Aligni for Purchasing Managers
Aligni MRP empowers purchasing managers to take a proactive and strategic approach to inventory and procurement.
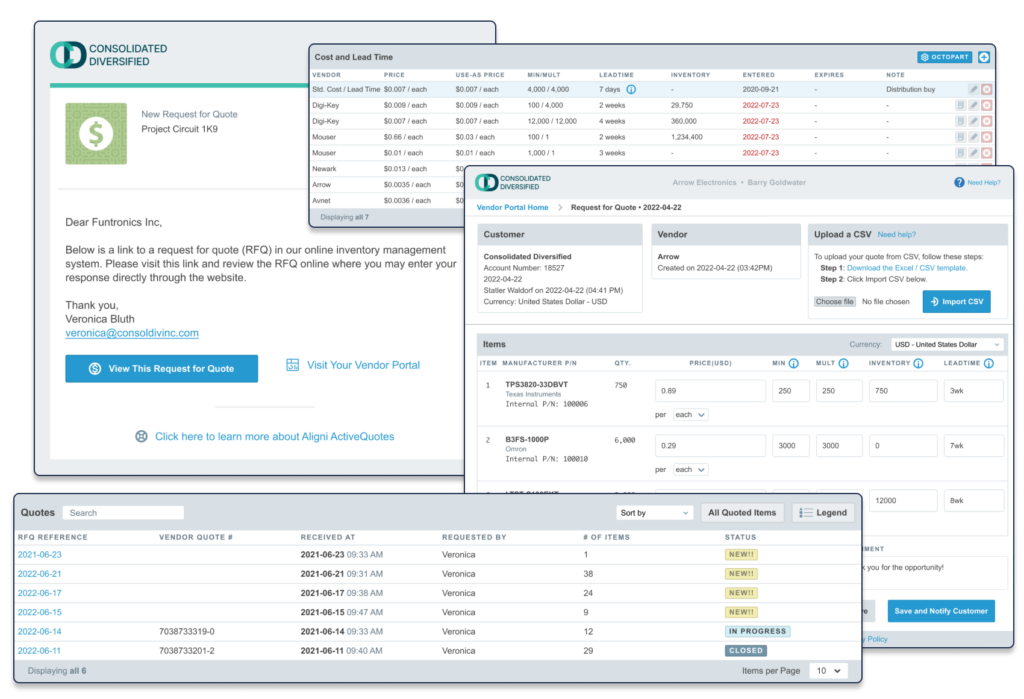
Aligni is a robust Materials Requirements Planning (MRP) system, purpose-built to manage inventory with exceptional efficiency and precision. Designed to support inventory and production management activities in small and mid-sized businesses, Aligni provides comprehensive visibility into on-hand quantities, consumption rates, and replenishment timelines for parts and materials. Aligni’s performance remains unparalleled thanks to its powerful item master database and intuitive, purpose-designed interfaces.
Manage In-Stock Inventory
Aligni MRP is the central hub for managing inventory quantities. With real-time updates, purchasing managers gain instant visibility into changes in inventory levels, enabling you to respond proactively to evolving needs and challenges.
One of Aligni’s standout features is the Inventory Outlook Chart, which provides a clear, time-based representation of material availability. It highlights consumption trends, anticipated replenishment dates, and adherence to pre-defined safety stock levels and reorder lead times. This data, combined with Aligni’s intuitive dashboards, turns complex information into actionable insights, enabling you to make informed, data-driven decisions quickly, and with confidence.

By providing the ability to set and manage safety stock thresholds, Aligni helps managers safeguard against stockouts, ensuring production continuity even during demand fluctuations. At the same time, overstock limits can be established to prevent excess purchasing and reduce unnecessary costs, while reorder deadlines ensure that materials arrive before inventory levels become critically low.
