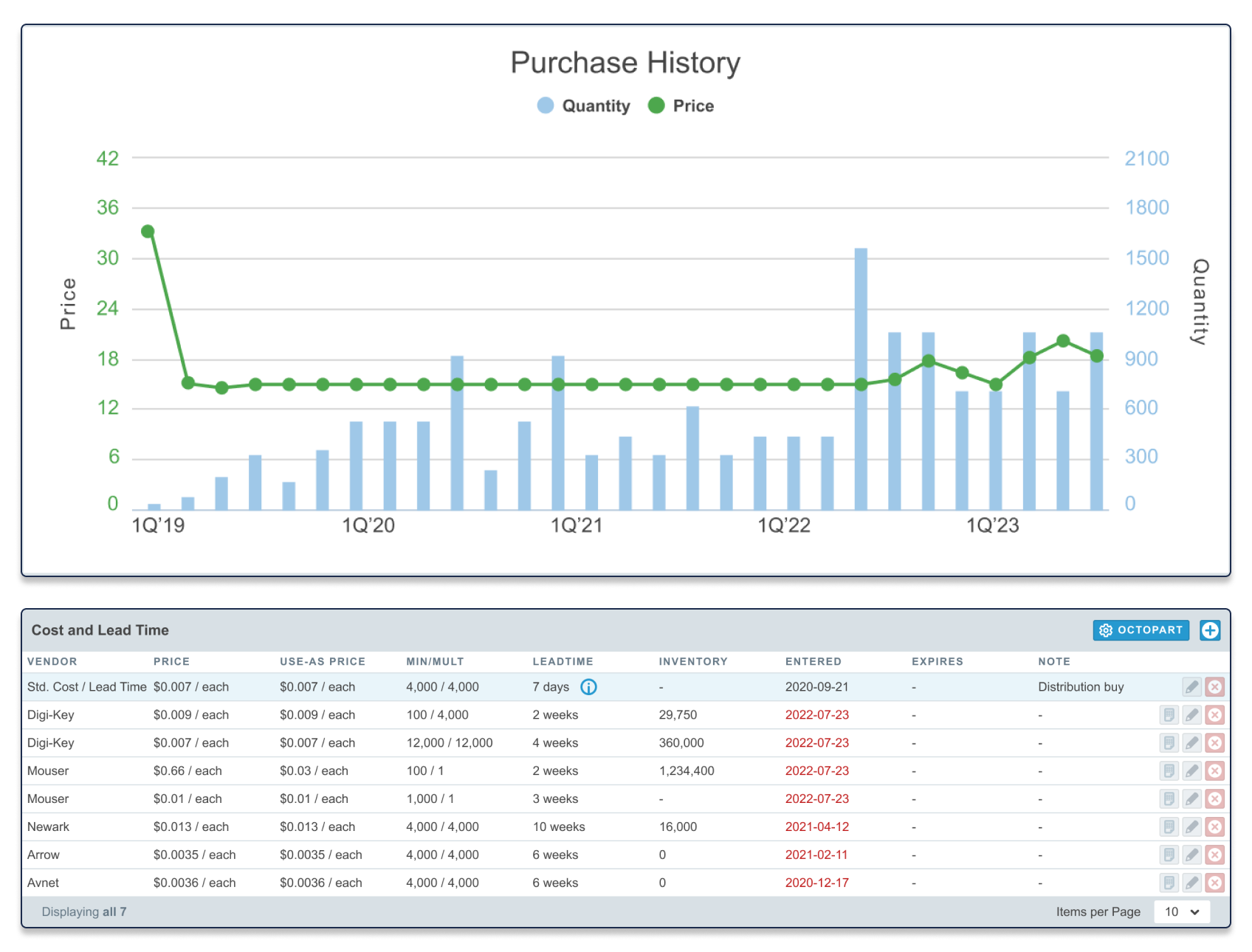
Connect Quotes and Orders to Production
At Aligni, we know that purchasing operations and manufacturing don’t happen in a vacuum. The Builds section of the Supply Chain Dashboard connects the buying operations to the needs of the shop floor. That’s why we’ve integrated the purchasing process with the management of inventory in Aligni MRP.
Builds are production orders, batches, or jobs scheduled for manufacturing in the system. The Build Manager section of the Aligni’s Supply Chain Dashboard visualizes the procurement operations in relation to the shop floor production schedule. This section line-lists the needs of production and whether the materials are allocated, reserved, or need to be requisitioned. It provides supply chain managers an overview into upcoming builds and their readiness for production and it’s the same information production managers view when managing operations. When both departments are working together from the same data, everyone wins.
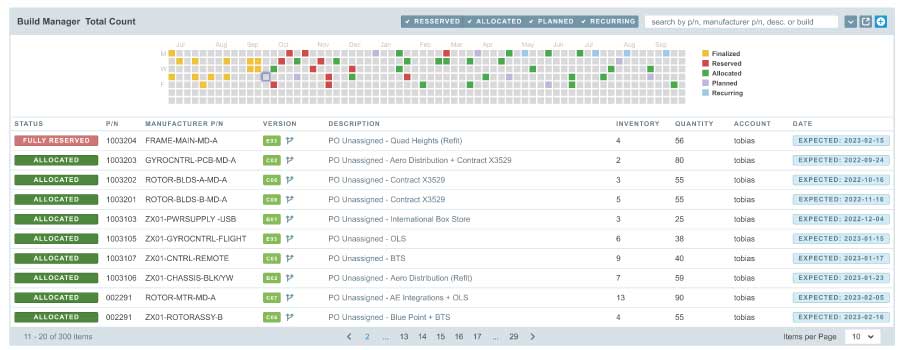
Learn more about purchasing management and Aligni’s Vendor Portal
Explore what Aligni can do for your organization
Learn More About Aligni
These aspects are just a few of the capabilities Aligni’s Supply Chain Dashboard provides to buyers and purchasing managers. Learn more about how Aligni can help you handle safety stock, manage inventory time lines and streamline supply chain operations.
Sign up today or try the demo to get a deeper understanding of what Aligni MRP can do to enhance your supply chain operations!