Understand Production Material Requirements to Plan Purchases
Another key feature of Aligni MRP is the Material Shortage Report (MSR). This sophisticated tool provides a concise, real-time snapshot of all near-term material and part requirements across production builds. By delivering clear insights, the MSR enables you to quickly identify and address potential shortages, ensuring timely production readiness.
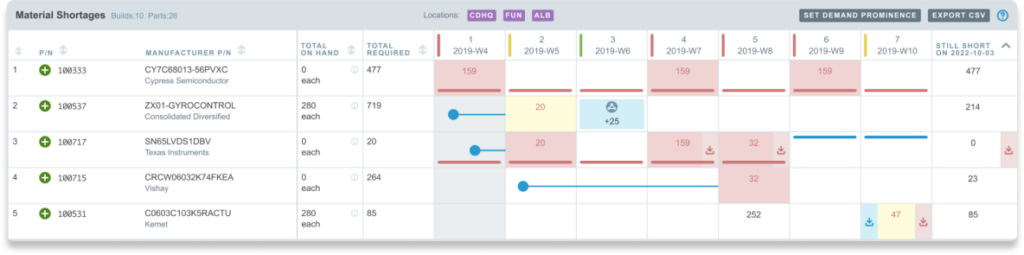
The MSR’s color-coded indicators offer an at-a-glance view of build statuses, clearly distinguishing between those ready for production and those awaiting inventory. It also highlights critical procurement lead times, for making informed purchasing decisions.
Improve supplier coordination, mitigate the risk of stockouts, and optimize cost management with enhanced visibility into inventory needs and procurement schedules. Aligni MRP transforms purchasing processes into a competitive advantage, driving efficiency, strengthening supplier relationships, and supporting uninterrupted production.
Create RFQs and Orders In App
Aligni simplifies the creation of RFQs (Requests for Quotes) and orders by directly utilizing build requirements stored within the system. This integration minimizes translation errors and ensures no orders are overlooked. Purchasing managers can efficiently compile all required parts and quantities from BOMs (Bills of Materials), build records, and part inventory pages to generate accurate RFQs and purchase orders. When building orders, Aligni generates vendor-specific purchase orders based on the requested parts identified in BOMs and builds, streamlining the procurement process.
For repeat orders, Aligni allows users to revisit older builds and BOMs to reorder parts in the correct quantities.. Managers can then adjust these older BOMs and builds to the new order quantities required. Aligni adjusts the individual part needs to match the overall order amount.
Aligni’s innovative “Part Cart” lets you create RFQs and Purchase Orders as quickly as ordering items from an online store. Visit any existing item list (e.g. previous builds, assembly BOMs, or even other POs and RFQs), add the items to your cart, and make any necessary adjustments.
Supporting documentation for these orders, including specifications and requirements, is securely stored in Aligni’s item master database. The product information can be securely shared through Aligni’s Vault capability, all without leaving the system, ensuring that purchasing managers can easily provide comprehensive, accurate details directly with suppliers to facilitate efficient and accurate quoting.
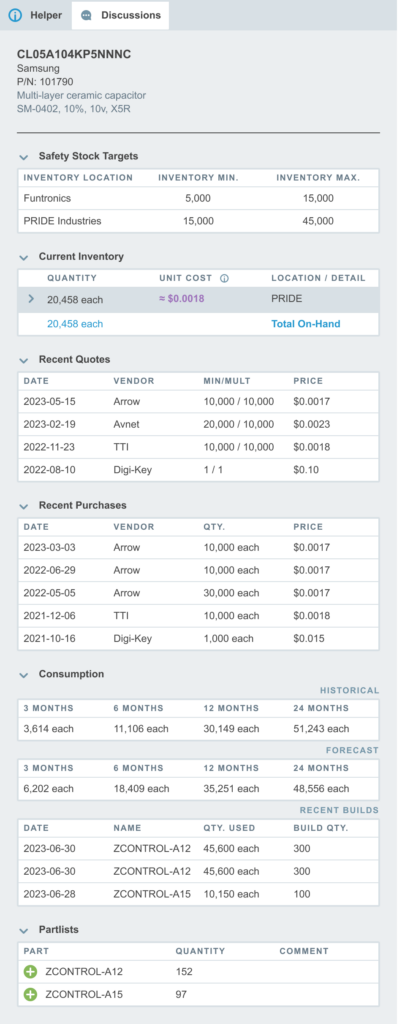
Effectively Manage Orders and Vendors
With Aligni, you gain a centralized, efficient approach to managing RFQs and orders, reducing errors, saving time, and strengthening supplier collaboration.
Streamline Vendor Communication and Quoting with Aligni ActiveQuote
Aligni’s ActiveQuote functionality enables purchasing managers to send RFQs and purchase orders directly from within the platform, eliminating the inefficiencies of transferring information between systems and email. All critical aspects of vendor communication are tracked and organized, with the details presented in a clear, centralized dashboard for easy access and review.
ActiveQuote provides purchasing managers with real-time visibility into the status of quotes in process. Users can sort quotes by creation date, originator, or stage in the procurement workflow. The dashboard allows filtering to display only drafts, pending, open, or closed quotes, enabling a streamlined approach to managing active quotes.
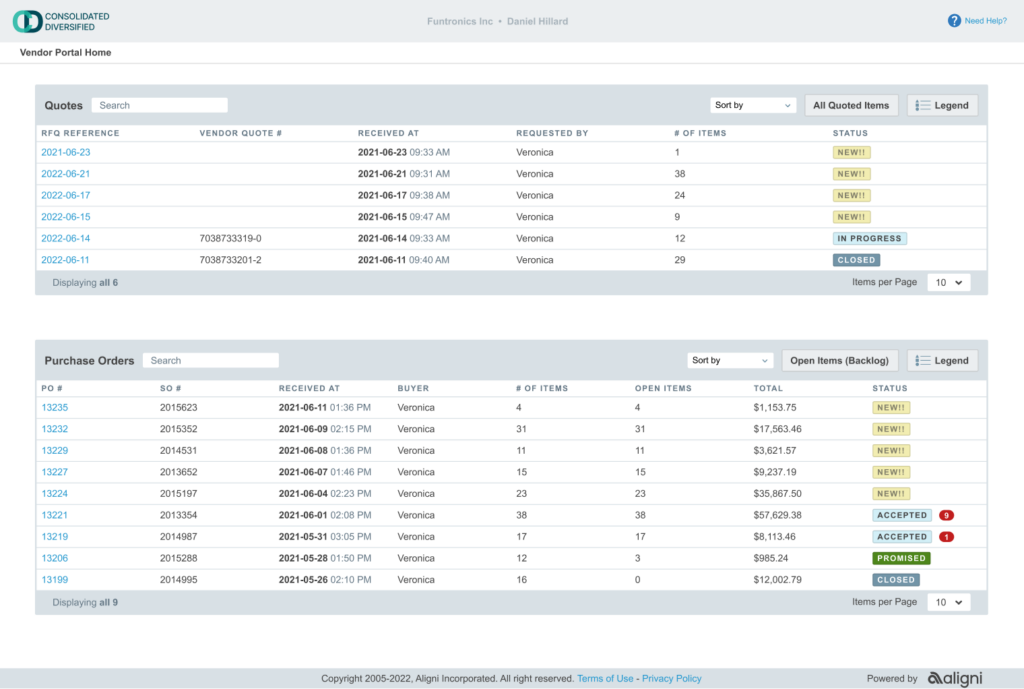
Consolidate vendor communication and quote tracking within Aligni’s Supply Chain dashboard and efficiently manage your processes, ensure transparency, and maintain control over procurement activities, saving time and enhancing operational accuracy.
Track Purchase Orders from Issuance to Receipt with Aligni
Aligni ensures complete visibility into purchase orders, tracking their progress from issuance to material receipt at your facility. Through the Supply Chain Dashboard, purchasing managers can monitor all purchases, including issue dates, vendors, and current statuses, in one centralized location.
The dashboard’s purchase order tracking features mirror the filtration capabilities of the quoting system, allowing users to sort and filter purchase orders by various criteria, such as status or vendor. This provides purchasing managers with a streamlined and efficient way to manage active and completed orders.
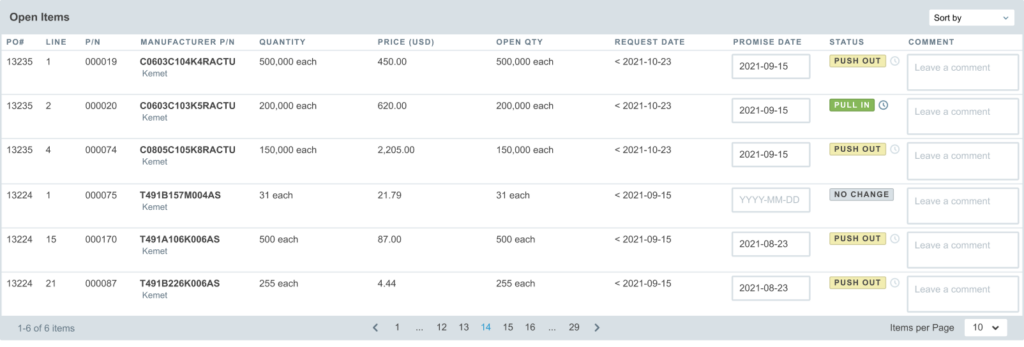
When paired with ActiveQuote’s functionality, which allows vendors to directly update delivery information, Aligni offers a dynamic, real-time overview of order statuses. This centralized and continuously updated system empowers businesses to assess orders accurately and plan effectively, even in the face of changing circumstances.
With Aligni, you can optimize procurement workflows, improve vendor collaboration, and ensure operational continuity with minimal effort.
Leverage Purchase History with Aligni for Strategic Purchasing
Aligni maintains a comprehensive record of past purchases, providing purchasing managers with easy access to valuable data for analysis and strategic decision-making. By reviewing historical trends, managers can make informed choices and refine their buying strategies to optimize costs and streamline operations.
The platform allows users to track price changes over time, offering insights into market trends and enabling proactive adjustments to purchasing plans. Additionally, Aligni supports the analysis of purchase price relative to order volume, helping you determine the most cost-effective order frequencies and evaluate the benefits of bulk purchasing.
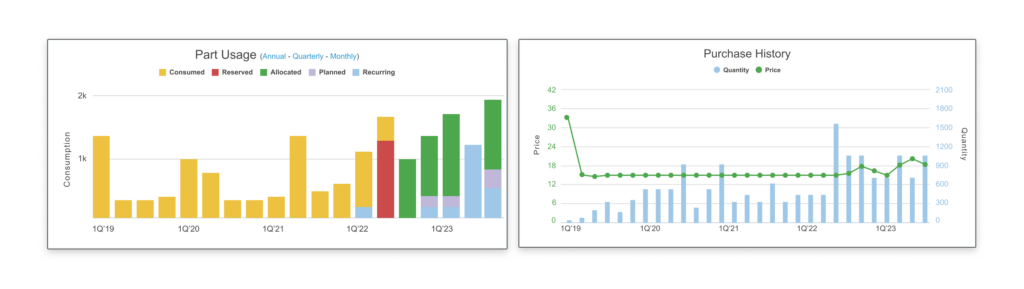
Aligni also provides the ability to review prior orders, including delivery timelines, enabling managers to develop more accurate and reliable lead time estimates for each vendor. Over time, these insights contribute to a comprehensive evaluation of vendor performance, helping businesses build stronger, more dependable supplier relationships.
Set Alerts and Collect Insight From Others in the Organization
With Aligni MRP, purchasing managers can navigate changing environments with confidence, leveraging real-time insights and collaborative tools to keep production on track and aligned with organizational goals.
Aligni features customizable alerts that notify managers when critical conditions arise, such as inventory shortages or low safety stock levels. These alerts also extend to change management activities, ensuring production managers are promptly informed of developments that could impact operational workflows.
To further enhance communication and collaboration, Aligni’s DiscussAnywhere feature allows managers to engage directly in discussions about changes, gain clarity on their implications, and ask essential questions. By fostering transparency and cross-departmental collaboration, Algini empowers you to proactively address potential issues, ensuring that operations remain efficient and uninterrupted.
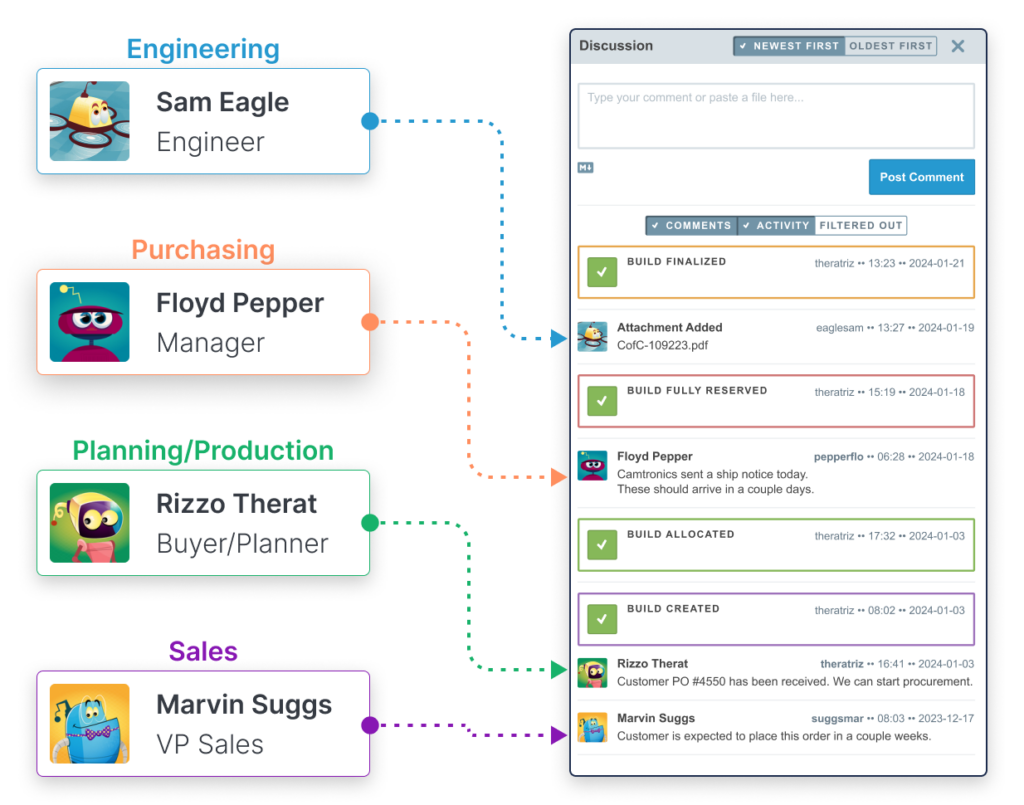
Explore what Aligni can do for your organization
Learn More About Aligni
These features represent just a fraction of the powerful capabilities Aligni MRP offers to purchasing managers and buyers. Explore how Aligni can help you effectively manage safety stock, optimize inventory timelines, and streamline your purchasing operations.
Take the next step toward smarter procurement—sign up today or try our interactive demo to see firsthand how Aligni MRP can transform your supply chain management and drive operational excellence.
Start your 30-day free trial
Join over 4,000 teams that are managing their manufacturing with Aligni.